Worcester actuation systems – Flowserve DFC17 User Manual
Page 14
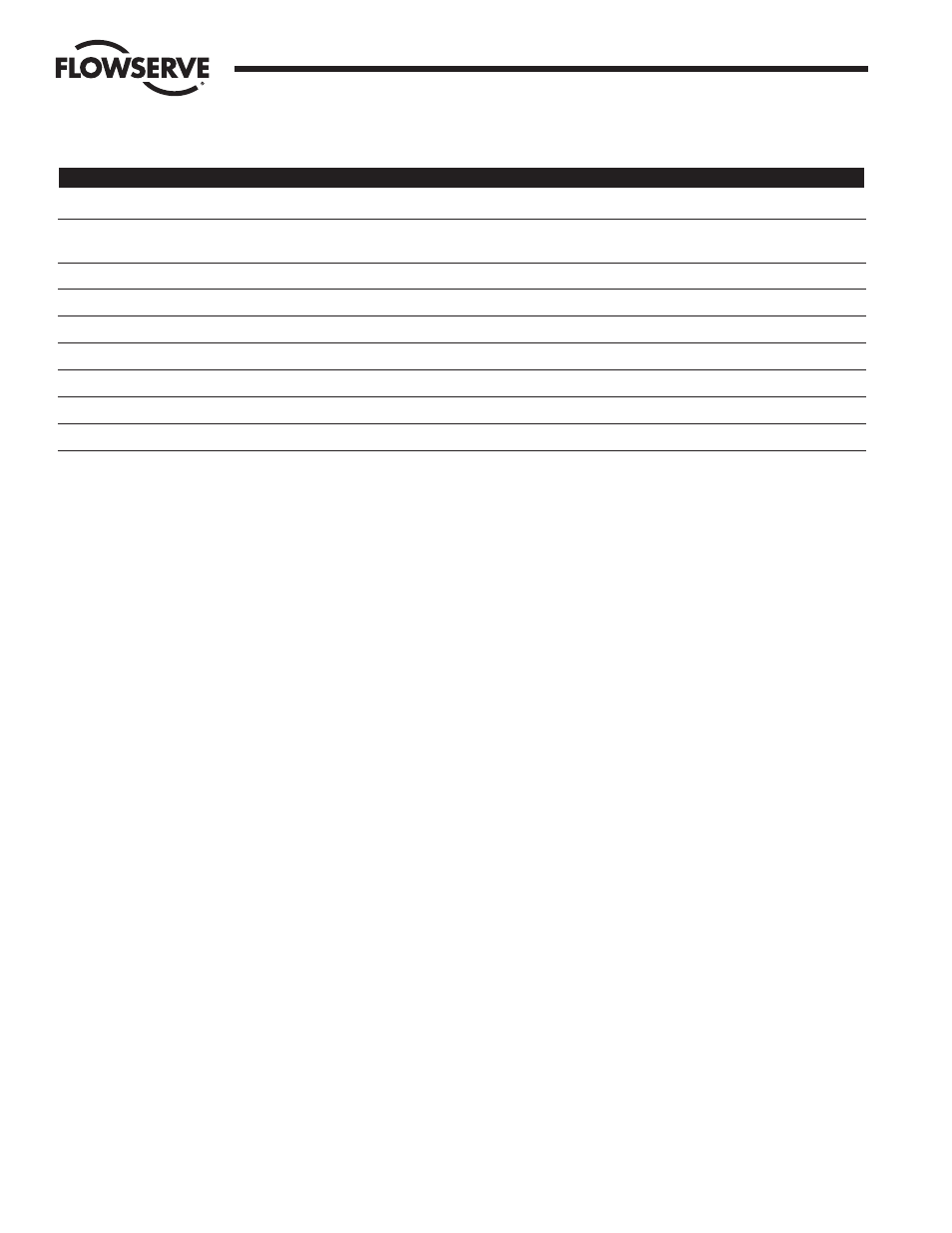
14
DataFlo Digital Electronic Controller DFC17 Installation, Operation and Maintenance Instructions
WCAIM2026
4.2.5 Key Sequences for Calibrating Counter-clockwise Position
Press DN to select the counter-clockwise setpoint
parameter PoCC
Press SEL + UP to begin calibrating the parameter.
1) Use either the UP or DN switches to manually rotate
the actuator to its full counter-clockwise (CCW)
position.
2) With the actuator in the full CCW position, the voltage
reading on the display should be greater than 3.000
volts. If not, recheck PoC. If it is correct and the PoCC
reading is still not correct, contact factory.
Press SEL to accept the value shown and return to
the calibration menu.
4.2.6 Key Sequences for Calibrating Analog Process #1 Lower
Input Signal
This procedure is followed only if an analog process
module is used.
Press DN to select the lower input parameter PrlL
Press SEL + UP to begin calibrating the parameter.
Attach an accurate current source to the process input
and set a current of 4.0 mA. The voltage reading on the
display should be less than 1 volt.
Press SEL to accept the value shown and return to the
calibration menu.
4.2.7 Key Sequences for Calibrating Analog Process #1 Upper
Input Signal
This procedure is followed only if an analog process
module is used.
Press DN to select the upper input parameter PrlU
Press SEL + UP to begin calibrating the parameter.
Attach an accurate current source to the process input
and set a current of 20 mA. The voltage reading on the
display should be greater than 3.000 volts
Press SEL to accept the value shown and return to the
calibration menu.
4.2.8 Key Sequences for Calibrating Single Channel RTD Process
Module
This procedure is followed only if a single channel RTD
process module is used. With this type of process
module, an attached 100 ohm platinum RTD develops a
voltage representing the temperature of the process.
RTDs can cover a very wide temperature range. The RTD
module however allows a narrower temperature range to
be used. This is useful for applications that need higher
resolution and do not need a wide range.
The purpose of this procedure is to specify the
temperature units, temperature range, and to record the
actual voltage values at the lower and upper process
limits. This procedure involves adjusting components on
the RTD module. This procedure is entered by selecting
either the Pr1L or Pr1U parameter for calibration. When
either of those parameters is selected for calibration, the
controller starts the following calibration sequence. At any
time in the menu, the user can press the SEL key to
return to the calibration menu.
Any one step in the calibration procedure can be
performed without performing the others. However, it is
recommended to perform all the calibration steps if any
one item is changed.
Calibrating the RTD module circuitry involves adjusting
the span and zero potentiometers on the module to
achieve a good voltage swing for the temperature range
selected. When adjustments have been properly
completed, the calibration routine will use the calibrated
analog voltages to create a linearization table.
Flow Control Division
Worcester Actuation Systems
Table 4.2.1 Calibration Mode Menu
Display
Description
Acceptable Range
SEtL
Setpoint lower limit signal value.
Less than 1 volt.
SEtU
Setpoint upper limit signal value.
Between 3.800 volts
and 5.000 volts.
PoC
Shaft position feedback value at full clockwise position.
Between .200 volts and .400 volts.
PoCC
Shaft position feedback value at full counter-clockwise position.
Greater than 3.0 volts.
PrlL
Process #1 signal lower limit value.
Unique to process.
PrlU
Process #1 signal upper limit value.
Unique to process.
Pr2L
Process #2 signal lower limit value.
Unique to process.
Pr2U
Process #2 signal upper limit value.
Unique to process.
CYt
Cycle time measurement.
Dependent on actuator.