Foreword, Welded – Flowserve G4 Marathon Sleeveline Plug Valves User Manual
Page 2
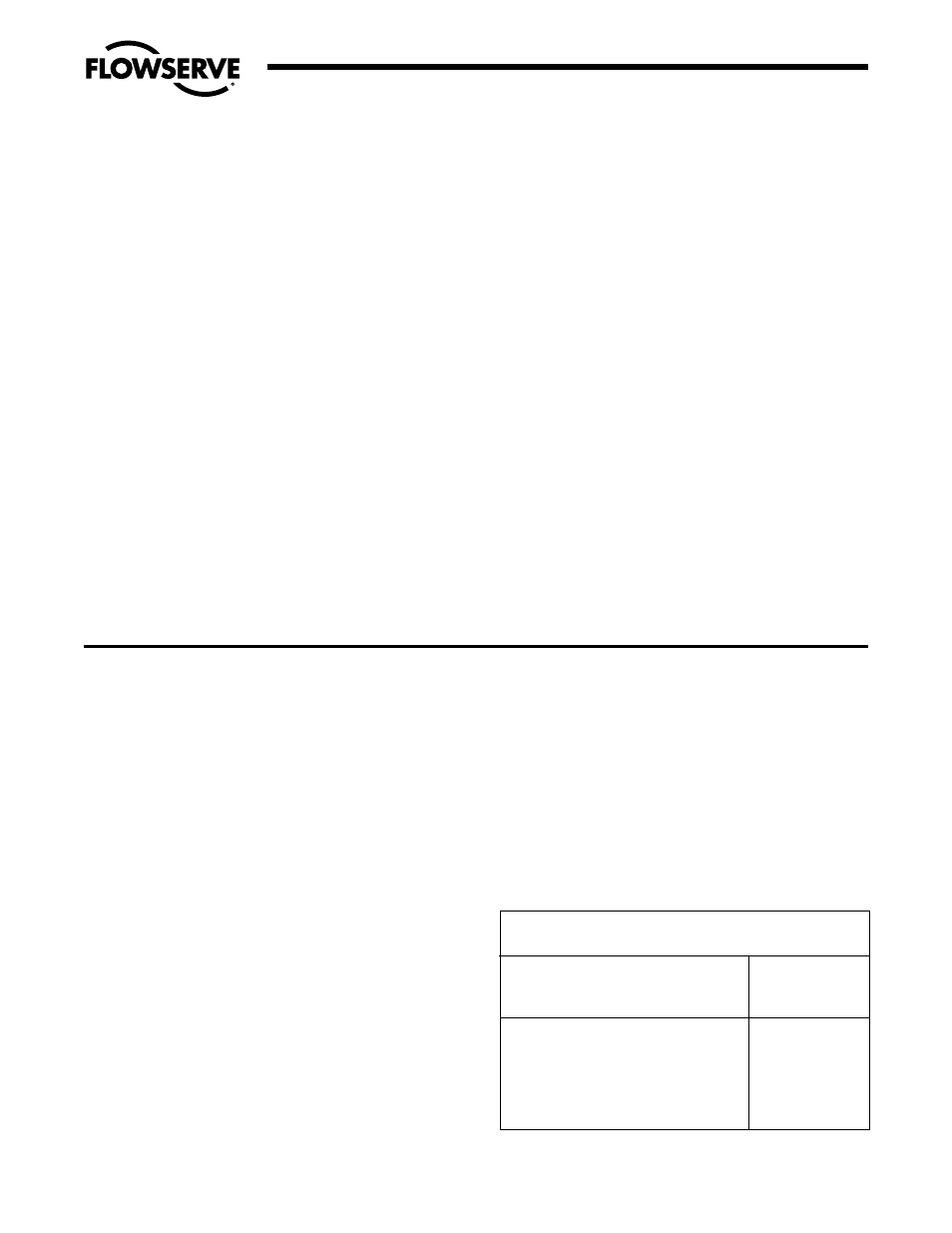
FOREWORD
Flowserve Corporation, Flow Control Division, has established
this Installation, Operating, and Maintenance Manual to facili-
tate field installation, operation and repair of G4 Marathon,
G4Z Marathon and G4R Marathon valves.
It is recommended that questions or concerns involving the
processes described in this manual be directed to the local
Sales Representative of Flowserve Corporation. Only
Flowserve replacement repair parts and assembly tooling
made or designed by Flowserve Corporation should be used.
Part numbers referenced in the following sections are avail-
able from Flowserve Corporation, Flow Control Division.
TABLE OF CONTENTS
SECTION
TITLE
PAGE
FOREWORD
I
INSTALLATION INSTRUCTIONS – FLANGED AND WELDED G4 Marathon, G4Z Marathon, G4R Marathon
2
II
OPERATING/MAINTENANCE – G4 Marathon, G4Z Marathon, G4R Marathon
3
III
VALVE DISASSEMBLY – G4 Marathon, G4Z Marathon, G4R Marathon
4
IV
PRESSURE CONTAINING FASTENERS
5-6
V
A.
VALVE ASSEMBLY –
1
/
2
" &
3
/
4
" G4 Marathon, G4R Marathon
7-8-9
B.
VALVE ASSEMBLY – 1"-8" G4 Marathon, G4R Marathon
10-11-12
VI
ASSEMBLY SPECIFICATIONS – FIRESAFE VALVES G4Z Marathon, G4ZR Marathon
13-14-15
VII
RECOMMENDED SPARE PARTS
16
SECTION I
INSTALLATION INSTRUCTIONS –
FLANGED AND WELDED G4 MARATHON, G4Z MARATHON, G4R MARATHON
FLANGED:
Installation of Flowserve flanged valves is best accomplished by
locating valves in pipeline flanges, assuring all corrosion and
foreign material are removed from pipe flange and then center
gaskets with the valve flanges. Fasteners or taper pins should
be used to align holes and locate gaskets. Fasteners should be
tightened to the corresponding valve and fastener size.
WELDED:
Flowserve Corporation, Flow Control Division recommends
using only qualified welding procedures and personnel for
weld installation of G4 Marathon and G4R Marathon valves.
The following precautions should be observed:
1. The valve should be inspected prior to welding to assure
that no foreign materials obstruct the flow passageway
and that the weld preparations are free of corrosion and
physical damage.
2. The valve should be in the open position while being welded.
Open position is when the flow indicator on the plug stem is
pointing in the direction of the pipeline.
3. Valves of the G4 Marathon and G4R Marathon style contain
various seal materials which have a maximum temperature
limitation. (Refer to Table 1.1 for temperature limitations.)
The valve body sleeve area should not exceed this tempera-
ture during welding including preheats, interpasses, or post
weld heat treatments as applicable. Due to welding variables,
contact the Flowserve Corporation, Cookeville, TN, Valve
Operation for additional information or recommendations.
4. Leak-off or buffering connections should be installed after
the valve has been welded into the pipeline. A suitable thread
sealant is recommended for installing such connections.
TABLE 1.1
TEMPERATURE LIMITATIONS
MAXIMUM
MATERIAL DESCRIPTION
SERVICE
TEMPERATURE
Ultra High Molecular Weight
Polyethylene (UMPE)
200°F (93°C)
Tetrafluoroethylene Polymer (PTFE)
400°F (204°C)
Durlon 2
450°F (232°C)
Duriron Durco 82 (DU-82)
275°F (135°C)
2
Flow Control Division
Section 1.0