Flowserve Valtek MaxFlo 3 User Manual
Page 4
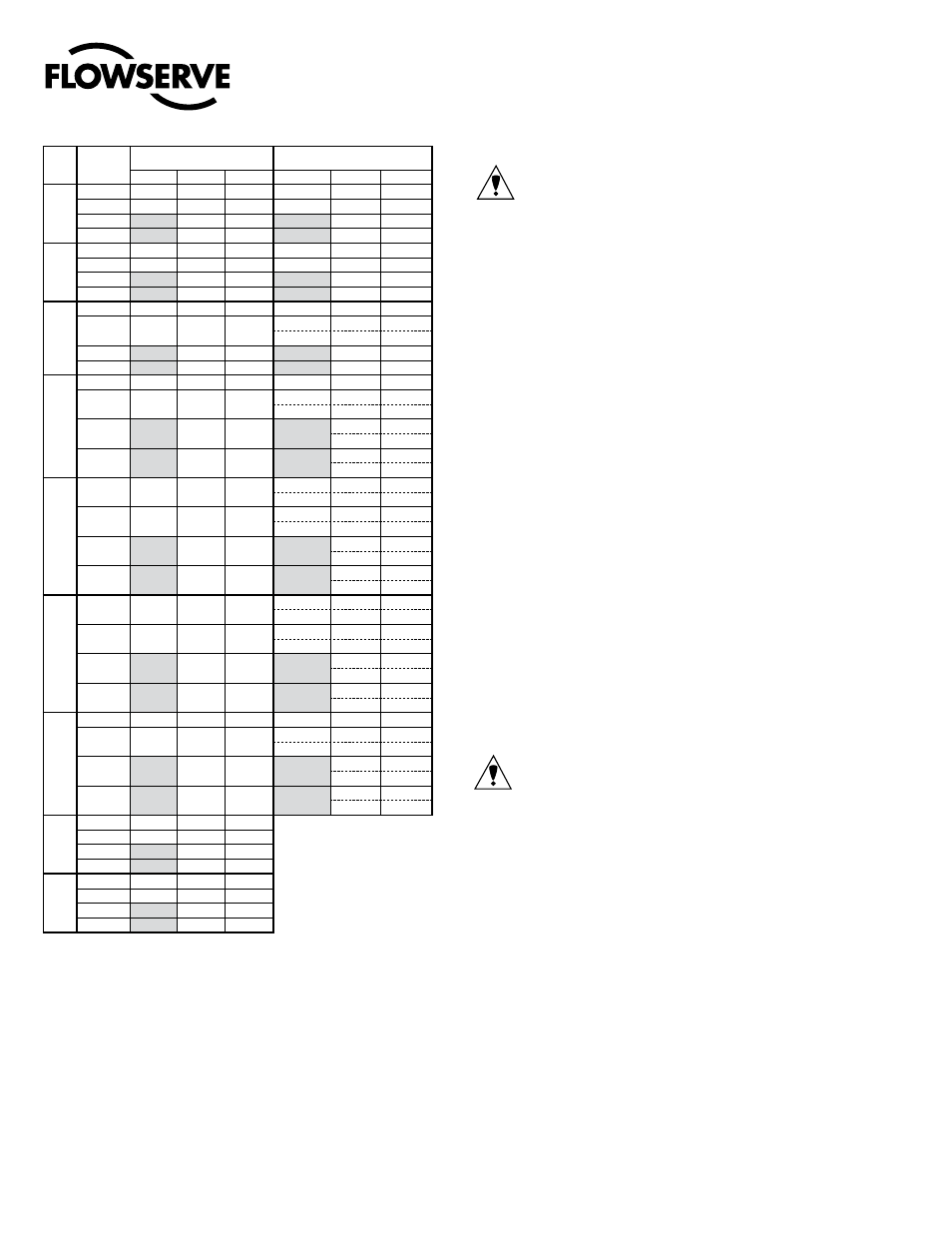
®
User instructions - MaxFlo 3 - VLENIM0052-02 02.07
4
Table I: Line Flange Bolting Specifications
4
QUICK-CHECK
Before commissioning, check the control valve by fol-
lowing these steps:
4.
Check for full stroke by varying the instrument signal
settings appropriately. Observe the plug position in-
dicator located on the actuator or the positioner. The
plug should change position with a smooth turning
movement.
4.
Check all air connections for leaks. Tighten or replace
any leaking lines.
4.3
Check packing box bolting for proper tightness.
CAUTION: Do not overtighten packing. This can cause
excessive packing wear and high stem friction that may
impede shaft movement. After the valve has been in serv-
ice for a short period, recheck the packing-box nuts. If
the packing-box leaks, tighten the nuts just enough to
stop the leak.
4.4
Make sure the valve fails in the correct direction in case
of air failure. This is done by positioning the valve at mid-
stroke and turning off the air supply and observing the
failure direction. If the action is incorrect, see the sec-
tion “Reversing the Air-action” in the instructions of the
installation, operation and maintenance manual of the
appropriate actuator.
5
PREVENTATIVE MAINTENANCE
At least once every six months, check for proper op-
eration by following the preventative maintenance steps
outlined below. These steps may be performed while the
valve is in-line and without interrupting service. If an in-
ternal problem is suspected, refer to section “Valve Dis-
assembly”.
5.
Look for signs of gasket leakage through the end flanges
and bonnet. If necessary, re-torque flange, bonnet and
post bolting.
5.
Examine the valve for damage caused by corrosive fumes
or process drippings.
5.3
Clean the valve and repaint areas of severe oxidation.
5.4
Check the packing-box for proper tightness. If there is
a persistent leak, change the packing after referring to
sections “Valve Disassembly and Body Reassembly”.
CAUTION: Do not overtighten packing. This can cause
excessive packing wear and high friction that may im-
pede shaft movement.
5.5
If the valve is equipped with a lubricator, add lubricant if
necessary.
5.6
If possible, stroke the valve and check for smooth, full-
stroke operation. Unsteady shaft movement may indicate
an internal valve problem.
5.7 Check the calibration of the positioner. For further pre-
ventative maintenance, see the instructions in the instal-
lation, operation and maintenance manual for the appli-
cable positioner.
5.8
Ensure all accessories, brackets and bolting are securely
fastened.
5.9
If possible, remove air supply and observe actuator for
correct fail-safe action.
5.0 Check the actuator and all air connections for leaks.
5. If an air filter is supplied, check and replace the cartridge
if necessary.
Valve
size
Nominal
Pressure /
Rating
MaxFlo 3 flanged
Size x Length
MaxFlo 3 flangeless
Size x Length
Inches
Metric
Qty/ valve
Inches
Metric
Qty/ valve
DN5
"
ANSI 50
/ X .6 M X 65
8
/ X 6.75
M X 70
4
ANSI 300
5/8 X 3. M6 X 80
8
5/8 X 6.88
M6 X 75
4
PN 6
M X 70
8
M X 75
4
PN 40
M X 70
8
M X 75
4
DN40
½"
ANSI 50
/ X .88 M X 70
8
/ X 7.50
M X 90
4
ANSI 300
3/4 X 3.6 M0 X 95
8
3/4 X 8.38
M0 X 5
4
PN 6
M6 X 80
8
M6 X 00
4
PN 40
M6 X 80
8
M6 X 00
4
DN50
"
ANSI 50
5/8 X 3.5 M6 X 85
8
5/8 X 8.38
M6 X 5
4
ANSI 300
5/8 X 3.5
M6 X 90
6
5/8 X 3.50
M6 X 90
4
5/8 X 8.50
M6 X 0
6
PN 6
M6 X 85
8
M6 X 5
4
PN 40
M6 X 85
8
M6 X 5
4
DN80
3"
ANSI 50
5/8 X 3.6 M6 X 95
8
5/8 X 0.5
M6 X 65
4
ANSI 300
3/4 X 4.5 M0 X 0
6
3/4 X 4.5
M0 X 0
4
3/4 X .00
M0 X 80
6
PN 6
M6 X 85
6
M6 X 85
6
M6 X 55
5
PN 40
M6 X 95
6
M6 X 95
6
M6 X 65
5
DN00
4"
ANSI 50
5/8 X 3.6 M6 X 95
6
5/8 X 3.6
M6 X 95
4
5/8 X .5
M6 X 95
6
ANSI 300
3/4 X 4.5 M0 X 5
6
3/4 X 4.5
M0 X 5
4
3/4 X .5
M0 X 35
6
PN 6
M6 X 85
6
M6 X 85
6
M6 X 85
5
PN 40
M0 X 00
6
M0 X 00
6
M0 X 300
5
DN50
6"
ANSI 50
3/4 X 3.75 M0 X 05
6
3/4 X 3.75
M0 X 05
4
3/4 X 3.5
M0 X 340
6
ANSI 300
3/4 X 4.88 M0 X 5
4
3/4 X 4.88
M0 X 5
8
3/4 X 4.00
M0 X 360
8
PN 6
M0 X 00
6
M0 X 00
4
M0 X 335
6
PN 40
M4 X 5
6
M4 X 5
4
M4 X 350
6
DN00
8"
ANSI 50
3/4 X 4.5 M0 X 0
6
3/4 X 4.5
M0 X 360
8
ANSI 300
7/8 X 5.5 M X 40
4
7/8 X 5.5
M X 40
4
7/8 X 5.9
M X 390
0
PN 6
M0 X 00
4
M0 X 00
8
M0 X 350
8
PN 40
M7 X 35
4
M7 X 35
8
M7 X 385
8
DN50
0"
ANSI 50
7/8 X 4.6 M X 0
4
ANSI 300
X 6.5
M4 X 55
3
PN 6
M4 X 0
4
PN 40
M30 X 50
4
DN300
"
ANSI 50
7/8 X 4.75 M X 0
4
ANSI 300
/8 X
M7 X 70
3
PN 6
M4 X 5
4
PN 40
M30 X 60
3