MK Products Advanced Color Logic User Manual
Page 17
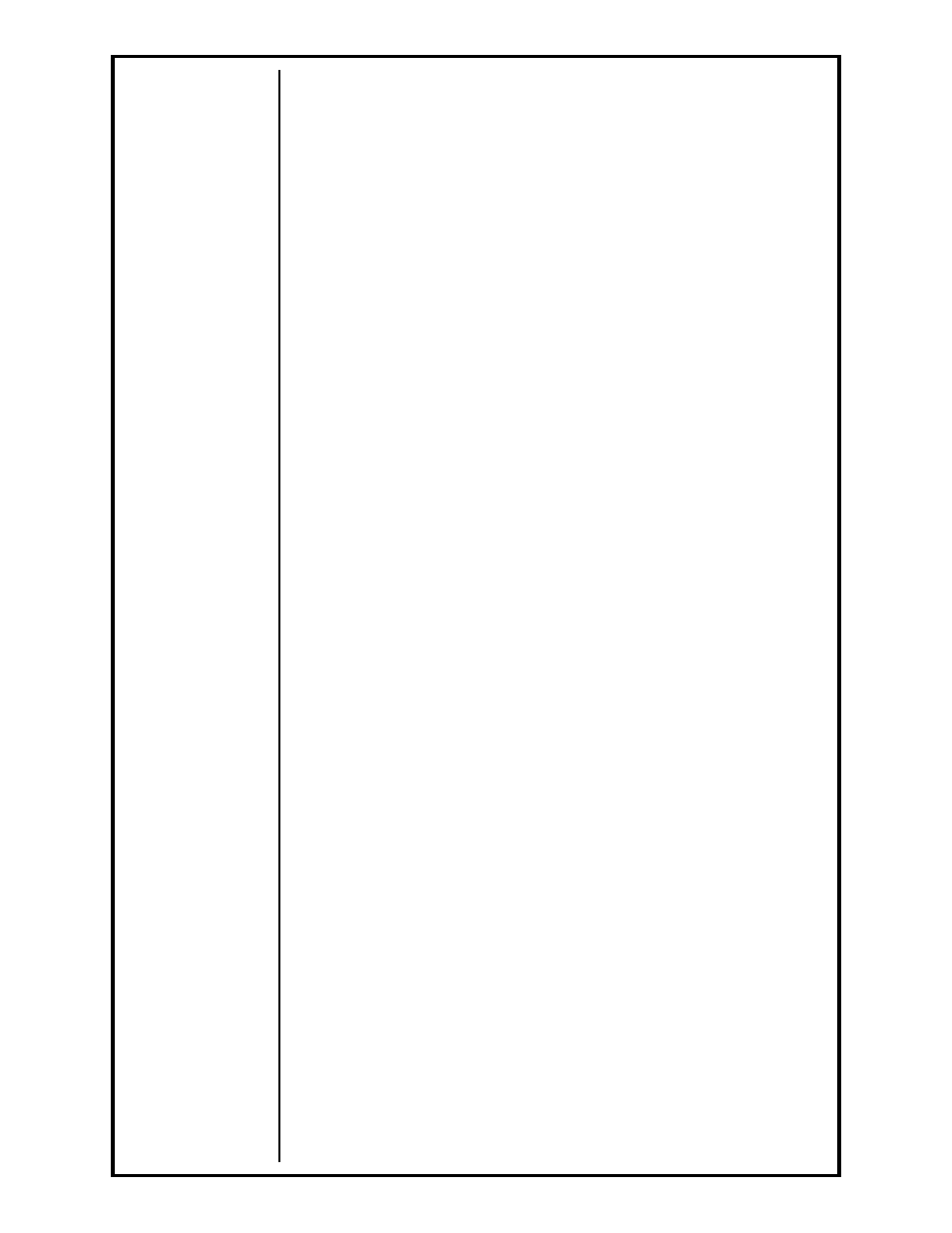
Advanced Color Logic Owner’s Manual - Page 10
not required, the operator could leave these lines blank if he chooses,
they are to help identify and describe each and every procedure. They
will not affect the operational ability or performance function of the weld
procedure, but they will show on all printouts.
Pressing [ENTER] will move the cursor box to the next line, top to bottom,
accepting either a blank line or the typed information. Once all the lines
are filled, or entered and accepted, pressing [ENTER] once again will
continue to the next option.
Next, you can enter and modify the pre- and post-weld parameters for
each weld procedure. These features include Max Scale allowed, Pre-
Purge gas time, Strike Current value, number of tacks and Post-Purge
gas time.
2.9.1.1 Maximum Scale Change
This value limits the amount, by percentage, by which both the Current
and Motor Speed may be scaled, either up or down. This value should
be large to allow for compensations of expected variations in material and
welding conditions, but not so large that control of the welding process is
lost.
This value has no effect unless the ACL system is in Production Mode
(see WELDING OPERATIONS in this section).
2.9.1.2 Pre-Purge Time
This is the amount of time that the purge gas will flow prior to starting the
welding arc. Valid values are from 0.02 to 300.00 seconds.
2.9.1.3 Strike Current
This is the current value at which the arc will strike and initiate an arc.
Valid values are from 5.0 to 25.0 amps.
2.9.1.4 Tacks Number
This value determines how many tacks are required around the
circumference of the item to be welded. Multiple tacks will occur at
opposing points with the last tack opposite Home or the programmed Start
Position. Valid values are from 0 to 8 tacks. The tack parameters are
specified in the Advanced Tab.
2.9.1.5 Post-Purge Time
This is the amount of time that the purge gas will flow once the welding
arc has extinguished, regardless if the procedure has fully completed or
whether the operator has prematurely halted the procedure by pressing
[STOP]. Valid values are from 0.02 to 300.00 seconds.
2.9.1.6 Procedure Levels Information Table
Level 1 of each procedure is considered the Up Slope Level; in this Level
current and rotor speed will initiate and start the welding arc, commence
rotation of the rotor and take the procedure to its programmed welding
parameters.
Level 2 and subsequent Levels’ hereafter, are considered Weld Levels.
The previous Up-Slope Level simply initiated and started welding; these
next Levels will be programmed to perform the actual welding of the tubes,
fittings, and parts. Up to 90 levels are available (excluding the Final Slope
Level) for entering and modifying welding parameters.
The welding parameter values have the same function as in Level 1.
Once the Weld Level data has been entered and/or modified, the ACL
program will automatically move to the next subsequent Level.
The Final Slope Level (marked as **) is considered part of the weld
procedure, but it does not perform any welding. The function of the Final
Slope Level is to slope the welding current and travel speed in order to
eliminate detrimental effects produced by the heat of the welding arc, and