9 running the pump – Flowserve MP1 Sier-Bath User Manual
Page 24
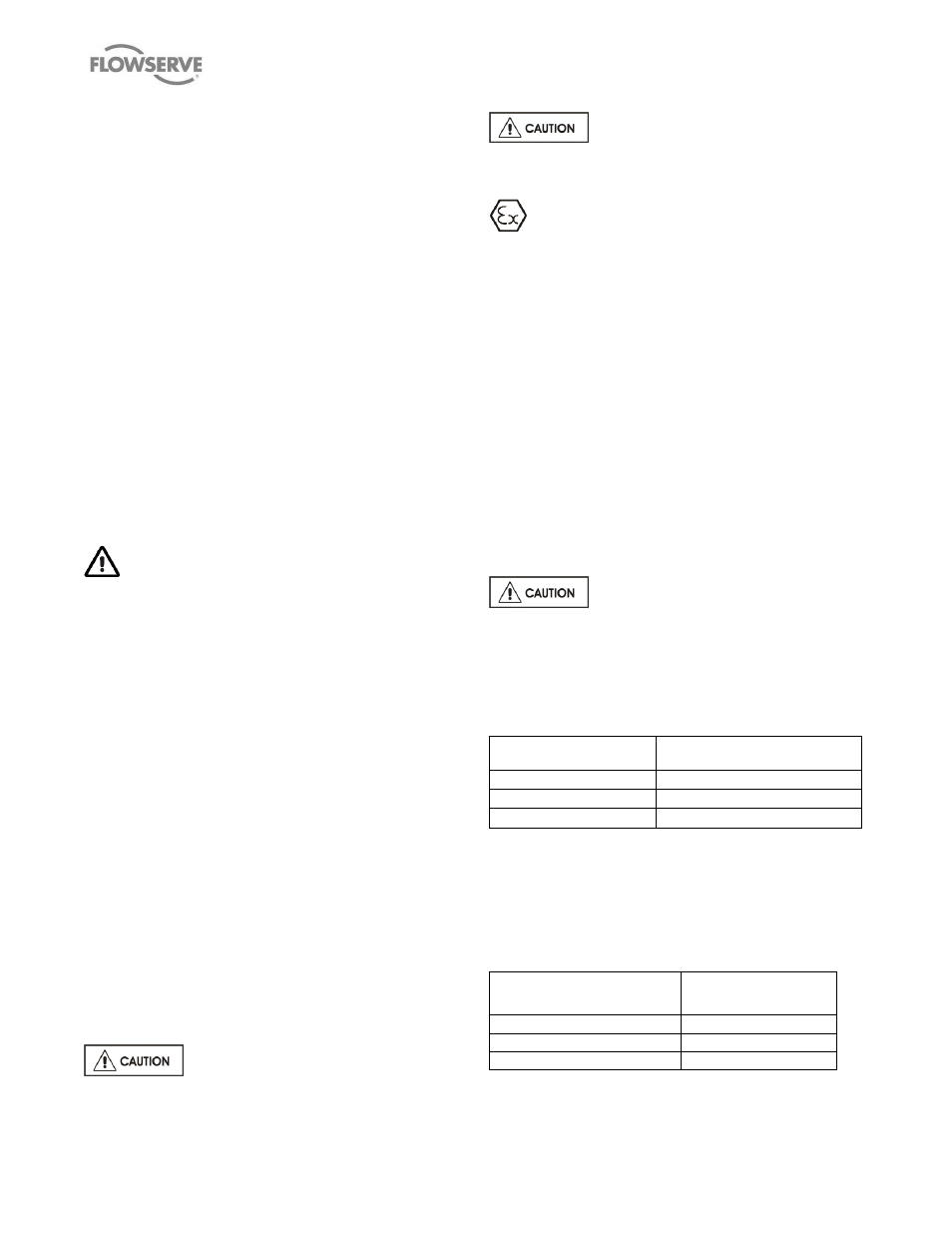
MP1 USER INSTRUCTIONS ENGLISH 26999958
– 10-12
Page 24 of 48
flowserve.com
operating conditions as possible. This data may be
helpful in identifying and correcting changes in future
performance before serious problems occur.
Typical data to be recorded is: serial number of pump
and driver, suction pressure, discharge pressure,
specific gravity, capacity, pump speed, amperage and
voltage (each phase), seal liquid pressure, ambient
temperature,
pumping
temperature,
bearing
temperatures, vibration etc.
After the unit has been running continuously about one
week, the coupling halves of direct driven units should
be given a final check for misalignment caused by pipe
strains or temperature strains. If the alignment is
correct, both the pump and driver should be dowelled
to the baseplate. The pump should be dowelled with
one dowel in each support foot. Refer to the
manufacturer’s
manual
for
driver
dowelling
instructions.
5.9 Running the pump
5.9.1 Venting the pump
Vent the pump to enable all trapped air to escape
taking due care with hot or hazardous liquids.
The pump can be vented by opening the plugs in the
suction chamber.
There is a spot between the Suction Spool and the
Outer Casing that cannot be vented before start-up.
Being a Multi-Phase Pump, there is no need to fully
vent the air from this location. There is no need to
have a bleed point on the Outer Casing just to vent this
pocket. The air or gas from this pocket might or might
not disappear during operation; but this little air or gas
trapped in this pocket should not pose a risk for the
operation of the pump.
Under normal operating conditions, after the pump has
been fully primed and vented, it should be unnecessary
to re-vent the pump.
5.9.2 Pumps fitted with mechanical seal
Mechanical seals require no adjustment. Any slight
initial leakage will stop when the seal is run in.
Before pumping dirty liquids it is advisable, if possible,
to run in the pump mechanical seal using clean liquid
to safeguard the seal face.
External flush or quench should be
started before the pump is run and allowed to flow for
a period after the pump has stopped.
Never run a mechanical seal dry, even
for a short time.
5.9.3 Bearings
It is recommended that temperature and/or
vibration monitoring at the bearings is done if the
pumps are working in a potentially explosive
atmosphere
If bearing temperatures are to be monitored it is
essential that a benchmark temperature is recorded at
the commissioning stage and after the bearing
temperature has stabilized. Record the bearing
temperature (t) and the ambient temperature (ta).
Estimate the likely maximum ambient temperature (tb).
Set the alarm at (t+tb-ta+5)
C [(t+tb-ta+10)
F] and
the trip at 100
C (212
F) for oil lubrication.
5.9.4 Normal vibration levels, alarm and trip
For guidance, pumps generally fall under a
classification for rigid support machines within the
International rotating machinery standards and the
recommended maximum levels in Table 5 are based
on the API-676 standard, 3
rd
Edition.
Alarm and trip values for installed
pumps should be based on the actual measurements
(N) taken on the pump in the fully commissioned as
new condition. Measuring vibration at regular intervals
will then show any deterioration in pump or system
operating conditions.
Table 5
– Max. vibration limits
Condition
Vibration velocity
– unfiltered
mm/s (in./s) r.m.s.
Normal
N
5.5 (0.22)
Alarm
N x 1.25
6.9 (0.27)
Shutdown trip
N x 1.5
8.2 (0.32)
5.9.5 Stop/start frequency
Pump sets are normally suitable for the number of
equally spaced stop/starts per hour shown in the Table
6. Check actual capability of the driver and
control/starting system before commissioning.
Table 6
– Motor stop/starts per hour
Motor rating
kW (hp)
Maximum stop/starts
per hour
Up to 15 (20)
15
Between 15 (20) and 90 (120)
10
Above 90 (120)
6