4 guarding, 5 priming and auxiliary supplies, 6 starting the pump – Flowserve MP1 Sier-Bath User Manual
Page 23: High temperature start up, Post start-up
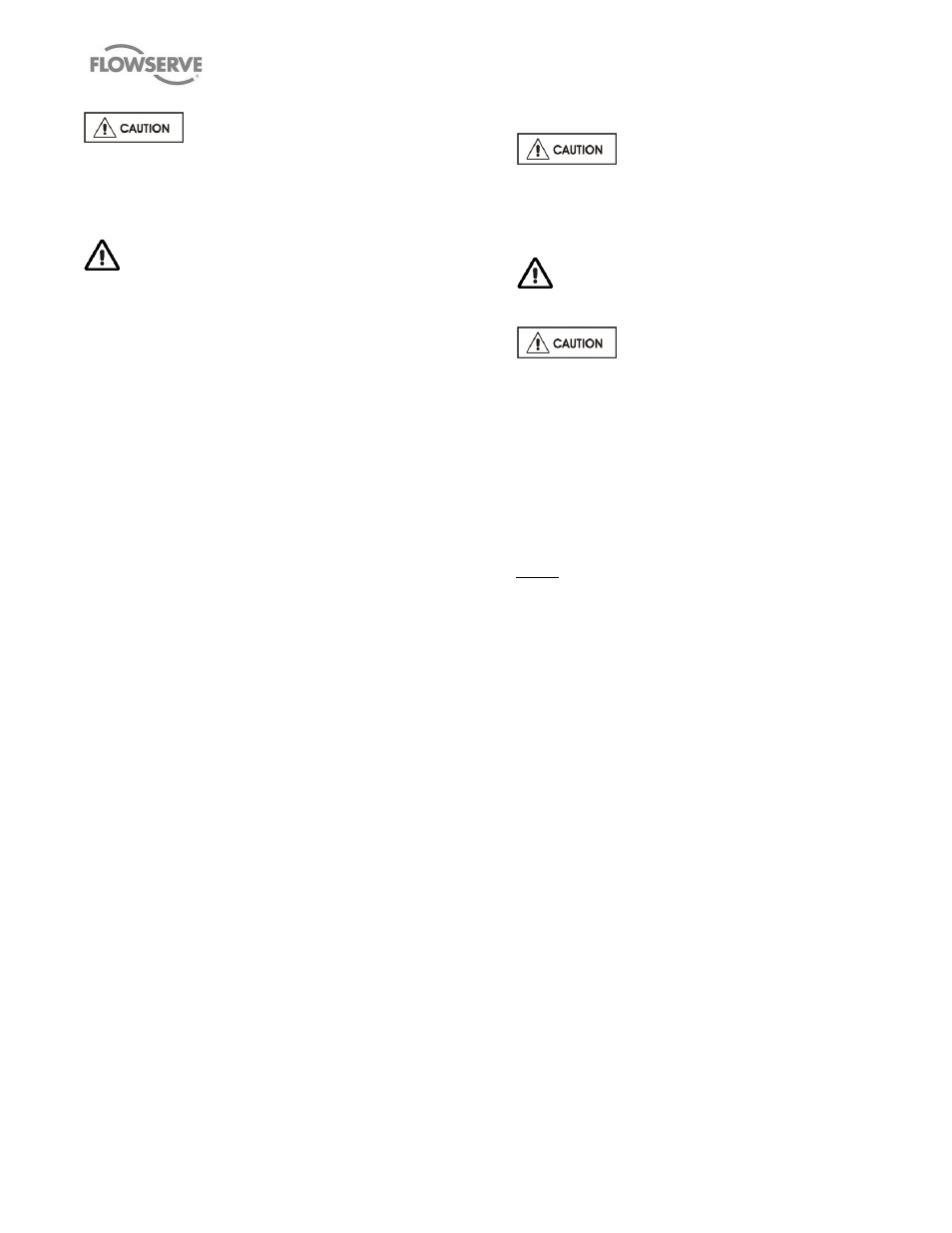
MP1 USER INSTRUCTIONS ENGLISH 26999958
– 10-12
Page 23 of 48
flowserve.com
If maintenance work has been carried
out to the site's electricity supply, the direction of
rotation should be re-checked as above in case the
supply phasing has been altered.
5.4 Guarding
Guarding is supplied fitted to the pump set. If this
has been removed or disturbed ensure that all the
protective guards around the pump coupling and
exposed parts of the shaft are securely fixed.
5.5 Priming and auxiliary supplies
Before starting any rotary pump it is absolutely
necessary that both the pump and suction line be
primed with liquid. This can be accomplished by one
of the following methods:
1. Remove pipe plug from discharge side of body
and install a temporary filling line. Pour
appropriate amount of the liquid being pumped
into the pump through
this line while rotating the
pump by hand in the opposite direction from that
shown on the rotation arrow. This will cause the oil
to work into the pumping rotors to help seal while
priming. Turn temporary filling line down and direct
into the baseplate drip pan or some other suitable
container. Start the pump, running it in the rotation
shown on the rotation arrow. When a solid stream
of oil is achieved from the filling line, stop the
pump, remove the piping and replace the pipe
plug.
2. When the liquid supply level is above the pump
discharge valve, it is primed by opening the
suction and discharge valves. The in-flowing liquid
will displace the air and fill the suction line, pump
casing and discharge line up to the level of supply.
3. When the above two methods are unsuitable, it is
necessary to vacuum prime the pump. This can be
accomplished with a vacuum pump or air ejector.
The priming line is attached to the upper most
portions of the discharge / suction piping. To
prime, close the discharge valve and do not start
the driver until the pump and piping are full of
liquid. Provision must be made to seal the stuffing
box with sealing fluid to prevent in leakage of air.
It should be noted that if a valve is not provided on the
discharge side of the pump it may be necessary to
prime the entire system to avoid excessive power
consumption on initial start-up.
5.6 Starting the pump
a)
Ensure flushing and/or cooling/
heating liquid supplies are turned ON before
starting the pump.
b)
OPEN the outlet valve.
c)
OPEN all inlet valves.
d)
Prime the pump.
e)
Ensure all vent connections are closed
before starting.
f)
Start motor and check outlet pressure.
g)
Do not run the pump with the outlet
valve closed.
h)
If NO pressure, or LOW pressure, STOP the
pump. Refer to section 7 FAULTS; CAUSES AND
REMEDIES, for fault diagnosis.
5.7
High temperature start up
In case of a high temperature start up, it is essential
that the entire pump, including any product
recirculation piping, has had time to achieve stability at
the required operating temperature prior to start up. If
the entire pump is not stable at the required operating
temperature, it could cause distortions in the housings
or body and may cause mechanical problems during
start up or operation. The same precaution is also true
of the recirculation piping. It is also imperative that the
pump and recirculation piping be completely covered
with securely fastened insulation.
In addition to the standard start up procedures outlined
the following steps should be followed in high
temperature applications.
1) An empty pump should first be filled with product
at ambient temperature to avoid thermal shock.
The pump should never be started empty or cold.
2) Steam or a heat transfer liquid should be
circulated through the housing and body jackets as
well as the recirculation piping jackets. The
heating medium should be at the operating
temperature and circulated at a rate which will
produce
a
maximum
temperature
rise
of
approximately 65 °C per hour (117 °F per hour). A
four hour heat soak period prior to start up is
recommended.
3) An appropriate flow of the heat transfer medium is
required during operation to ensure the pump is
maintained at the operating temperature.
5.8
Post start-up
Once the unit has operated satisfactorily for several
days, record as much information about these normal