Flowserve QLQ Vertical Worthington User Manual
Page 14
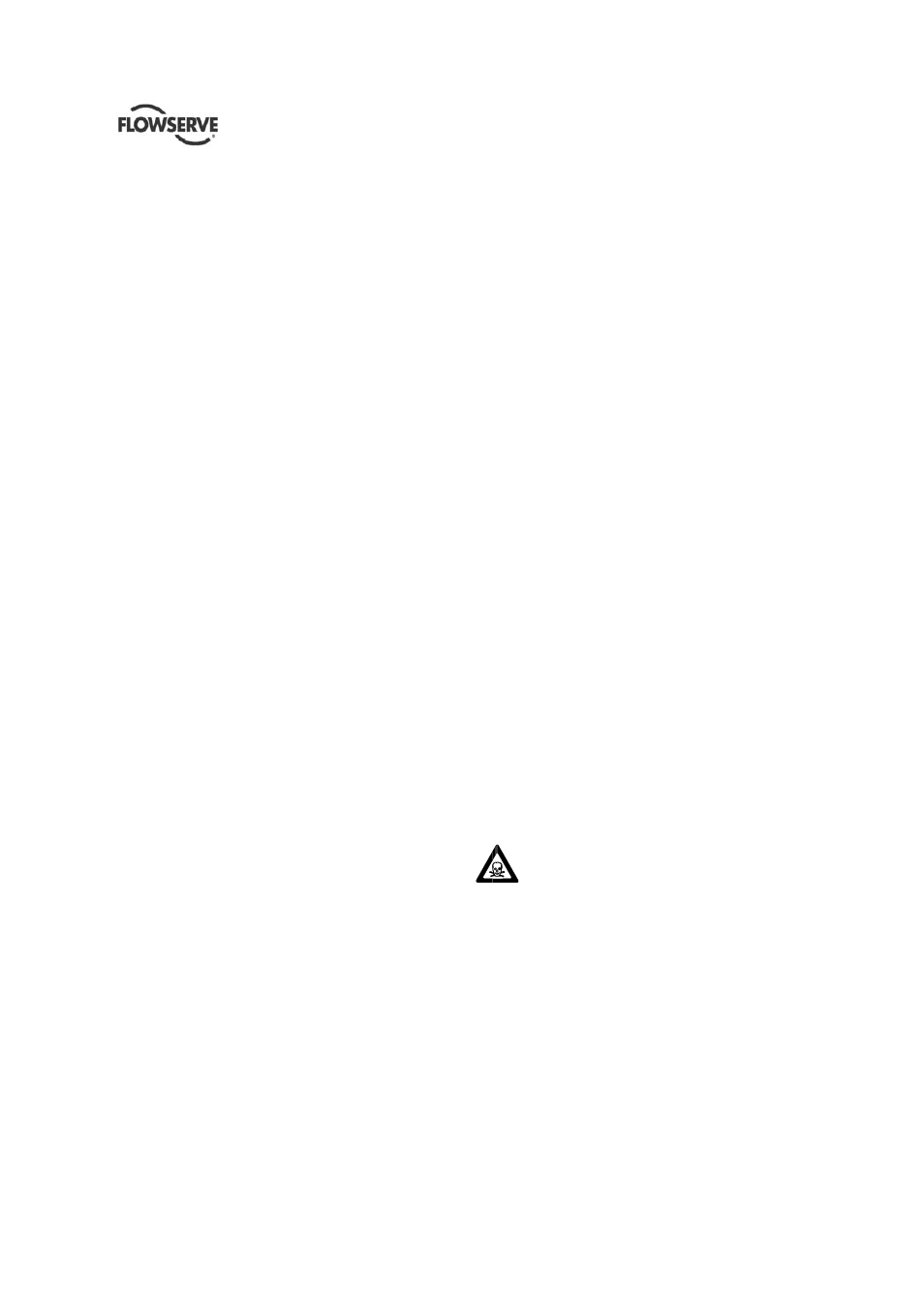
QLQ, QLQC USER INSTRUCTIONS ENGLISH 87900027 – 06/14
Page 14 of 61
d) Depending upon the length of time the equipment
was stored, the type of storage provided (i.e.
Indoor: heated, unheated, ground floor, concrete
floor. Outdoors: under roof, no roof, waterproof
coverings, on concrete, on ground) and as a
result of the inspection of (a),(b) & (c) above the
FLOWSERVE representative may require a
partial or complete dismantling of the equipment.
e) Dismantling may necessitate restoration of
painted or preserved surfaces, and, or
replacement of gaskets, "O" rings, packing and
bearings.
f) All costs involved during inspection, dismantling,
restoration, replacement of parts and reassembly
will have to the accounted to the purchaser. All
necessary labour, tools and cranes will be
supplied by the purchaser.
Upon completion of the inspection the FLOWSERVE
representative shall submit a report to the purchaser,
and to the Manager of Customer Service, stating in
detail the results of the inspection.
One month prior to installation of the equipment, a
FLOWSERVE representative is to be employed to
conduct a final inspection. This inspection will be
made to assure that the requirements of the six
months inspection report were satisfactorily
completed and that the equipment is ready for
installation.
Upon completion of this inspection the FLOWSERVE
representative shall submit a final report to the
purchaser, and to the Manager of Customer Service,
advising the results of the final inspection.
All costs involved in conducting the final inspection
will have to the accounted to the purchaser.
Prior to and during start up, any requirements for the
services of an FLOWSERVE representative will
revert back to the original contract agreement for
equipment purchased, with revised costing.
2.4.1.4 Delay in the startup
Startup of the pumps, after installation on the plant,
should be executed within two months as a
maximum.
In case, for any reason, the period between
installation and startup should exceed the two
months, the following precautions must be taken:
a) If acid descaling are foreseen on the plant, the
pump must be by-passed during these
operations, or, otherwise, shall be fully
disassembled, washed with basic solution, dried
and reassembled. All these operations shall be
executed by Flowserve personnel or under
Flowserve supervision.
b) It is advisable, for a long term permanence on the
plant before startup, that blind flanges are
interposed between the pump nozzles and the
relevant pipe, to avoid the possibility that foreign
material can be introduced into the pump. In case
such flange s not installed, it is advisable that the
inner parts of the pumps is carefully inspected
(by disassembling, if necessary) to verify the
absence of foreign material before the startup.
c) During the period between installation and
startup the same maintenance checks described
in point 2.4.1.3 shall be carried out.
2.4.1.5 Painting and preservation
Paints and preservatives used are either
FLOWSERVE standard or 'special' as required by the
contract specification. Refer to FLOWSERVE for the
description of paints and preservatives used on this
order if needed.
2.4.1.6 Associated equipment
Motors, Turbines, Gears, etc., being supplied by
FLOWSERVE.
Generally rotors of associated equipment should be
blocked to relieve bearing loads. Storage should be
indoors and dry. See the specific manufacturers
storage requirements.
2.5 Recycling and end of product life
At the end of the service life of the product or its
parts, the relevant materials and parts should be
recycled or disposed using an environmentally
acceptable method and in accordance with local
regulations. If the product contains substances which
are harmful to the environment, these should be
removed and disposed in accordance with current
local regulations. This also includes the liquids
and/or gases that may be used in the "seal system"
or other utilities.
Make sure that hazardous substances are
disposed of safely and that the correct personal
protective equipment is used. The safety
specifications must be in accordance with the
current local regulations at all times.