Flowserve Valtek StarPac 1 Intelligent Control Systems User Manual
Page 12
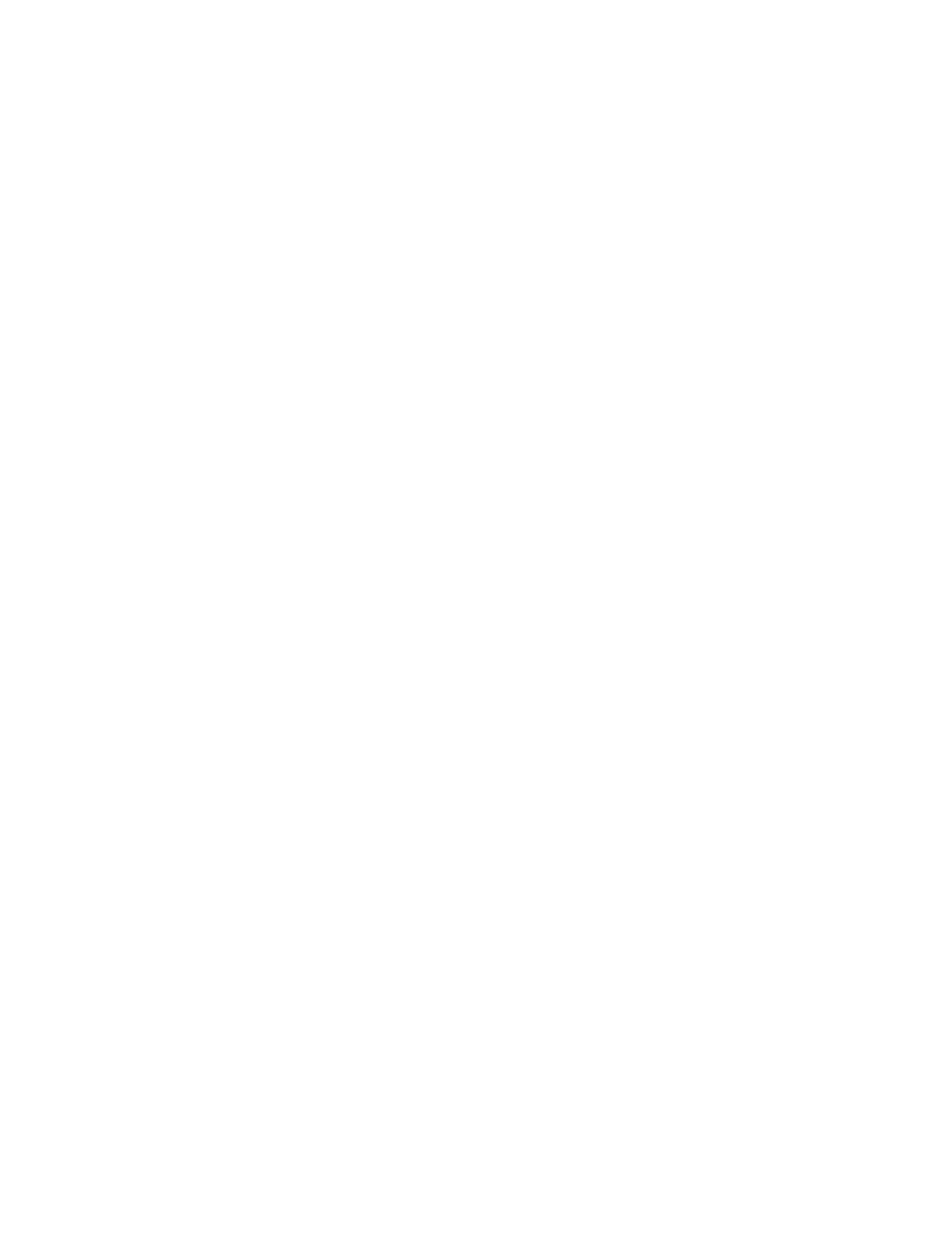
41-12
Flowserve Corporation, Valtek Control Products, Tel. USA 801 489 8611
SYSTEM MAINTENANCE
Flowserve recommends that the StarPac system cali-
bration and maintenance work be done once every six
months. If after checking the calibration of the StarPac,
a component is determined to be defective the following
section will help with the component replacement.
The following items may be needed to install, start up
and calibrate the StarPac system electronics.
• Power supply: 24 VDC regulated
±
2.4 VDC, 300 mA
• StarTalk software (proper version for the electron-
ics being used)
• Computer with internal or external RS-485 commu-
nication adapter
• RS-485 connection cable
• Digital volt meter with 4 - 20 mA range
• Air supply: 50 psig (3.4 bar) minimum, 80 - 100 psig
(6.3 - 7.8 bar) preferred; coalescing air filter required
• Gauges or the ability to accurately determine pro-
cess pressures and valve air supply pressures
• 4 - 20 mA command source
• Thermocouple calibrator or simulator with 0 - 932
°
Fahrenheit (0 to 500
°
Celsius) range
Mechanical Subsystem Maintenance
Refer to the appropriate Flowserve Installation, Opera-
tion & Maintenance (IOM) instructions for details on the
repair and maintenance of the control valve positioner
and actuator components. Please refer to the manufac-
turers’ manuals for maintenance and operation instruc-
tions for non-pneumatic actuators, e.g., electric or
electro-hydraulic actuators.
At first glance the additional tubing and connections of
the StarPac system may appear to make standard
valve maintenance more difficult and complex. The
following instructions will show a maintenance method
that will make this task much easier. Please note that
most of the additional tubing attached to the StarPac
system is electrical conduit and does not contain pro-
cess fluid.
WARNING: The process line must be depressur-
ized and drained of process fluid, and decontami-
nated prior to working on the internal valve compo-
nents. Failure to do so may cause serious injury to
personnel.
1. Depressurize the line, decontaminate the valve (if
needed) and shut off the air supply to the valve
positioner.
2. Disconnect the four actuator air tubes from the
positioner and StarPac system.
3. Disconnect the four mounting bolts that attach the
StarPac system bracket and positioner bracket.
4. Disconnect the follower arms from the StarPac
base and positioner. This is done by removing the
follower arm nut and washer and pulling the arm off
the shaft. Notice that this shaft connection is keyed
and that the shafts are slightly spring loaded.
5. The actuator subassembly is now isolated and is
removed by loosening the bonnet bolts and lifting
the actuator away from the body.
The StarPac system tubing holds the StarPac base
and positioner in place, eliminating the need to
disconnect wiring or air connections.
6. Standard valve maintenance may now be done on
the actuator or valve body components. Refer to
the Flowserve IOM instructions for details on such
things as trim or packing replacement. If the trim
needs to be replaced, use the same trim number
and characteristic as the original trim, or the flow
calculations could be affected. If a trim size change
is needed, contact a Flowserve representative to
find out about flow calibration options.
7. Reassemble the system by reversing the above
steps. Be sure to follow the procedures outlined in
the Flowserve IOM instructions for valve reassem-
bly. Make sure when reconnecting the follower
arms that the arms fit correctly on the keyed shafts
and have a positive spring action.
8. Turn on the air supply to the valve and check for
leaks in the reattached actuator tubing lines. Check
the calibration of the positioner for proper opera-
tion. Refer to Flowserve IOM 24 instructions for
details on calibrating the Beta positioner.
9. Turn on power to the StarPac system. Use the
StarTalk software to check the system calibration
and do a valve stroke calibration to reset the
StarPac’s position feedback. Refer to the Calibra-
tion section of the StarPac manual.
Position Feedback System
The position feedback linkage of the StarPac system is
a critical part of the flow metering ability of the system.
This linkage is used to calculate the valve’s C
V
for a
given stroke. This linkage should be lubricated and
checked periodically for tight, smooth operation. The
follower arm should operate smoothly with no binding
and have a positive spring loading on the arm. Inspect
the follower arm pin for excess wear and replace if
needed. The takeoff arm attached to the stem clamp
must be firmly secured to the stem clamp and perpen-
dicular to the actuator stem. If this takeoff arm is canted
or misaligned, problems may occur with positioner
calibration and the position reading on the StarPac may
go out of range.
On rotary actuators, make sure the adjustment linkage
locknut is tight and has no excessive play in the ball
joints. The rotary shaft clamp must be tight and should
not freely rotate on the shaft.