Flowserve 1400 Valtek Logix User Manual
Page 15
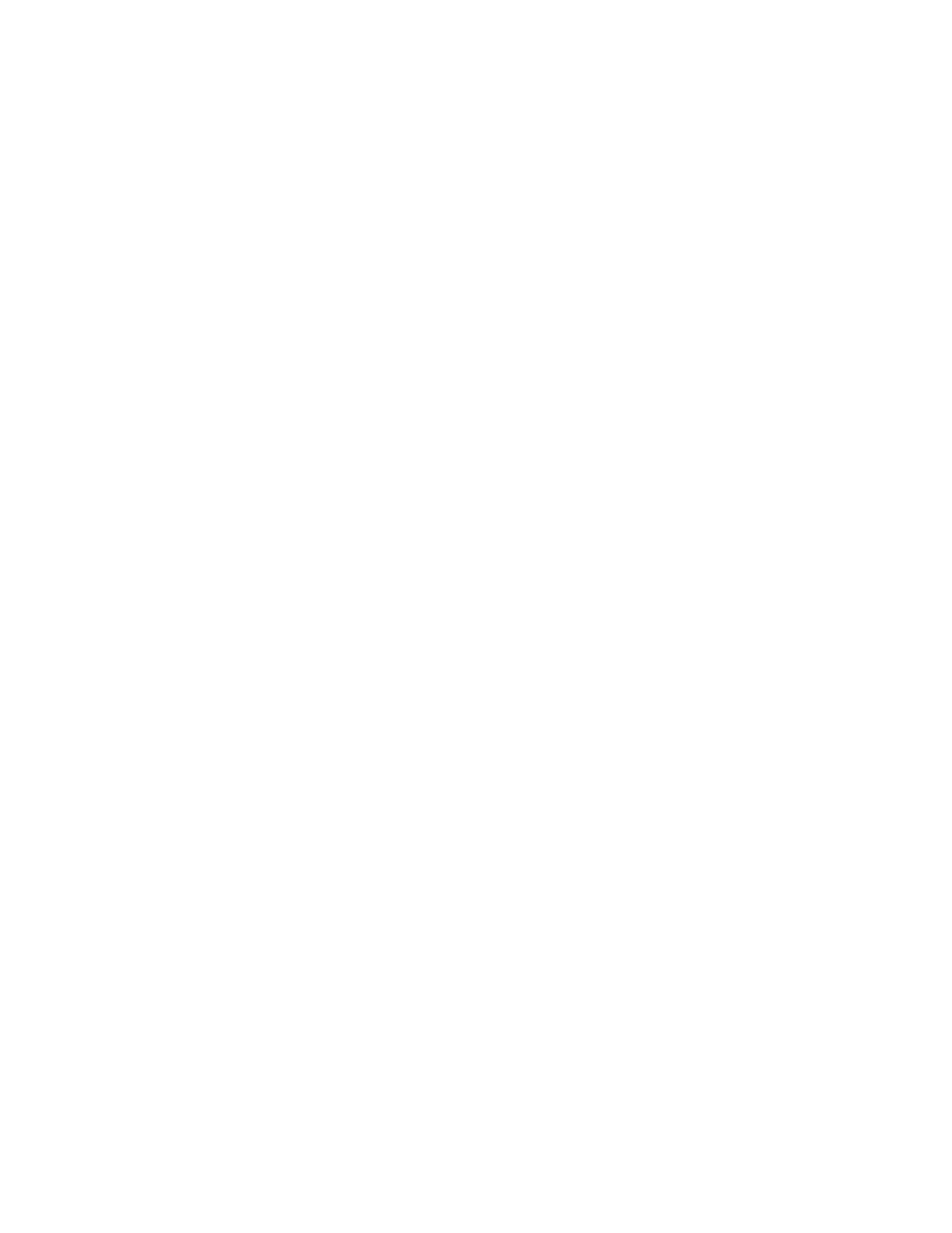
46-15
Flowserve Corporation, Valtek Control Products, Tel. USA 801 489 8611
Mounting and Installation
Electrical Wiring
Verify polarity when making field termination connection.
With a fieldbus power supply connected, verify that an
LED is blinking to determine if the electronics are
running. Only one LED will blink at any given time.
Compatibility with DCSs using 24VDC
FB specifies a 9-32V operation range. A fieldbus com-
patible power supply with terminators should be used to
power a Logix 14xx digital positioner with a DCS using
9 - 32 VDC.
Reverse polarity protection
The Logix 14xx digital positioner is reverse polarity
protected. Inadvertent reversing of the voltage supply
across the Logix 1400 digital positioner should not
damage the device, if current is limited.
Air Action
Air-to-open and air-to-close are determined by the actua-
tor tubing, not the software. When air action selection is
made during configuration, the selection is telling the
control which way the actuator is tubed. Verify that tubing
is correct prior to a stroke calibration. The top output port
on the positioner is called
output 1. It should be tubed to
the increase open side of the actuator. That is, for an air-
to-open actuator,
output 1 should go to the bottom of the
actuator.
Linear vs. Rotary
The positioner has two configuration settings: Linear and
rotary. To achieve better resolution, stem position sen-
sor gains are adjusted based on the angle of rotation of
the linkage. The linear setting allows for linkage rotation
up to 65 degrees. The rotary setting allows for linkage
rotation up to 95 degrees. These settings only determine
the angle of sensor rotation and do not affect control
parameters. If a positioner is set to linear linkage and a
red LED blinks after calibration, the most common cause
is that the sensor movement was greater than 65 de-
grees. This can occur if the roller pin was placed in the
wrong hole on the follower arm or the stem clamp is
placed too high. The take-off arm should always be level
with the stem clamp on linear mountings.
The Logix 14xx positioner has an electrical measure-
ment range of 95 degrees. That is, the electronics will
sense stem position over a 100 degrees range of travel
of the follower arm. On a rotary valve, the typical rotation
is 90 degrees. When installing a Logix 14xx positioner on
a rotary valve, it is important that the 90 degrees valve
rotation is centered within the 95 degrees electrical
range. If mechanical movement falls outside the electri-
cal measurement range, the positioner can have a dead-
band at one end of travel in which valve movement
cannot be sensed.
the stem begins to move. The stem movement reduces
the deviation between control command and stem posi-
tion. This process continues until the deviation goes to
zero. The control algorithm is both proportional and
integral. This algorithm will be further explained later in
this document.
A more detailed example to explain the control function
follows. The following configuration exists.
• Unit will receive its command from the FB.
• Custom characterization is disabled (therefore char-
acterization is linear).
• Soft limits or FINAL_VALUE_CUTOFF are disabled.
• Valve has zero deviation with a present input com-
mand of 50 percent.
Actuator is tubed Air-to-Open
Given these conditions, 50 percent represents a com-
mand of 50 percent. Custom characterization is disabled
so the command is passed 1:1 to the CMD_USED. Since
zero deviation exists, the stem position is also at 50
percent. With the stem at the desired position, the spool
valve will be at a position in which no air flow is allowed
to either side of the actuator. This is commonly called the
null or balanced spool position. Now, change the com-
mand from 50 percent to 75 percent. The positioner sees
this as a FINAL_VALUE command of 75 percent. With
linear characterization, the CMD_USED becomes 75
percent. Deviation is the difference between the control
command (CMD_USED) and Stem Position: Deviation =
75 percent - 50 percent = +25 percent, where 50 percent
is the present stem position. With positive deviation, the
control algorithm sends a signal to move the spool up
from its present position. As the spool moves up, the
supply air is applied to the bottom of the actuator and air
is exhausted from the top of the actuator. This new
pressure differential causes the stem to start moving
towards the desired position of 75 percent. As the stem
moves, the deviation begins to decrease. The control
algorithm begins to reduce the spool opening. This
process continues until the deviation goes to zero. At
this point, the spool will be back in its
null or balanced
position. Stem movement will stop. Desired stem posi-
tion has now been achieved.
One important parameter should now be discussed point:
Inner-loop offset. A number called inner-loop offset
(IL_OFFSET) is added to the output of the control
algorithm. (Refer to Figure 16.) For the spool to remain in
its
null or balanced position, the control algorithm must
output a non-zero spool command. This is the purpose of
the inner-loop offset. The value of this number is equiva-
lent to the signal that must be sent to spool position
control to bring it to a
null position with zero stem
deviation. This parameter is important for proper control
and will be discussed further in the
Control and Tuning
section.