Flowserve MF User Manual
Page 20
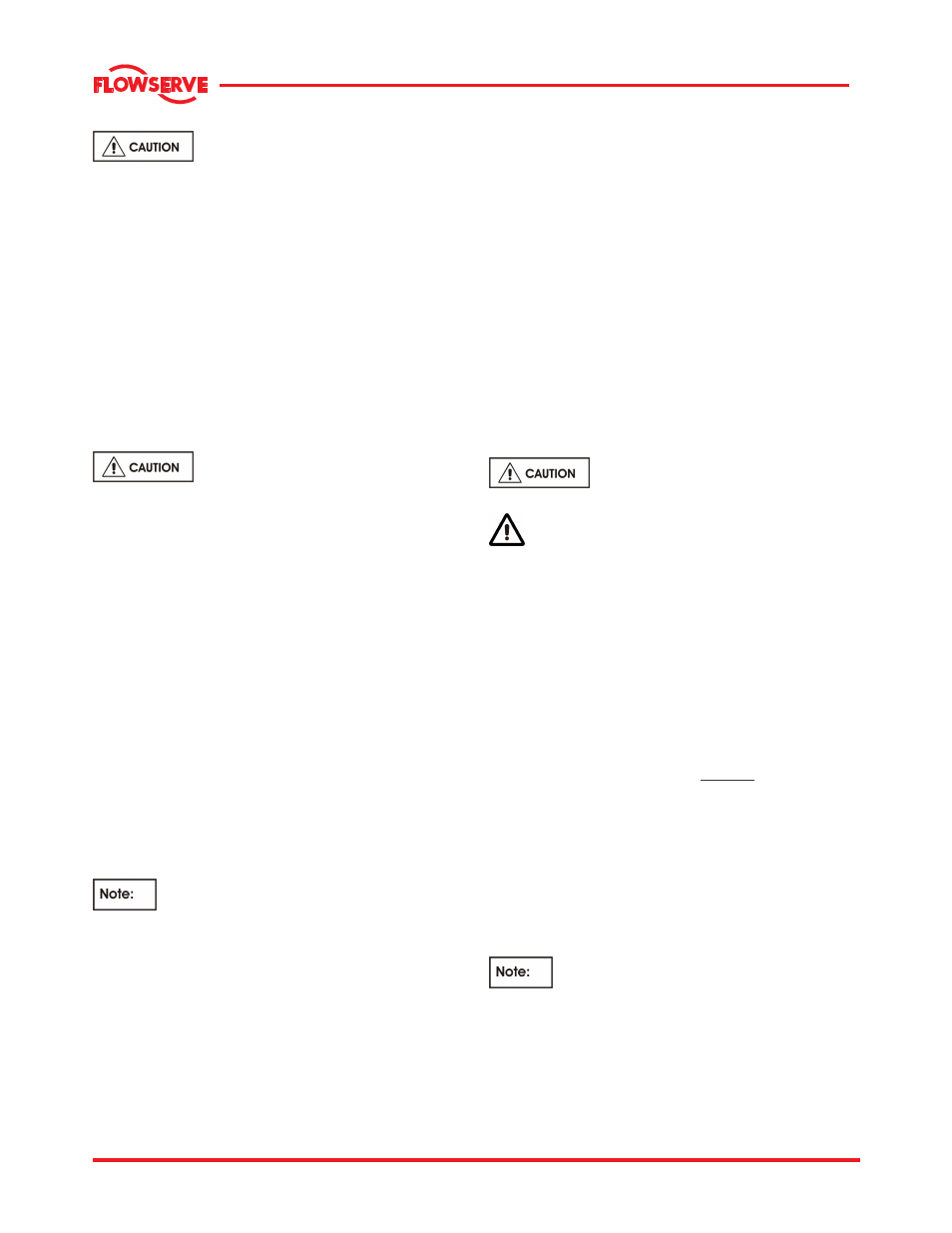
MF USER INSTRUCTIONS ENGLISH 71569191 12/04
Page 20 of 50
®
4.6 Piping
Protective covers are fitted to the pipe
connections to prevent foreign bodies entering during
transportation and installation. Ensure that these
covers are removed from the pump before
connecting pipes.
4.6.1 Pipework velocities
In order to minimize friction losses and hydraulic
noise in the pipework it is good practice to choose
pipework that is one or two sizes larger than the
pump suction and discharge. Typically main
pipework velocities should not exceed 2 m/s (6 ft/sec)
suction and 3 m/s (9 ft/sec) on the discharge
.
Take into account the available NPSH that must be
higher than the required NPSH of the pump.
Never use the pump as a support for
piping.
4.6.1.1 Piping strains
Pipe strains are a common cause of misalignment,
hot bearings, worn couplings, and vibrations.
Satisfactory operation cannot be maintained when
the piping imposes a force on the pump. Misaligned
piping flanges can spring and pull a pump out of
position when their bolts are drawn up.
Flanges must have flat faces and be brought
squarely together before the bolts are tightened.
To avoid breaking the flanges when tightening the
bolting, mating pipe flanges should also have flat
faces and full face gaskets should be used.
Suction and discharge pipes, and associated
equipment, should be supported and anchored near,
but independent of the pump so that no strain will be
transmitted to the pump casing.
Pipe couplings that are not axially rigid are
sometimes used in the discharge and/or suction
piping to avoid transmitting any piping strains caused
by system pressure, thermal expansion, or pipe
misalignment. Such pipe couplings allow transmittal
to the pump, a force equal to the area of the
expansion joint times the pressure in the piping.
These forces can have a significant magnitude and it
is impractical to design the pump casing, base plate,
support, etc., to withstand them.
Consequently, when pipe couplings lack axial rigidity,
a suitable pipe anchor must be installed. Alternately,
adequate restraining devices should be used and
properly adjusted to prevent these forces from being
transmitted to the pump. Maximum forces and
moments allowed on the pump flanges vary with the
pump size and type.
To minimize these forces and moments that may, if
excessive, cause misalignment, hot bearings, worn
couplings, vibration and the possible failure of the
pump casing, the following points should be strictly
followed:
•
Prevent excessive external pipe load
•
Never draw piping into place by applying
force to pump flange connections
•
Do not mount expansion joints so that their
force, due to internal pressure, acts on the
pump flange
Ensure piping and fittings are flushed
before use.
Ensure piping for hazardous liquids is arranged
to allow pump flushing before removal of the pump.
4.6.2 Suction piping
Experience has shown that the major source of
trouble in centrifugal pump installations, other than
misalignment, is traceable to a faulty suction line.
The utmost attention must be given to this portion of
the installation to ensure that the pump receives
hydraulically stable flow. The suction piping should
be direct as possible and its length held to a
minimum. If a long suction line is required, increase
the pipe size to reduce friction losses. Then
gradually reduce the pipe size in steps before
entering the pump. The piping should be run without
having high spots and should have a continual rise
toward the pump. This prevents formation of air
pockets.
Clean out all debris from the suction line and wet well
prior to operating the pumps. Care should be
exercised to keep the suction piping air tight and
sealed against leakage
Isolation valve in suction line is strongly
recommended to facilitate future servicing needs. An
isolation valve is recommended in the suction line, if
a positive head exists.