Flowserve S-series PolyChem User Manual
Page 18
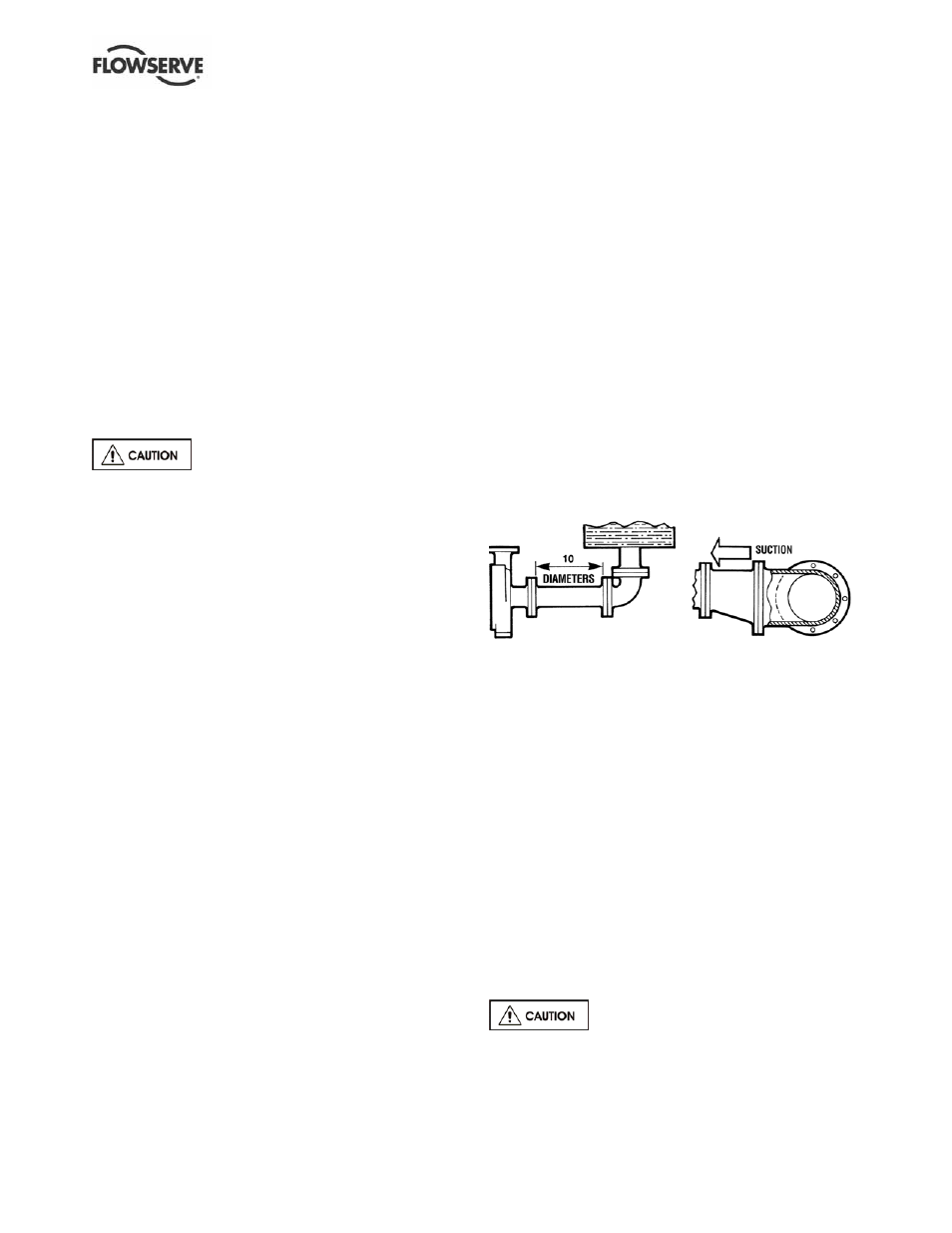
USER INSTRUCTIONS POLYCHEM S-SERIES ENGLISH 71569207 11-08
Page 18 of 52
flowserve.com
h) The parallel and angular vertical alignment is
made by shimming under the motor.
i)
The motor feet holes are again centered on the
motor mounting studs using the centering nut. At
this point the centering nut is removed and
replaced with a standard nut. This gives
maximum potential mobility for the motor to be
horizontally moved during final, field alignment.
All four motor feet are tightened down.
j)
The pump and motor shafts are then aligned
horizontally, both parallel and angular, by moving
the pump to the fixed motor. The pump feet are
tightened down.
k) Both horizontal and vertical alignment is again
final checked as is the coupling spacer gap.
l)
See section 4.8, Final shaft alignment.
4.6 Piping
Protective covers are fitted to both the
suction and discharge flanges of the casing and must
be removed prior to connecting the pump to any pipes.
4.6.1 Suction and discharge piping
All piping must be independently supported, accurately
aligned and preferably connected to the pump by a
short length of flexible piping. The pump should not
have to support the weight of the pipe or compensate
for misalignment. It should be possible to install suction
and discharge bolts through mating flanges without
pulling or prying either of the flanges. All piping must be
tight. Pumps may air-bind if air is allowed to leak into
the piping. If the pump flange(s) have tapped holes,
select flange fasteners with thread engagement at least
equal to the fastener diameter but that do not bottom
out in the tapped holes before the joint is tight.
The following is the recommended procedure for
attaching piping to the PolyChem S-series pump. (See
section 6.6 for torque values.)
a) Check the surface of both flanges (pump/pipe) to
ensure they are clean, flat, and without defects.
b) Lubricate the fasteners.
c) Hand tighten all of the fasteners in a crisscross
pattern.
d) The fasteners should be torqued in increments –
based a crisscross pattern.
The first increment should be at 75% of the
full torque
The second increment should be at the full
torque
Verify that the torque value of the first
fastener is still at the full torque value
e) Retorque all fasteners after 24 hours or after the
first thermal cycle.
f)
Retorque all fasteners at least annually
4.6.2 Suction piping
To avoid NPSH and suction problems, suction piping
must be at least as large as the pump suction
connection. Never use pipe or fittings on the suction
that are smaller in diameter than the pump suction size.
Figure 4-7 illustrates the ideal piping configuration with a
minimum of 10 pipe diameters between the source and
the pump suction. In most cases, horizontal reducers
should be eccentric and mounted with the flat side up as
shown in Figure 4-8 with a maximum of one pipe size
reduction. Never mount eccentric reducers with the flat
side down. Horizontally mounted concentric reducers
should not be used if there is any possibility of entrained
air in the process fluid. Vertically mounted concentric
reducers are acceptable. In applications where the fluid
is completely de-aerated and free of any vapor or
suspended solids, concentric reducers are preferable to
eccentric reducers.
Figure 4-7 Figure 4-8
Avoid the use of throttling valves and strainers in the
suction line. Start up strainers must be removed shortly
before start up. When the pump is installed below the
source of supply, a valve should be installed in the
suction line to isolate the pump and permit pump
inspection and maintenance. However, never place a
valve directly on the suction nozzle of the pump.
Refer to the Durco Pump Engineering Manual and
the Centrifugal Pump IOM Section of the Hydraulic
Institute Standards for additional recommendations
on suction piping. (See section 10.)
Refer to section 3.4 for performance and operating
limits.
4.6.3 Discharge piping
Install a valve in the discharge line. This valve is
required for regulating flow and/or to isolate the pump
for inspection and maintenance.
When fluid velocity in the pipe is high,
for example, 3 m/s (10 ft/sec) or higher, a rapidly
closing discharge valve can cause a damaging
pressure surge. A dampening arrangement should
be provided in the piping.