Flowserve QLQ Vertical Worthington User Manual
Page 19
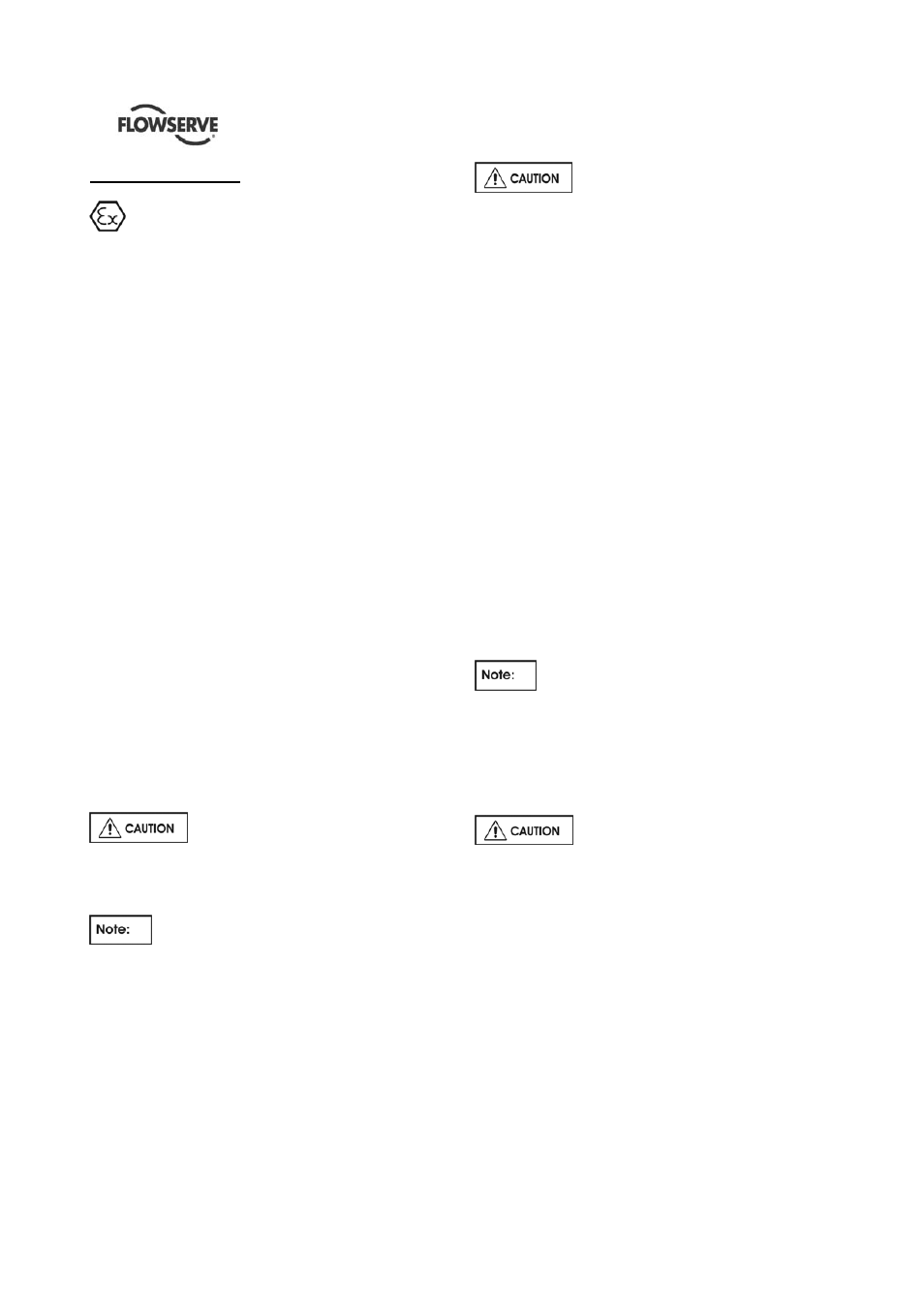
QLQ, QLQC USER INSTRUCTIONS ENGLISH 87900027 – 06/14
Page 19 of 61
4 INSTALLATION
Equipment operated in hazardous locations
must comply with the relevant explosion protection
regulations. See section 1.6.4, products used in
potentially explosive atmospheres.
Six months prior to the scheduled installation date, a
Flowserve Pump Division representative is to be
employed to conduct an inspection of the equipment
and the facility. If any deterioration of equipment is
noticed, the Flowserve Pump Division representative
may require a partial or complete dismantling of the
equipment including restoration and replacement of
some components.
4.1 Location
The pump should be located to allow room for
access, ventilation, maintenance and inspection with
ample headroom for lifting and should be as close as
practicable to the supply of liquid to be pumped.
4.1.1 General installation check-list
The following checks should be made before starting
actual installation.
a) Make sure that motor nameplate ratings and the
power supply system match correctly.
b) Check the sump depth and pump length match-
up.
c)
Check the liquid level in the sump.
d) Check the installation equipment to be sure that
it will safely handle the pump weight and size.
e) Check all pump connections (bolts, nuts etc.) for
any shipping and handling related problems.
Always support shafting in at least
three places when lifting or installing. No installation
should be attempted without adequate equipment
necessary for a successful installation.
On hollow shaft drivers, check the clutch size
against the shaft size, which must go through the
clutch
On solid shaft drivers, check the motor shaft size
against the coupling bore size
Apply thread lubricant sparingly to
male shaft threads only at the time of making up
shaft connection. Excess lubricant should be
avoided.
4.1.2 General installation instructions
As standard option the pumps are shipped with the
suction bowl, column and suction head fully
assembled and the suction barrel (if is supplied)
shipped separately.
4.1.2.1 Lifting
See lifting methods in section 2.3.
4.1.2.2 Equipment and tools required for
installation of a fully assembled pump
a) Mobile crane capable of hoisting and lowering the
entire weight of the pump and motor.
b) Cable sling for attaching to the pump and motor
lifting eyes.
c) Ordinary hand tools: Pipe wrenches, end
wrenches, socket set, screwdrivers, Allen
wrenches, wire brush, scraper and fine emery
cloth.
d) Thread sealing compound designed for type of
connection and light machinery oil.
The single most common cause of pump
vibration is from a bent shaft. Shafting is straightened
to stringent tolerances prior to shipping and great
care must be exercised in its handling.
Always support shafting in at least three places when
lifting or installing.
Parts and accessories may be placed
inside shipping containers, or attached to skids in
individual packages.
Inspect all containers, crates and skids for attached
parts before discarding.
Lifting heavy objects is dangerous. Use of
appropriate tools and procedures is must.
4.1.2.3 Uncrating and cleaning of a fully
assembled pump
a) Clean the parts of all dirt, packing material and
other foreign matter.
b) Clean all machined surfaces. Remove any rust
spots found on the machined surfaces with fine
emery cloth.