Final shaft alignment check – Flowserve TB-MAG INNOMAG User Manual
Page 21
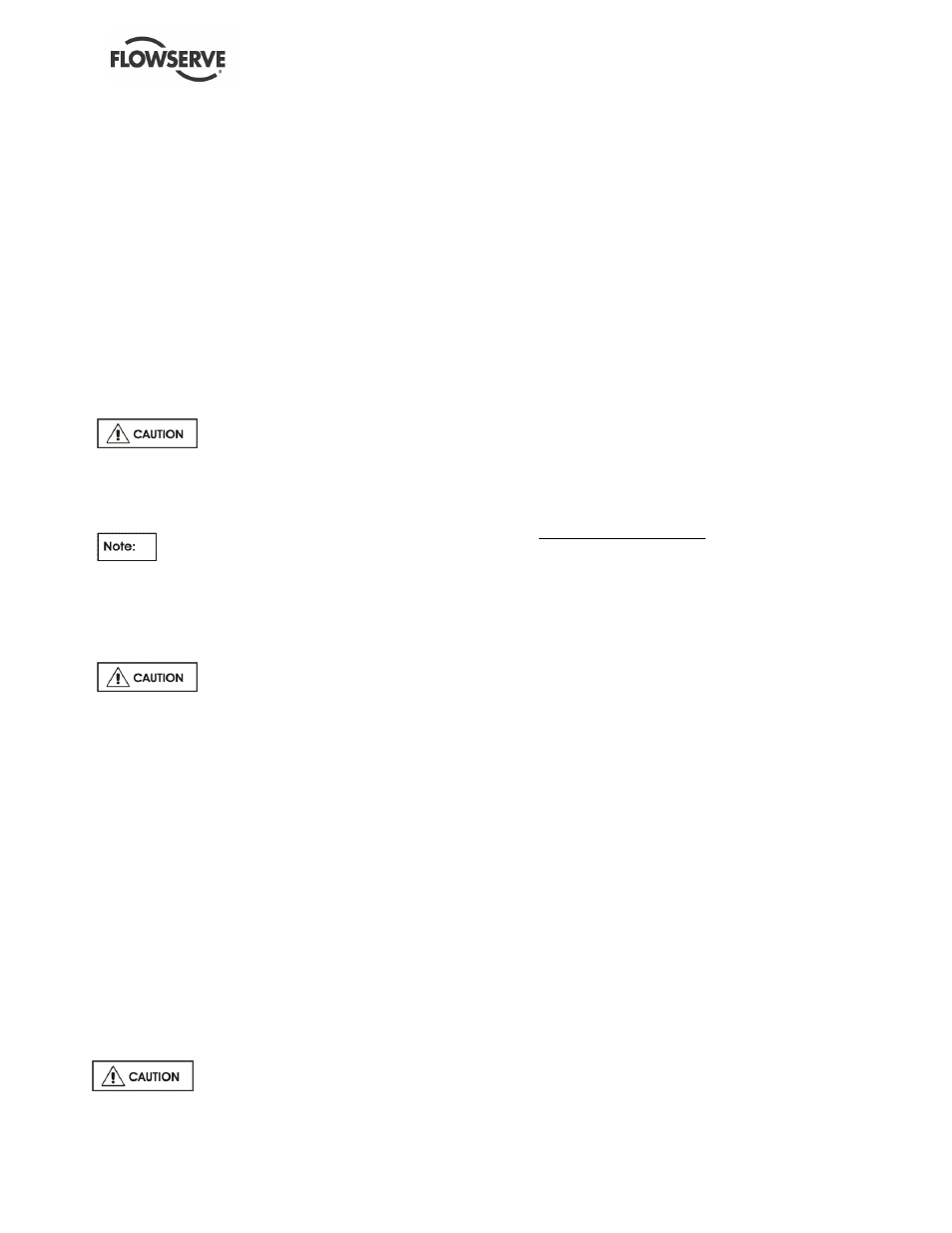
INNOMAG® TB-
MAG™ ASME and ISO SEALLESS ENGLISH 26999988 06-14
Page 21 of 44
4.7.1.2 Temperature probe
An optional ThermicSense temperature probe can
be installed on the casing drain to monitor the
internal fluid in the casing [1100].
4.7.1.3 ThermicSense Installation
The ThermicSense thermowell will be packaged
separately for protection during shipping and must
be assembled before use. For wiring refer to the
thermocouple sensor manufacturer’s instructions
a)
Verify that rubber gasket / o-ring is secured to
temperature sensor tip.
b)
Insert temperature sensor tip into the
thermowell and hand tighten.
c)
Use a 1/2 in. wrench to fully secure the sensor to
the thermowell.
Do not over-tighten.
d)
Adjust direction of sensor sheathing before
tightening compression fitting.
e)
Ensure sensor tip is fully pressed into
thermowell.
The sensor must be fully inserted to get an
accurate reading.
f)
Hand-tighten the compression fitting.
g)
Use a 1/2” wrench to fully tighten the
compression fitting and secure sensor
sheathing.
Do not over tighten the fitting.
h)
Affix the PTFE drain gasket to thermal well.
i)
Insert the completed ThermicSense assembly
into the casing drain and insert bolts (1/2 in.-13
ASME, M12x1.75 ISO) with lock washers.
j)
Tighten bolts evenly to maintain alignment and
torque to 13.5 Nm (10 lbf
•ft)
k)
Install wire leads to appropriate temperature
monitor per manufacturer instructions and
guidelines.
4.8 Final Shaft alignment check
4.8.1 Close-coupled pumps
Alignment between the pump shaft and motor shaft
is built in by precise machining of the parts that
position these shafts. Parallel alignment of 0.18
mm (0.007 in.) and angular alignment of 0.002
mm/mm (0.002 in./in.) can be expected.
4.8.2 Long-coupled pumps
The pump and motor will normally
have to be aligned at ambient temperature with an
allowance for thermal expansion at operating
temperature. In pump installations involving high
liquid temperatures, typically above 100 ºC (212
ºF), the unit should be run at the actual operating
temperature, shut down and the alignment checked
immediately.
a)
Level baseplate if appropriate.
b)
Mount and level pump if appropriate. Level
the pump by putting a level on the discharge
flange. If not level, adjust the foot piece by
adding or removing shims [3126.1] between
the foot piece and the bearing housing.
c)
Check initial alignment. If pump and driver
have been remounted or the specifications
given below are not met, perform an initial
alignment as described in section 4.5. This
ensures there will be sufficient clearance
between the motor hold down bolts and motor
foot holes to move the motor into final
alignment. The pump and driver should be
within 0.38 mm (0.015 in.) FIM (full indicator
movement) parallel, and 0.0025 mm/mm
(0.0025 in./in.) FIM angular.
Stilt mounted baseplates
If initial alignment cannot be achieved with the
motor fasteners centered, the baseplate may
be twisted. Slightly adjust (one turn of the
adjusting nut) the stilts at the driver end of the
baseplate and check for alignment to the above
tolerances. Repeat as necessary while
maintaining a level condition as measured from
the pump discharge flange.
d)
Run piping to the suction and discharge to the
pump. There should be no piping loads
transmitted to the pump after connection is
made. Recheck the alignment to verify that
there are no significant changes.
e)
Perform final alignment. Check for soft-foot
under the driver. An indicator placed on the
coupling, reading in the vertical direction,
should not indicate more than 0.05 mm (0.002
in.) movement when any driver fastener is
loosened. Align the driver first in the vertical
direction by shimming underneath its feet.
f)
When satisfactory alignment is obtained the
number of shims in the pack should be
minimized. It is recommended that no more
than five shims be used under any foot. Final
horizontal alignment is made by moving the
driver. Maximum pump reliability is obtained by
having near perfect alignment. Flowserve
recommends no more than 0.05 mm (0.002 in.)
parallel, and 0.0005 mm/mm (0.0005 in./in.)
angular misalignment.
g)
Operate the pump for at least an hour or until it
reaches final operating temperature. Shut the