Seat removal, Diaphragm replacement, Start-up – Jordan Valve Mark 60 Series - Sliding Gate Pressure Regulator User Manual
Page 2: Trouble shooting, Maintenance
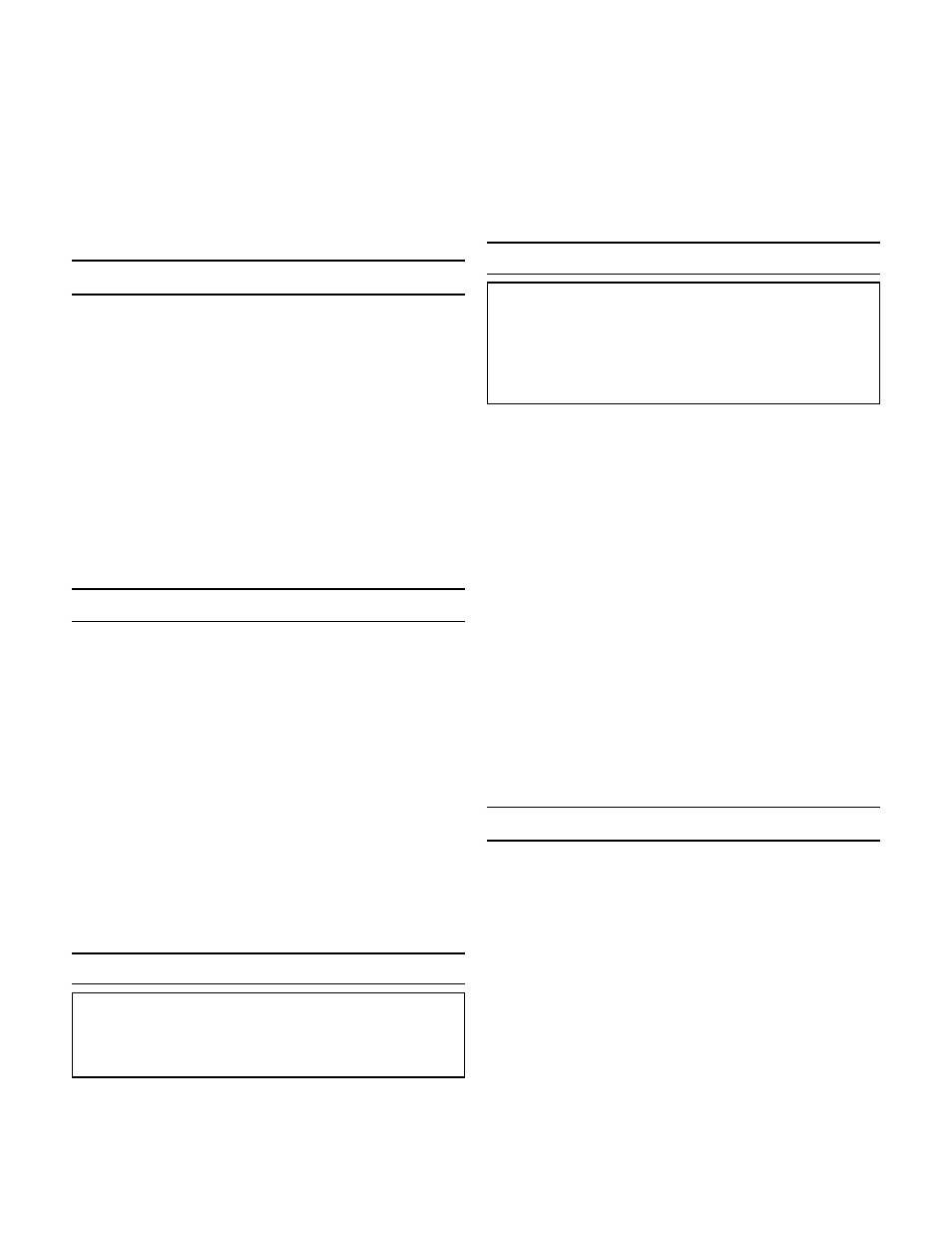
the valve by bleeding pressure from the upstream
side of the valve.
4.
When the pressure gauges indicate that all pres-
sure has been removed from the system, close the
outlet shutoff valve. The valve may be removed
from the line and serviced.
Note: Refer to the drawings at the end of the docu-
ment for description and proper orientation of parts.
Seat Removal
Jordan Valve Sliding Gate Seats are lapped to
light band flatness. Maintaining such tolerances
is of paramount importance of your assurance
of excellent operation and tight shutoff. DO NOT
use metallic objects in removing the seats. Care
in handling is imperative.
1.
With the valve out of the line, remove the cap bolts
(29), and lift the cap (28) straight up off of the body
(19). Notice that the cap has an internal vertical
web on which the disc spring is located. Check the
connection of the disc spring (26).
2.
Lift the disc (25) off of the plate (23) and place on a
clean surface with the lapped sides up.
3.
Place the valve body on its side. Place a hand over
the plate (23) to receive it and tap lightly on the
back of the plate with a soft, blunt object; push the
plate (23) out evenly. Place the plate on a clean
surface, lapped side up.
4.
Clean all parts and the body and cap with a good
quality solvent. The disc (25) and the plate (23)
may then be cleaned. Place a 4/0 polishing cloth
or jeweler’s cloth on a smooth, flat surface and in
a figure “8” motion. If the parts are scarred, do not
attempt to re-lap them, but return them to the fac-
tory for repair or replacement.
5.
Continue on to the procedures outlined under
STROKE ADJUSTMENT.
Diaphragm Replacement
1.
In removing the diaphragm (9), you must first re-
move the disc and the plate. This is outlined under
SEAT REMOVAL previously.
2.
Remove all of the compression from the spring (6)
by rotating the adjusting screw (1) counterclock-
wise until it moves freely. (Failure to remove the
pressure from the spring could result in personal
injury or damage to the valve.)
3.
Remove the spring housing bolts (8) and spring
housing (7). Remove the spring (6), and the spring
seat (5).
4.
Hold the disc pin (17) with an open-end wrench
and remove the diaphragm assembly by rotating
counterclockwise. The diaphragm assembly con-
sists of the upper diaphragm plate (11), diaphragm
(9), and lower diaphragm plate (12).
5.
If the diaphragm must be replaced, secure the low-
ing to the vessel.
5.
The control line should be sloped away from the
valve.
6.
Install a shut-off valve (not a needle valve) in the
control line.
7.
Install a pressure gauge in the control line or near
the inlet of the valve to aid in setting the valve and
checking for inlet pressure during maintenance
procedures. (There is a ¼” NPT tapped opening in
the lower bonnet.)
Start-Up
1.
Fully open the control line shut-off valve.
2.
Fully open the outlet shut-off valve.
3.
Slowly open the inlet shut-off valve.
4.
Slowly open and close outlet shut-off valve several
times. This fully strokes the valve to insure satisfac-
tory operation.
5.
With the outlet shut-off valve open, slowly screw
down the adjusting screw until the desired pres-
sure is shown on the outlet pressure gauge.
6.
To change the controlled pressure, turn the adjust-
ing screw clockwise to increase the pressure, and
counterclockwise to decrease the pressure.
7.
Body and cap bolts should be retightened to 90-ft./
lbs. torque after valve reaches operating tempera-
ture.
Trouble Shooting
If You Experience Erratic Control:
Oversizing causes cycling and hunting and reduces
the rangeability of the valve. Make certain that your
sizing is correct.
Steam Traps downstream may need attention.
Safety Valve may be jammed open.
Excessive foreign matter on seats.
Valve Stroke out of adjustment. Check and readjust
if necessary.
Valve disc may not be moving freely. Check disc
guide clearance and clearance of the stem to the
bushings.
If the Valve Will not Operate:
Diaphragm ruptured.
Adjusting spring broken. Replace.
Improper spring setting. Reset.
Maintenance
Caution: Ensure that the valve is de-pressurized
before loosening any fittings and joints. The fol-
lowing steps are recommended before perform-
ing any maintenance on the valve.
1.
Close the control line shut-off valve.
2.
Close the inlet shut-off valve.
3.
Allow pressure to bleed off through downstream
piping. Do not attempt to reverse the flow through
-2-