Reversing air-action on rotary actuators, Converting positioner input signal, Calibration – Flowserve Valtek Beta Positioners for Control Valves User Manual
Page 7: Calibrating positioner zero and span
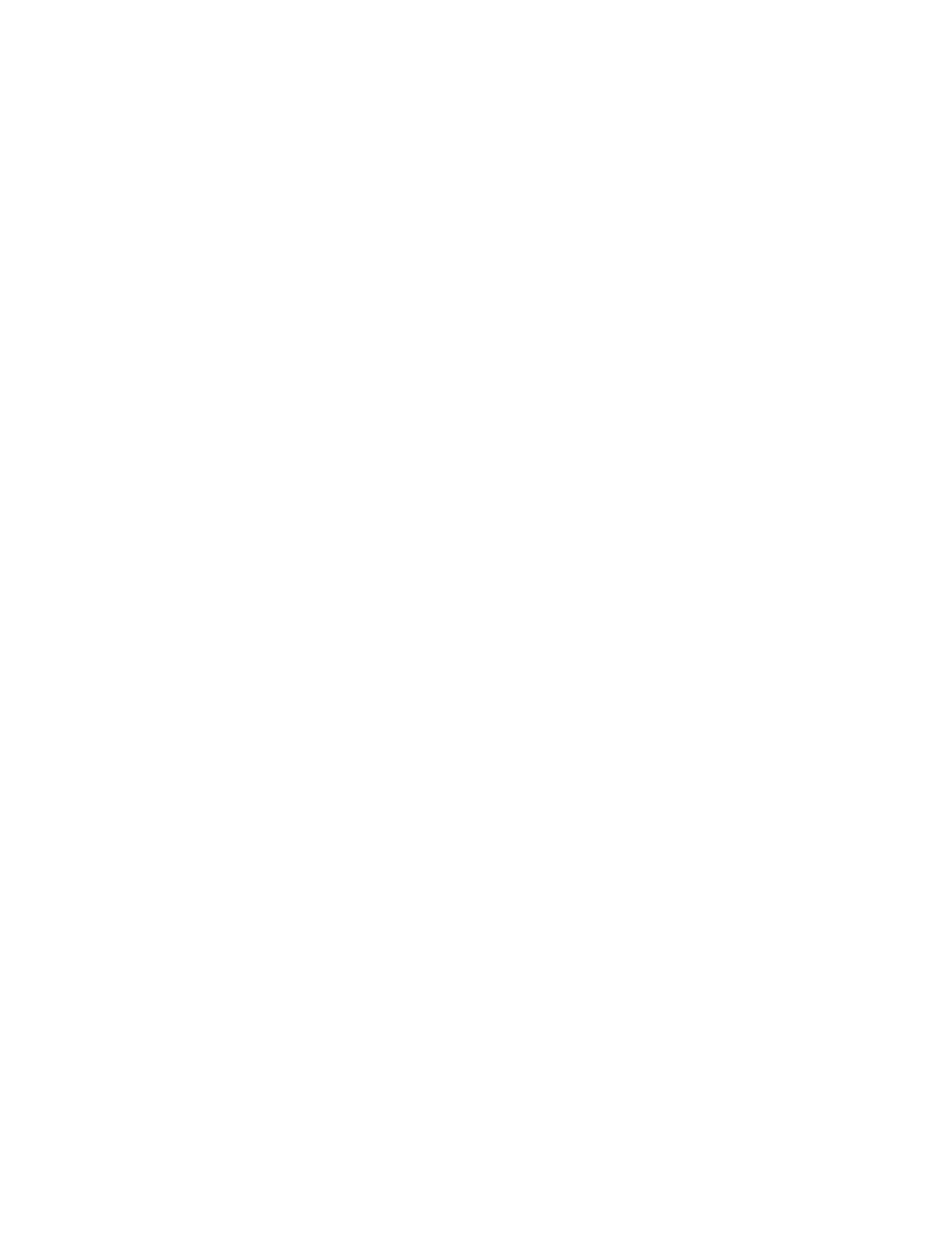
24-7
Flowserve Corporation, Valtek Control Products, Tel. USA 801 489 8611
of the cam shaft nut (59). Slide the cam shaft nut
(59) through the outer bearing and screw it onto the
cam shaft (57). Tighten the cam shaft together
firmly so that the follower arm (58) is securely
clamped. Also, make sure the cam (56) is tightly
secured to the cam shaft. Check to be sure there is
no slippage. Apply a small amount of grease to the
bent end of the return spring (18) and feed it through
the hole in the cam (56). Loop the other end of the
return spring over the screw (19) and screw it into
the positioner base.
NOTE: Screw head will not bottom out.
5. Replace the range adjustment arm (13) and its snap
ring (8).
6. Rotate the zero adjustment arm (22) back into place
and reinstall the feedback spring (34).
7. Insert the follower pin (62) into the hole in the
actuator lever arm and drive it firmly into place with
a hammer (see Figure 8).
8. Apply grease to the sliding surfaces of the follower
arm (58) before mounting the positioner to the
transfer case. When mounting the positioner to the
transfer case, make sure to guide the follower arm
(58) so the pin slides in the slot on the follower arm
(see Figure 8). Fasten the positioner to the transfer
case with the three mounting screws. Push up on
cam to verify that the pin is riding in the follower arm
slot or remove the transfer case cover plate to
inspect.
CAUTION: Failure to replace the cover-plate
before operating the actuator will cause dam-
age to the shaft since the coverplate houses a
shaft support bearing.
Depending on the positioner cam side selected, the
rotation of the valve shaft may be linear or equal
percent when compared to the instrument signal
to the positioner. Figures 13 through 16 show the
shaft rotation versus instrument signal of a valve
(Valdisk, MaxFlo or ShearStream). These graphs
should be used when visually checking the valve
shaft rotation versus positioner signal relationship.
Reversing Air-Action on Rotary Actuators
Reversing the action on rotary actuators is achieved by
mounting the yoke to the opposite side of the transfer
case. Refer to Installation, Operation, Maintenance
Instructions 10, Valdisk Control Valves; Installation,
Operation, Maintenance Instructions 27, ShearStream
Control Valves; Installation, Operation, Maintenance
Instructions 31, Rotary Actuators; or Installation, Opera-
tion, Maintenance Instructions 39, MaxFlo Control
Valves.
Converting Positioner Input Signal
Converting a Beta positioner’s input signal from an I/P to
pneumatic or pneumatic to I/P control signal is accom-
plished by unbolting the existing input signal module
and replacing it with the other (either an I/P module or a
pneumatic module). The part numbers for these mod-
ules are found in the “Ordering Information” section of
this bulletin.
Calibration
Procedures for calibrating both rotary and linear actua-
tors are the same.
Valtek positioners mounted on valves are calibrated at
the factory; however, due to shipping and handling, it
may be necessary to check the calibration before oper-
ating the valve. There are three feedback springs (34)
available for use in the Beta Positioner, depending on
the valve stroke and split range required. The silver
spring (standard) is used with standard stroke actuators
and provides one or two-way split ranges (3-15, 3-9, 9-
15 with the pneumatic module, or ranges of 4-20, 4-12,
12-20 mA with the I/P module). A red spring is used with
short stroke actuators (
1
/
2
-inch on 25 or 50 square-inch
actuators,
3
/
4
and 1-inch strokes on 100 square-inch
actuators) and provides one, two, or three-way split
ranges. A green spring provides three or four-way split
ranges on standard stroke actuators.
WARNING: When stroking the actuator during cali-
bration, be sure to keep hands, hair, and clothing
away from moving parts. Failure to do so can cause
serious personal injury.
Calibrating Positioner Zero and Span
For Calibration, see Figure 7 and proceed as follows:
1. For standard ranges (3-15 psi, 4-20 mA), loosen the
zero adjustment locking knob (23) and adjust the
zero adjustment knob (20) until the valve begins to
stroke at just over the desired zero point (usually 3
psi pneumatic, 4 mA electrical).
2. Loosen range adjustment locking screw (9) about
1
/
8
turn.
3. With a screwdriver, turn the range adjustment gear
(12) so that the valve is at full stroke at just under the
desired maximum range point (usually 15 psi pneu-
matic, 20 mA electrical).
4. Return to minimum signal (usually 3 psi pneumatic,
4 mA electrical) and check the zero. Repeat steps
1 - 4 if necessary.
5. Tighten the range adjustment locking screw (9).
6. Tighten the zero adjustment locking screw (23).