Flowserve Valtek StarPac 1 Intelligent Control Systems User Manual
Page 11
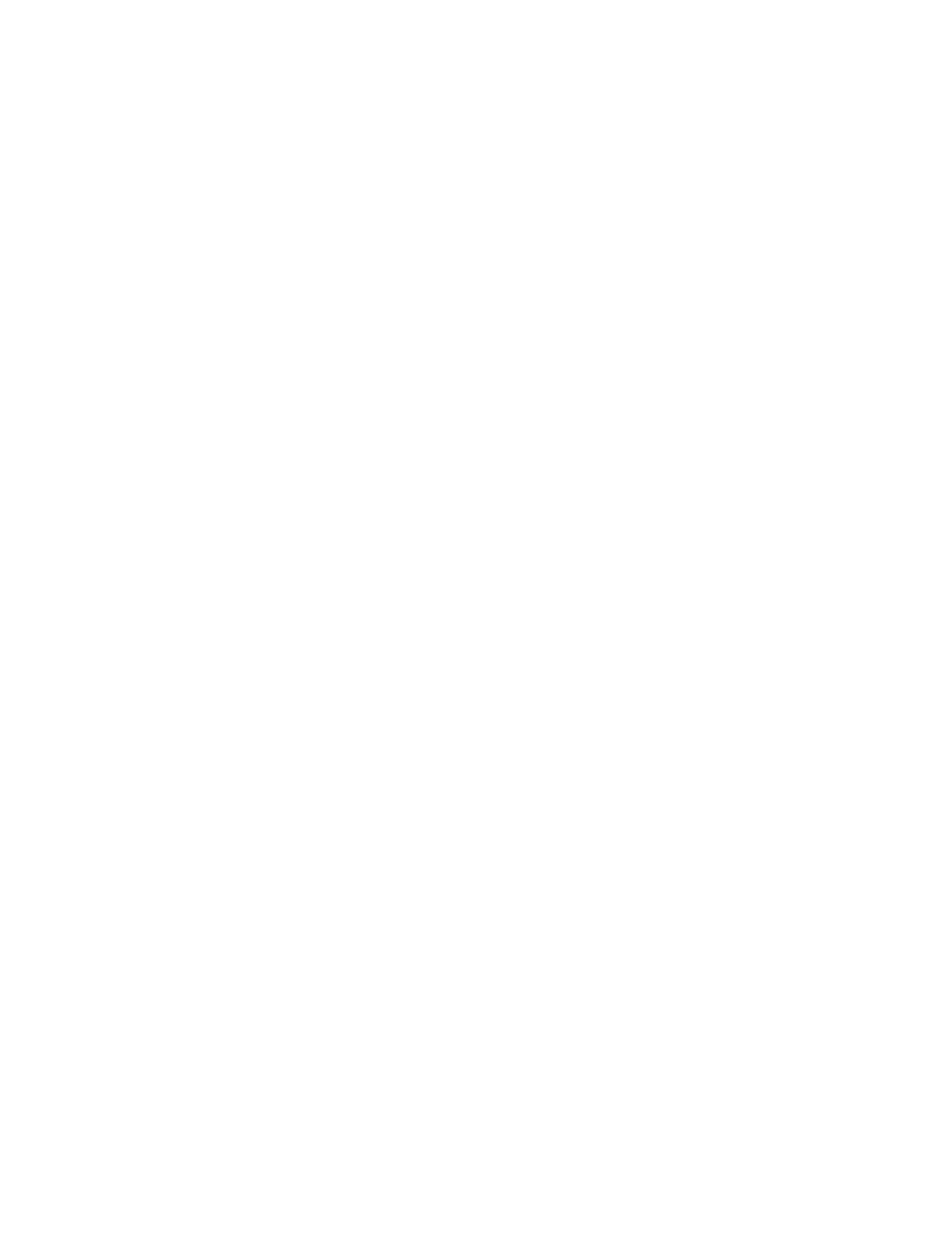
41-11
Flowserve Corporation, Valtek Control Products, Tel. USA 801 489 8611
them into the standoffs and hold the board in place.
The board is properly seated when the pressure
standoffs are almost flush against the bottom of the
board.
CAUTION: Do not twist or bend the board once
the nipples are plugged in or they may break.
Using one of the assembly screws to hold the
board in alignment while attaching the other
wires and boards will help prevent this.
13. Attach the I/P cable wires to the two-screw terminal
block marked 'I/P,' (red wire to the positive terminal
and black wire to the negative terminal). Notice that
this is a plug-in terminal block and may be un-
plugged without removing the wires.
14. Detach the second NT board from the new stack.
Attach the three-wire hallpot harness from the new
stack into the hallpot connector. The small 'ears' on
the outer edges of the new brown plug should point
to the outside edge of the hallpot.
15. Plug the process sensor connector into the J4
connector on the bottom of this board. On older
StarPac models this connector is a single soldered
eight-pin connector. The more recent models have
two sensor cables which are terminated separately
with crimped on pins and a brown housing. For the
separated cable arrangement, be sure to plug the
correct sensor into the correct half of the board
connector (P
1
to P
1
and P
2
to P
2
section).
16. Plug the board into the bottom board mounted on
the base while making sure all pins are aligned.
Use an assembly screw to temporarily hold the
board in place.
17. Attach the thermocouple wires to the two-screw
terminal block on this board, noting the correct
polarity. Red wire to 'R' and yellow wire to 'Y.' If
additional wire length is needed, gently pull more
wire from the base. Also, bend the wires close to
the terminal block (excessive looping is not needed
due to the notches cut in the boards).
18. Plug in the remaining boards. (Be sure to check the
alignment of the pins.) Secure the board stack
together by placing the one spacered assembly
screw in the upper right hand corner.
19. Set the dip switches on the digital board to match
the settings on the old board stack.
NOTE: This step does not apply when upgrading
from the DataStream model.
20. Reaffirm that all connections are properly aligned
and secure.
21. Reattach field wiring to the user interface terminals.
22. Apply 24 VDC power. The liquid crystal display
should display the version number and then the
default display mode.
23. Establish communications and use the StarTalk
software to upload the saved .CCT file for this
system into the new NT module. (If updating from
an older StarPac DataStream model, use the file
conversion utility to convert the old .TBL file into a
compatible Modbus file.)
24. With the air supply shut off, the valve should be
either fully closed or fully opened, depending on the
failure spring action ordered. Use the configuration
menu to set the LCD to display the position continu-
ously. Rotate the hallpot shaft until the displayed
value for position is within a few percentages of
either zero percent (if the valve is closed) or 100
percent (if the valve is open). Tighten the hallpot
connector set screw. (
Alternate method: If access
to the set screw is difficult due to the alignment of
the takeoff arm, connect the air supply and stroke
the valve 50 or 100 percent open as indicated on
the valve stroke plate. Adjust the hallpot shaft to an
indicated position reading of 50 or 100 percent,
then tighten the set screw. Care must be taken if
this method is used to ensure that the ADC values
of the position feedback do not go out of range at
either end of stroke.) Once this has been adjusted
correctly, if the boardstack needs to be replaced,
redoing the setting is not needed unless the hallpot
itself is damaged.
NOTE: If the position values displayed decrease
rather than increase when the valve strokes open,
the three-wire hallpot connector is reversed and
needs to be unplugged and rotated 180
°
.
25. Replace the plastic shroud and the remaining two
assembly screws. Make sure all wiring is beneath
the shroud and that no wires are trapped between
the bottom board and the vibration isolators in
which the assembly screws attach.
26. Turn the air supply back on to the actuator.
27. After verifying that stroking the valve is safe, use
the calibration menu to first recalibrate the actuator
pressure sensor, and then perform a valve stroke
calibration. During this calibration, watch the posi-
tion ADC values to ensure that the hallpot adjust-
ment is not at its limit on either end of stroke. (If
needed, readjust the hallpot shaft setting to keep
the shaft rotation within the operating range of the
hallpot, then recalibrate.)
28. Secure both the large electronics and the smaller
interface covers.
29. Use the StarTalk software to calibrate the process
sensors and verify the other operational param-
eters of the system.
Do not forget to reconfigure the
LCD to display the desired variables.
30. Return the system to operation.