Flowserve BUSwitch with Foundation Fieldbus Communications Protocol User Manual
Page 2
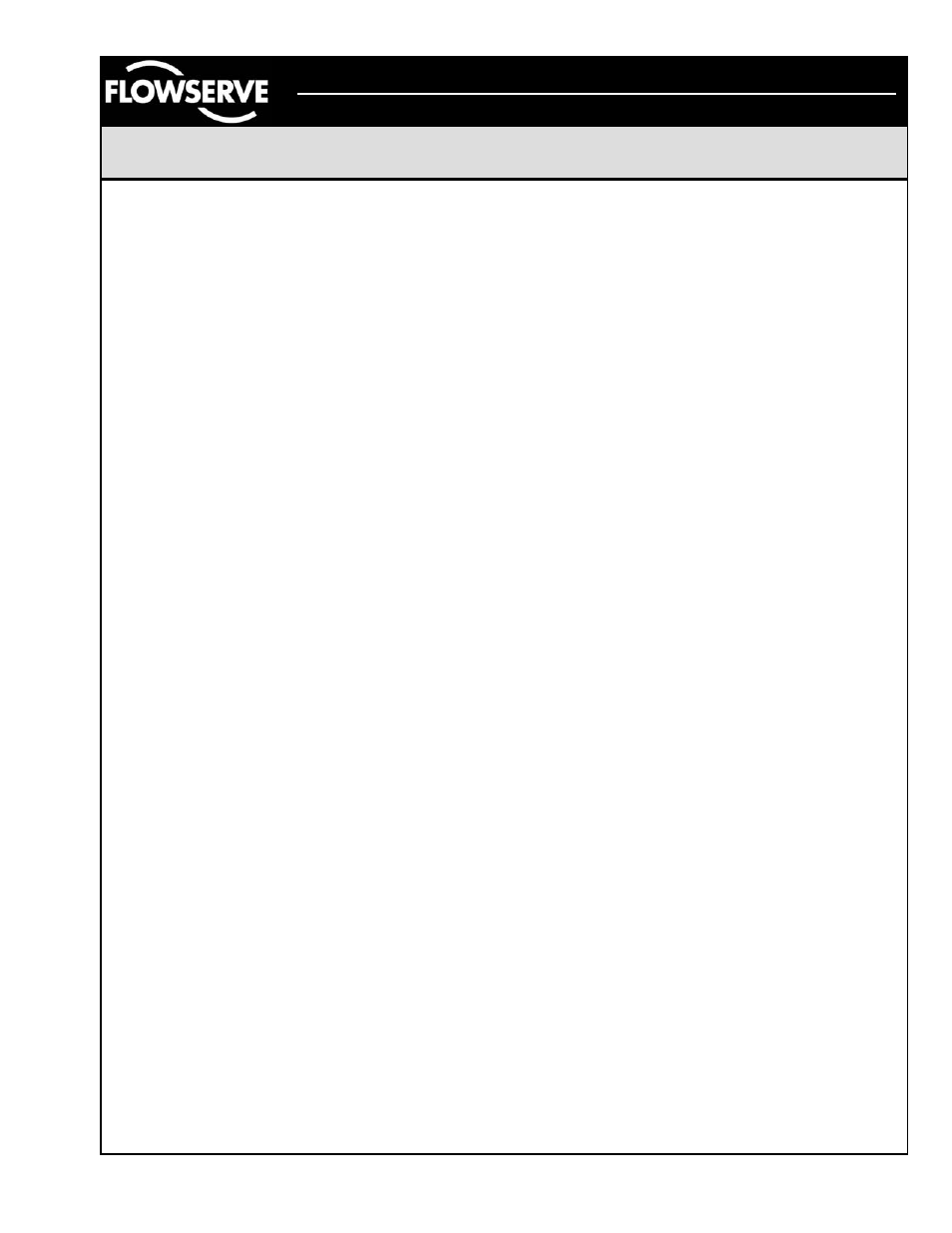
AX
ENIM0048-01 (Firmware Rev. Nov. 11 99) (AUTO-48) 11/01
Page 2 of 16
©2001, Flowserve Corporation,
Springille, UT
Flowserve Corporation
1350 South Mountain Springs Parkway
Phone: 801
489 2233
Flow
Control
Division Springville,
Utah
84663
Facsimile:
801
489
2228
Automation
Business
Unit www.flowserve.com
Email:
Automax Valve Automation Systems
Product Specification
Table of Contents
Introduction . . . . . . . . . . . . . . . . . . . . . . . . .
2
Principles of Operation . . . . . . . . . . . . . . . .
2
Printed Circuit Board Specifications . . . . . .
3
Start-up Guide . . . . . . . . . . . . . . . . . . . . . . .
3
Mechanical Installation . . . . . . . . . . . . . . . .
4
Lubrication . . . . . . . . . . . . . . . . . . . . . . . . . .
4
Electrical Connections . . . . . . . . . . . . . . . . .
5
Adjustment of Switch Cams . . . . . . . . . . . . .
6
BUSwitch™ Embedded Software Specs . . .
6
Resource Block . . . . . . . . . . . . . . . . . . . . .
7
Resource Block Parameter Table . . . . . . . .
7
Transducer Block . . . . . . . . . . . . . . . . . . . .
9
Pneumatic Actuator Operation . . . . . . . . . .
9
Valve Position Monitoring and Reporting . .
9
Auxiliary Dry Contact Input . . . . . . . . . . . . .
10
Odometer . . . . . . . . . . . . . . . . . . . . . . . . . .
10
Transducer Block Parameter Table . . . . . . .
11
DI Function Block Parameter Table . . . . . .
14
DO Function Block Parameter Table . . . . . .
15
Introduction
Flowserve’s BUSwitch™ uses the F
OUNDATION
®
Fieldbus
communication protocol to operate pneumatic valve
actuators and monitor/report their position. BUSwitch™
also provides an odometer to assist in preventative
maintenance. The BUSwitch is registered as a Link
Master, making it a must for redundant control systems
where the BUSwitch maintains control of the segment in
the event the host system is down. The BUSwitch
supports up to 49 links.
Principles of Operation
BUSwitch™ utilizes two discrete output function blocks
(DO-1 and DO-2) to energize piezo or solenoid coils,
which act as pilots to shift a large capacity spool valve.
For spring return and double acting applications with a
desired fail position (open or closed) DO-1 is used to
operate a single pilot. For applications requiring fail in last
position, both DO blocks are used with a “dual coil” pilot
configuration.
In dual coil mode, users may choose to de-energize
piezo/solenoid coils after the valve has reached its desired
position or may configure the elements to remain
energized (factory default) (see “Transducer Block”).
Valve position is sensed with two limit switches.
BUSwitch™ communicates the state of these limits in the
transducer block’s CLOSED_SWITCH and OPEN
_SWITCH parameters and in the OUT_D parameters of
the DI-3 and DI-4 function blocks (linkable),
READBACK_D of DO-1 (Single Readback) or
READBACK_D of DO-1 and DO-2 blocks depending upon
configuration.
The transducer block’s ODOMETER parameter tracks the
number of valve strokes. It may be reset using
RESET_ODOMETER.
The transducer block’s transition alarm alerts the user if
the stroke time exceeds the time in the parameter
TIME_OUT. This alarm is also passed to the OUT_D of
the DI-1 block.
The OPERATION parameter permits the user to select
single coil, dual coil, or Single Readback for limit switch
status. Single Readback provides a digital feedback to the
READBACK_D parameter in the DO-1 block, allowing the
user to assign a single tag per device.
Four discrete input blocks are factory-configured. DI-1 is a
discrete value indicating the stroke exceeded a specific
time. DI-2’s OUT_D parameter provides a link to an
external dry-contact input (terminal P4). This input is
jumper-selectable to normally open or normally closed
(jumper J1/J2). Common uses for this input include valve
packing pressure monitoring or a pressure switch. DI-3 is
a discrete value indicating the closed switch status. DI-4
is a discrete value indicating the open switch status. All
discrete input blocks are linkable for field
interconnectability of function blocks.
A 2-wire cable using the FF H1 (31.25 Kbps) protocol
provides communication and power to the FF
Communication Board. The communications board,
switches, and piezo/coil pilots are all connected to an
interface board. Two versions of this interface card are
available:
•
2-Wire for bus-powered pilot applications. Utilizes
ultra-low power piezo pilot valves.
•
4-Wire for externally-powered pilot applications.
Utilizes a wide range of 24VDC coil pilot valves.
The communications card operates from 9.5 to 32 VDC.
BUSwitches are configured to dra
w 14mA of current.
Current consumption from the fieldbus segment will
remain constant whether a piezo/coil actuator is activated
or not.