0 troubleshooting, Worcester actuation systems – Flowserve DFC17 User Manual
Page 24
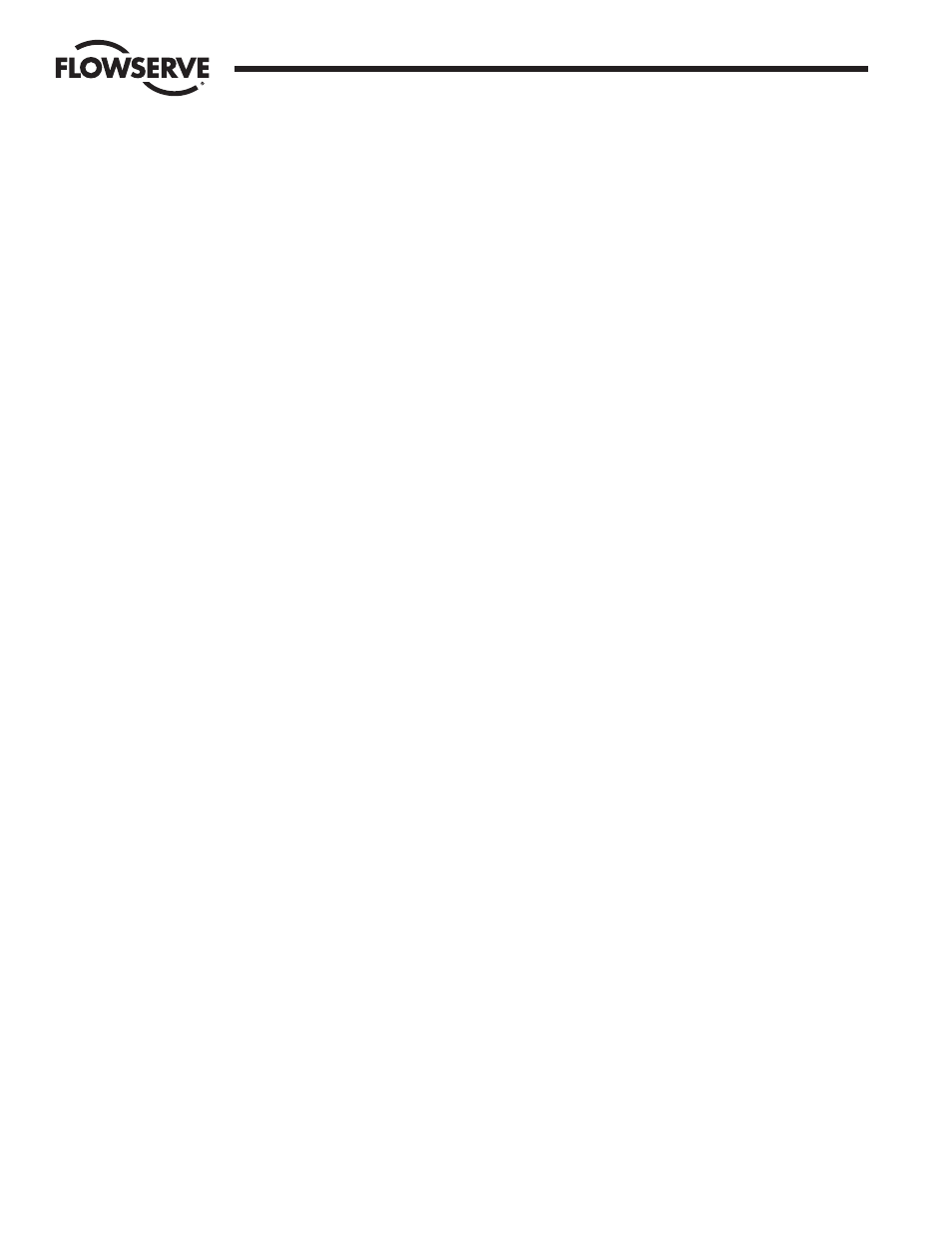
24
DataFlo Digital Electronic Controller DFC17 Installation, Operation and Maintenance Instructions
WCAIM2026
Flow Control Division
Worcester Actuation Systems
6.0 TROUBLESHOOTING
6.1 General
The following paragraphs and charts are a troubleshooting guide
for servicing the Controller, should a malfunction occur. If the
problem cannot be solved, the unit should be returned to the
factory for service.
The first thing to be checked, before proceeding to the
troubleshooting guide, is to determine if the malfunction is in the
Controller, or in the actuator. To do this for AC boards, remove
the red and black Controller leads from terminals 3 and 4 of the
actuator, and the AC line connections from terminals 1 and 2.
Tape these leads. Using a test cable, apply power to actuator
terminals 1 and 3. The actuator should rotate CCW until stopped
by the CCW limit switch. Then apply power to terminals 1 and 4
to check CW actuation and the CW limit switch.
For 240 VAC Digital Controller only, switches do not directly limit
travel. Exercise caution not to override limit switches. Operate
the unit to its limits in each direction, to assure that the basic
actuator is functional.
If the AC actuator does not operate, check wiring from the
terminal strip, through the limit switches to the motor and
capacitor. For 240 VAC actuator with Digital Controller, check
wiring from the terminal strip to the capacitor and to the motor.
Check switch continuity. Check for an open motor winding, and
check for a shorted capacitor.
If the problem in the actuator still cannot be determined, return
the unit for service. If the actuator functions properly, then
proceed to the troubleshooting guide.
For DC boards, remove red and black leads coming from
motor(s) at terminals 3 and 4. Connect these leads to power
supply to check motor(s) operation. If motor(s) run properly, then
proceed to the troubleshooting guide or return unit for service.
To facilitate troubleshooting a Controller, it would be
advantageous on resistive input units to connect a
potentiometer directly to the Process signal input terminals in
place of the standard process input. Use a 150 ohm or 1000
ohm potentiometer depending on which model is used. Figure 6
shows a schematic of a simple test unit that can be connected
to the input terminals to stimulate the process signal for a
milliamp rating.
6.1.1 Cam
Adjustment
The actuator cams should actuate the limit switches 1° to
3° after the actuator stops at either the fully open or fully
closed position.
If the actuator is closed at 0 degrees, the limit switch
must actuate by the time the actuator is at the minus 1 to
3 degree position. Similarly, at the open or 90 degree
position, the limit switch must actuate by the time the
actuator is at the 91 to 93 degree position.
NOTE: See NOTE in paragraph 6.1.3.
6.1.2 Check Fuse F1
Check fuse F1 to see if it is blown. If it is, replace it with
Littlefuse PICO II very fast-acting fuse rated at 62 mA.
(Newark part number 94F2146).
For DC boards, also check fuse F2 to see if it is blown. If
it is, replace it with a 1
1
/
4
", 250 volt, 3 amp fuse, available
through any electrical supplier.
IMPORTANT: To check fuse F1 - remove it from circuit
and test with ohmmeter. Resistance should be about
6 ohms.
NOTE: If fuse F1 is blown, excessive voltage (possibly
120 VAC) was applied to the signal input circuit. If so,
correct this condition before changing fuse. See
paragraph A of Part 1.1.
6.1.3 Check Basic Actuator for Proper Operation
For AC boards, check basic actuator for proper operation
using the correct AC Voltage.
A. Remove red and black leads coming from AC circuit
board at terminals 3 and 4 (if already installed). Tape
stripped ends of these wires.
B. For AC boards, alternately energize, with the
appropriate AC voltage, terminals 1 and 3 and 1 and
4. The actuator should move clockwise when
energizing terminals 1 and 4, stopping only at the
clockwise limit switch. The actuator should move
counter-clockwise when energizing terminals 1 and 3,
stopping only at the counter-clockwise limit switch.
NOTE: For 240 VAC Digital Controller only, limit
switches do not directly control motor. Therefore, the
actuator will not stop when the limit switches trip.
Use care not to drive the actuator past its normal
limits. Run the actuator to its limits in each direction,
to assure proper operation of the actuator.
6.1.4 Check for Noise Problems
If the circuit board’s light emitting diodes (LEDs) blink or
seem to continuously glow, electrical noise is interfering
with the Controller’s Process input signal or the setpoint
input signal. (Always use shielded cable for both the
process signal and the setpoint signal coming to the
Digital Controller board. Ground the shield at only one
end.) Adjust Digital Controller as necessary. See Part 4.2.
6.1.5 Replace Circuit Board
The following information is provided if it becomes
necessary to replace the circuit board.
A. Turn off the power supply and disconnect the circuit
board wires from the terminal strip. Disconnect the
pot wires at TB1 and any wires at TB2.
B. Remove circuit board mounting screws, nylon
washers, circuit board and insulator board with
rubber grommets from the brackets.