Skutt KilnMaster Kilns Manufactured between 2000 and 2006 User Manual
Page 35
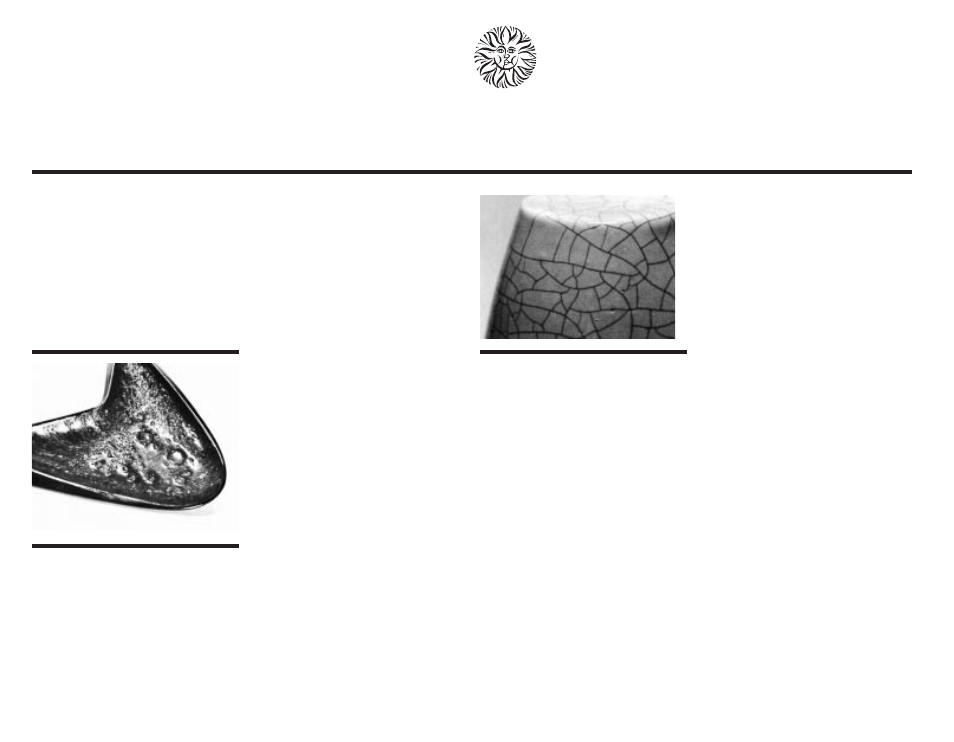
33
Excessive application of glaze.
The exam-
ple shown demonstrates the type of sur-
face which can result from too heavy an
application of glaze. This error is difficult
to salvage, so remember to apply less
glaze in the future. In general glaze should
be the thickness of a postcard when
applied. Allowing the glaze to dry thor-
oughly between coats will assist in identi-
fying the amount of glaze that has been
applied.
Discolored overglazes.
Underfiring occa-
sionally leaves small pin holes or pores in
the glaze that can’t be seen without a mag-
nifying glass. If there is poor ventilation in
the kiln, china paint oils may seep into
these pores and burn to charcoal, seriously
affecting the color of the finished piece.
You can sometimes repair the damage by
soaking the piece for several hours at a
low red heat about 1200˚F/650˚C, cooling
and inspecting to be certain that all the
carbon has been oxidized, and then giving
the piece a true glaze firing.
Cracks in the body.
When a crack occurs
in the body, examine the glaze at the edge
of the crack. If the glaze is inside the crack
or rounded over the corners, the break
occurred early in the glaze firing, and was
probably present in the clay body before
the piece was glaze fired. In some
instances a sound appearing piece of ware
will crack during a glaze or overglaze fir-
ing. This can be caused by an excess of
water used in the original clean-up of the
greenware. Too much moisture applied to
an area of greenware causes that area to
expand while the dry or slightly damp
areas have already gone through normal
shrinkage. Even if a piece of dry, cleaned
greenware shows no visible cracks, it is
possible an internal stress is there. This
crack can open up during later firings. If
the glaze at the edge of the crack is sharp,
the break developed after the glaze was
fired. This type of crack is usually due to
opening the kiln door or peepholes while
the ware is still hot.
Crazing.
Crazing is characterized by a net-
work of fine cracks in the glaze surface. It
may be caused by underfiring bisque, clay
or glaze, incompatible clay and glaze, or
by opening the kiln door before the ware
is completely cooled. Crazing might be
eliminated by refiring the piece to a tem-
perature one cone higher than the original
firing.
Delayed or aftercrazing.
Crazing may
also occur days or months after the piece
has been fired. Although the finish may
look perfect when it is first removed from
the kiln, crazing may occur. While under-
firing may not be the direct cause of
immediate crazing, it is the major cause of
delayed crazing. To correct it, refire the
piece to the cone recommended by the
manufacturer of the glaze. Allow the kiln
to cool naturally.
Shiny matte surface.
A matte glaze which
becomes glossy in the glaze firing is gener-
ally caused by overfiring. It is extremely
difficult to correct. Remember to fire to a
lower temperature in the future.
Textured glazes, smoothed.
A textured
glaze is formulated to develop an irregu-
lar surface when fired. If it fails to do so, it
is generally due to too light an application
of glaze. It is extremely difficult to correct
this condition. Reglazing and refiring
rarely will help.
Cloudy or discolored glazes
. This condi-
tion is characterized by a muddy or dis-
colored appearance in the fired glaze. It
may be caused by using dirty or contami-
nated brushes, by not leaving enough
space between the glazed pieces during
firing so chemical fumes jump from one
glaze to another, or by placing the piece
too close to the kiln elements. It is
extremely difficult to correct.
Grainy glaze.
Uneven or irregular color in
the glaze surface is generally caused by
too thin an application of glaze. To correct,
apply a coat of glaze, then refire.
Gray or discolored red glazes.
Gray wash
out, or black areas in the red glaze may be
caused by too thin an application of glaze,
the red glaze being fired with colors
which it is incompatible, (generally yel-
lows and greens) or firing too hot. This
may also be the result of too little oxygen
present during the firing. Cone 07 to 06 is
usually the best range for red glazes. To
salvage, apply a heavy coat of glaze and
refire. Use of the Skutt EnviroVent is
another way to eliminate these problems.
Underglaze peeling.
Underglaze may
pull away from the clay body. This may
be caused by too heavy an application, or
not firing the underglaze before applying
glaze. It is extremely difficult to correct
this error.
This section on glaze faults prepared in collabo-
ration with Martin L. LaVor who assisted with
information and illustrations.
Pinholes, crazing.
Excess glaze.