Flowserve WR User Manual
Page 17
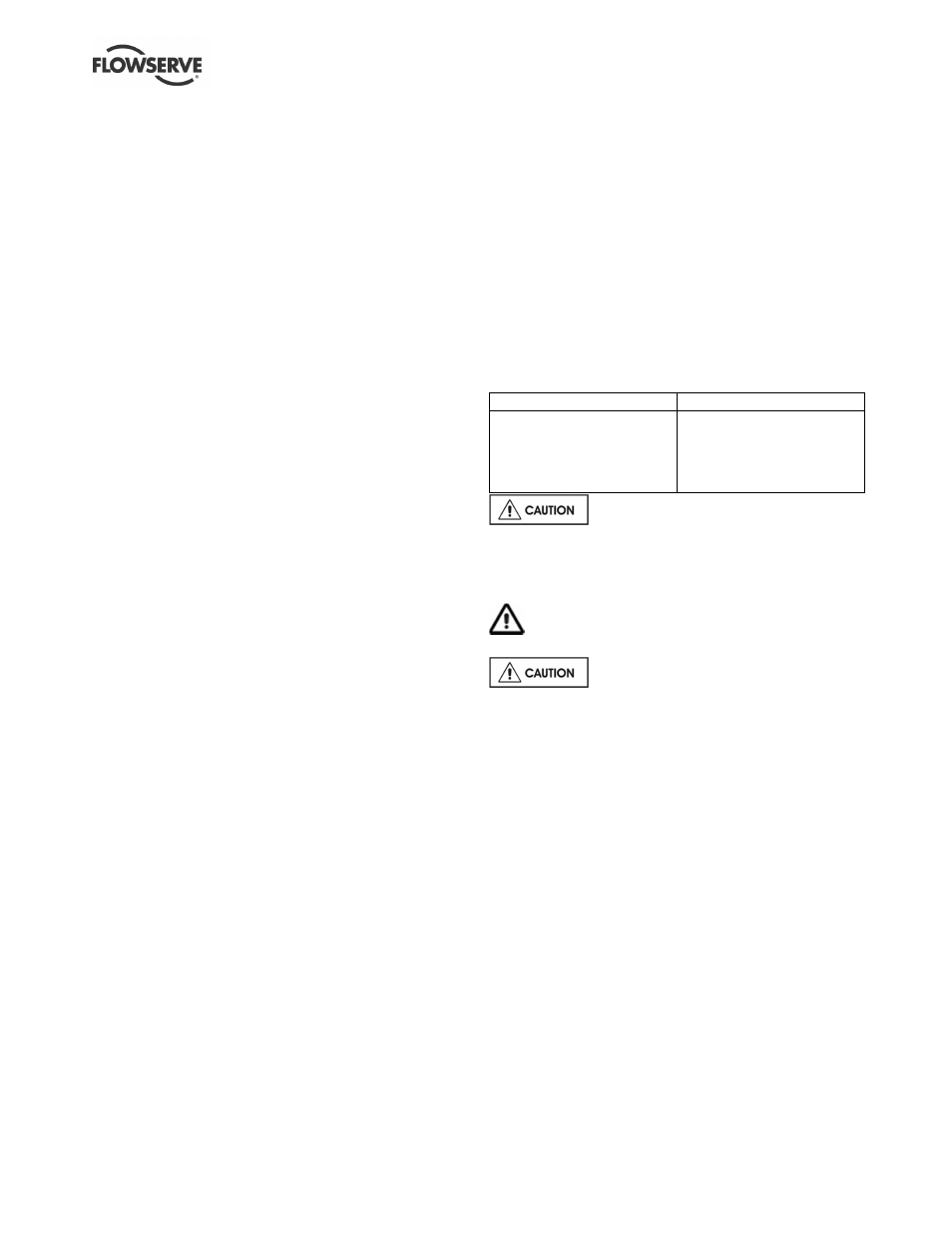
WR and CR USER INSTRUCTIONS ENGLISH 26999968 10-12
Page 17 of 28
flowserve.com
6.2.3 Re-lubrication
For general guidelines refer to section 5.1,
Lubrication.
Lubricant and bearing temperature analysis can be
useful in optimizing bearing change intervals.
6.2.4 Mechanical seals
When leakage becomes unacceptable the seal will
need replacement.
6.3 Spare parts
6.3.1 Ordering of spares
Flowserve keeps records of all pumps that have been
supplied. When ordering spares the following
information should be quoted:
1)
Pump serial number.
2)
Pump size.
3)
Part name – taken from section 8.
4)
Part number – taken from section 8.
5)
Number of parts required.
The pump size and serial number are shown on the
pump nameplate.
To ensure continued satisfactory operation,
replacement parts to the original design specification
should be obtained from Flowserve. Any change to
the original design specification (modification or use
of a non-standard part) will invalidate the pump’s
safety certification.
6.3.2 Storage of spares
Spares should be stored in a clean dry area away
from vibration. Inspection and re-treatment of
metallic surfaces (if necessary) with preservative is
recommended at 6 monthly intervals.
6.4 Recommended spares
Recommended spares are defined on the following
basis and contained in the table below and in section 8.
•
Class 1 (S1) – start-up and commissioning spares.
•
Class 2 (S2) – two year spares requirement
covering maintenance for this period.
•
Class 3 (S3) – five year capital spares
requirement.
A multiplier is provided in the last column of the table
for multiple pump purchases, which can be used
where more than one pump is purchased to give the
estimated volume of spares required.
See section 8 for recommended spares
6.5 Tools required
A typical range of tools that will be required to
maintain these pumps is listed below.
Readily available in standard tool kits, and dependent
on pump size:
•
Open ended spanners (wrenches) to suit up to
M 20 screws/nuts
•
Socket spanners (wrenches), up to M 20 screws
•
Allen keys, up to 10 mm (A/F)
•
Range of screwdrivers
•
Soft mallet
•
Thickness feeler gages
6.6 Fastener torques
Fastener size
Torque Nm (lbf•ft)
M8
M10
M12
M16
M20
16 (12)
25 (18)
35 (26)
80 (59)
130 (96)
Non-metallic gaskets incur creep
relaxation - before commissioning the pump check
and retighten fasteners to tightening torques stated.
6.7 Disassembly
Refer to Safety section 1.6 before dismantling
the pump.
Before dismantling the pump for
overhaul, ensure genuine Flowserve replacement
parts are available. Refer to sectional drawings for
part numbers and identification. (See section 8, Parts
lists and drawings.)
a) Close suction and discharge valves and drain
liquid from pump.
b) Remove screws from pump casing and pull motor
and rotating assembly complete from back of
pump casing, which is left connected in the
pipework.
c) Remove the impeller screw and pull off impeller.
(Alternatively, if the pump impeller is fitted with an
inducer, unscrew inducer and inducer stud and pull
off impeller.)
d) These pumps are packed gland as standard. To
complete dismantling, remove the gland nuts, slit
gland and stuffing box cover/mounting bracket
bolts (where fitted). Pull the stuffing box cover
from the mounting bracket and remove packing,
lantern ring and packing seating ring.
e) The mounting bracket (or the adapter where the
mounting feet are on the motor) can now be
separated from the motor after removing the fixing
screws.