Flowserve WR User Manual
Page 10
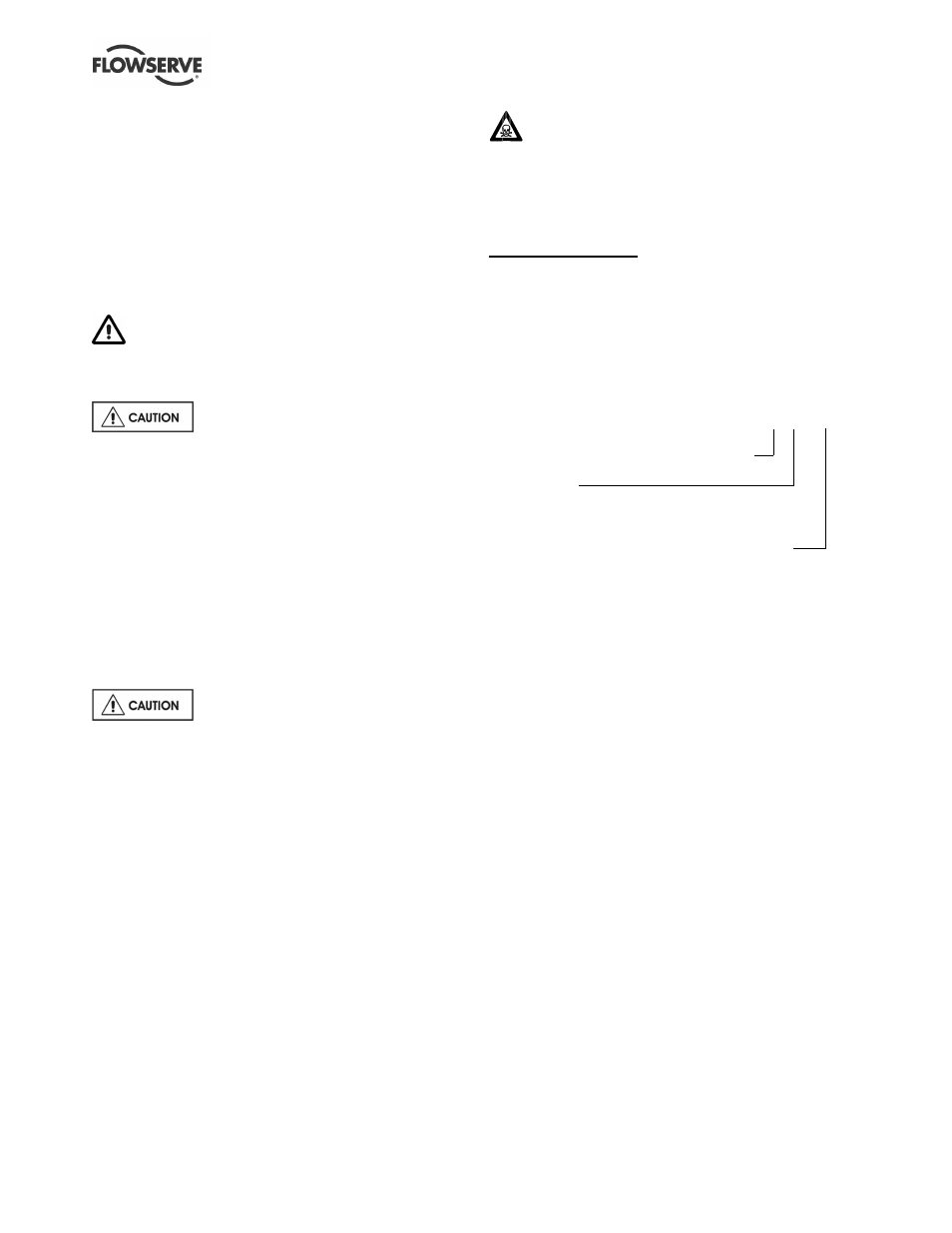
WR and CR USER INSTRUCTIONS ENGLISH 26999968 10-12
Page 10 of 28
flowserve.com
Each product has a unique serial number. Check
that this number corresponds with that advised and
always quote this number in correspondence as well
as when ordering spare parts or further accessories.
2.2 Handling
Boxes, crates, pallets or cartons may be unloaded
using fork lift vehicles or slings dependent on their
size and construction.
2.3 Lifting
A crane must be used for all pump sets or
components in excess of 25 kg (55 lb.). Fully trained
personnel must carry out lifting, in accordance with
local regulations.
No specific lifting points are provided
for this complete machine (unless so specified). Any
lifting points that can be seen are provided only for
dismantling parts for servicing. Slings, ropes and
other lifting gear should be positioned where they
cannot slip and where a balanced lift is obtained.
The angle between sling or ropes used for lifting must
not exceed 60°.
Before lifting the driver alone, refer to the
manufacturer’s instructions.
The driver weight is recorded on its nameplate.
2.4 Storage
Store the pump in a clean, dry location
away from vibration. Leave piping connection covers
in place to keep dirt and other foreign material out of
pump casing. Turn pump at intervals to prevent
brinelling of the bearings and the seal faces, if fitted,
from sticking.
The pump may be stored as above for up to 6
months. Consult Flowserve for preservative actions
when a longer storage period is needed.
2.5 Recycling and end of product life
At the end of the service life of the product or its
parts, the relevant materials and parts should be
recycled or disposed of using an environmentally
acceptable method and local requirements. If the
product contains substances that are harmful to the
environment, these should be removed and disposed
of in accordance with current regulations. This also
includes the liquids and or gases that may be used in
the "seal system" or other utilities.
Make sure that hazardous substances or toxic
fluids are disposed of safely and that the correct
personal protective equipment is used. The safety
specifications must be in accordance with the current
regulations at all times.
3 DESCRIPTION
3.1 Configurations
This is a robust centrifugal pump design for a wide
range of applications.
3.2 Name nomenclature
The pump size will be engraved on the nameplate
typically as below:
50WR160
Nominal discharge branch size in mm
Pump build:
WR - cast iron construction
CR - SS316 construction
Nominal maximum impeller diameter in mm
The typical nomenclature above is the general guide
to the D-line pump configuration description.
Identify the actual pump size and serial number from
the pump nameplate. Check that this agrees with the
applicable certification provided.
3.3 Design of major parts
3.3.1 Pump casing
The pump casing is designed with a horizontal
centreline end inlet and a vertical centreline top
outlet, which makes it self-venting. For ease of
maintenance, the pump is constructed so that pipe
connections do not have to be disturbed when
internal maintenance is required.
3.3.2 Impeller
A shrouded impeller with hub rings is fitted.
3.3.3 Shaft
The pump shaft is fitted directly on to the motor shaft
via a tolerance ring drive. The pump shaft or sleeve
can be removed from the motor for maintenance or
replacement.
3.3.4 Bearing housing and lubrication
The pump uses the driver's bearings to give primary
support and positioning to the input shaft. See the
driver's instruction book for lubrication details.