Appendix e pid tuning – TE Technology TC-24-25 User Manual
Page 20
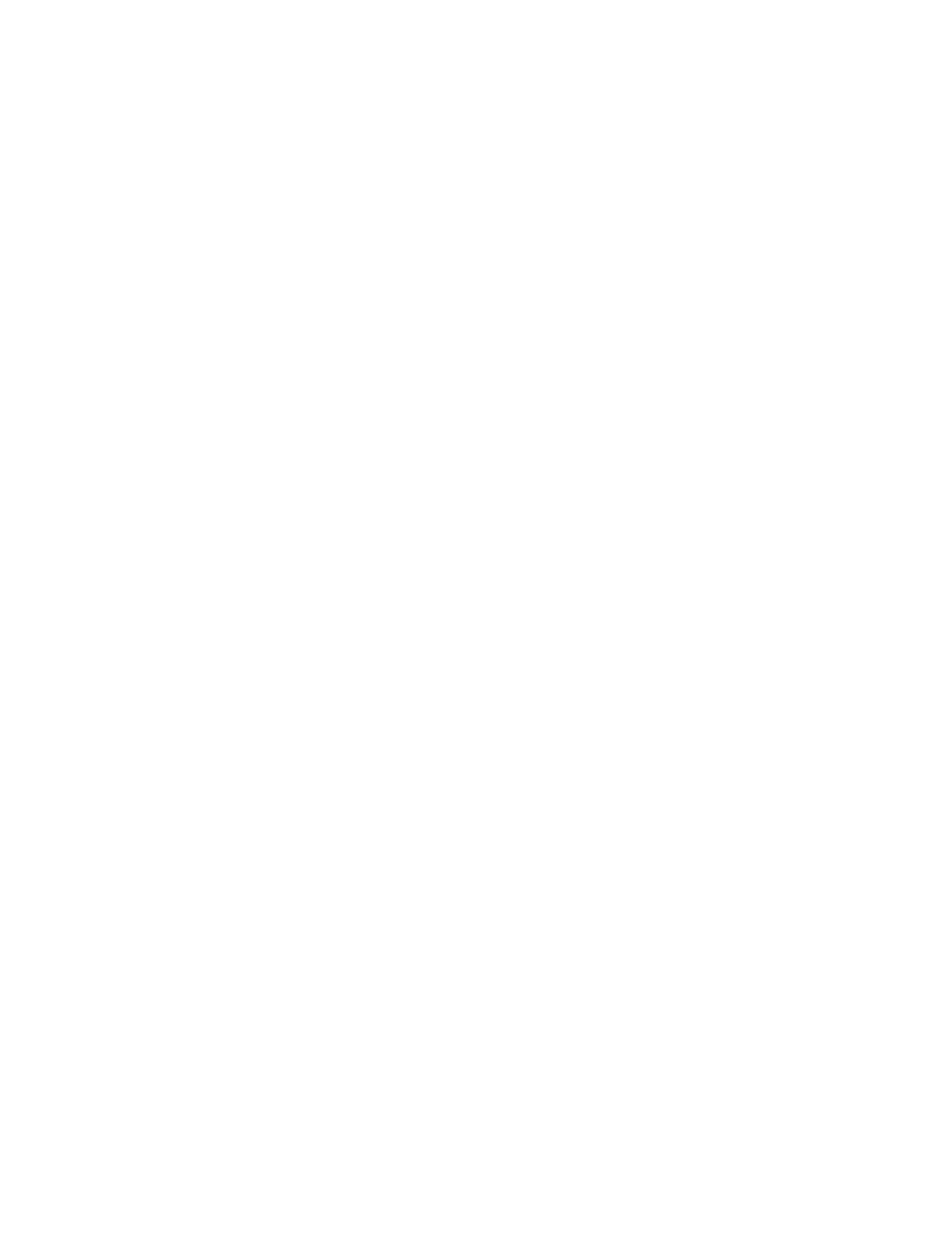
20
APPENDIX E PID Tuning
Tuning the TC-24-25 temperature controller involves three variables: (P)ROPORTIONAL
BANDWITH, (I)NTEGRAL GAIN, and (D)ERIVATE GAIN.
The control algorithm sums the three values of these terms to determine the output power.
P + I + D = > Power Applied
Most applications work satisfactorily with only the “P” and “I” values used.
Start the tuning process by setting the Integral and Derivative functions to zero. Then turn on the
controller.
PROPORTIONAL BANDWITH is defined as the temperature range around the set point where the
controller modulates (proportions) the output power. When the actual temperature deviates from the set
temperature, the “P” term of the control equation is increased until the power output reaches 100%.
Stated another way, the amount of temperature deviation required to increase the output to 100% is, by
definition, the proportional bandwidth. The programmable bandwidth range of the TC-24-25 is from 1°
to 100°. The units are shipped with a default setting of 20°.
Each thermal system has its own time constants determined by the thermal mass of the components and
the placement of the sensor relative to the load. When the “I” and “D” terms are set to zero, and the
bandwidth is too large, the temperature will never reach the set point. In this case the controller’s output
will approach zero as the temperature difference approaches zero, so the system will never get the
required power to actually reach the set point. On the other hand, if the bandwidth is too small and there
is any time lag between the cooling/heating element and the temperature sensor, the temperature will
initially overshoot the set point and then settle into a pattern of oscillation above and below the set point.
Assuming the controller is configured for your requirements, start the tuning process by applying power
with the default settings and observing the system’s response. If the system comes into the proportional
band and maintains a steady temperature near set point, without over shoot, the bandwidth setting is either
satisfactory or too large. Reduce the bandwidth setting until the system just begins to oscillate. At this
point, the bandwidth is too small. Note the bandwidth setting that just caused the system to oscillate, and
record the period of oscillation for use in determining the Integral Gain setting. To set the proportional
bandwidth, multiply the current bandwidth setting by 1.5 and use it as your new bandwidth setting. The
system should come into control and maintain a steady temperature near the set point.
INTEGRAL GAIN monitors the difference between the set point and the actual temperature. Its
function is to slowly change the output power until the difference between actual temperature and set
temperature is zero.
The function works by integrating the error signal at fixed intervals. The intervals are expressed in
repeats per minute. The acceptable range for the TC-24-25 is 0.01 to 10 repeats per minute. Start with a
setting determined by the following formula:
Integral Gain = 1/(2 x T) where “T” is the period of oscillation measured above. The period is expressed
in minutes.