Worcester actuation systems – Flowserve DFC17 User Manual
Page 22
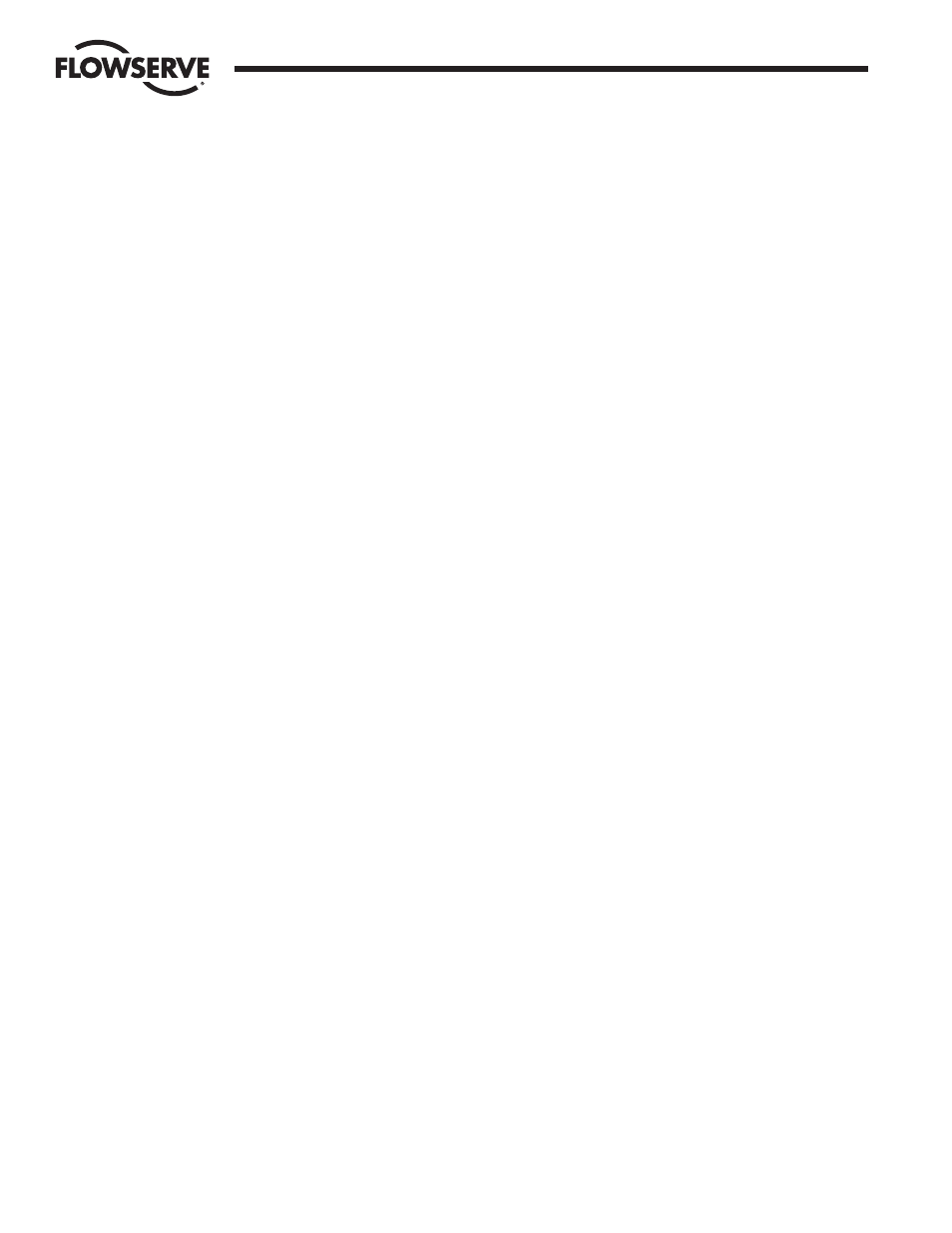
22
DataFlo Digital Electronic Controller DFC17 Installation, Operation and Maintenance Instructions
WCAIM2026
4.8 Controller Setup
4.8.1 General Setup
Read the Safety Considerations section to determine what
steps might be necessary to insure a safe control system.
Determine the Engineering Units for the setpoint and
process inputs. Program the lower and upper process
limits and lower and upper setpoint limits using
Program Mode.
Program alarm limits if they are used.
4.8.2 Tuning the Controller Automatically (open-loop tuning)
Be sure the controller is properly set up as described
above. Be sure to know the safe operating range of the
valve.
Enter the Manual Position Mode and set a starting valve
position.
Enter the Auto-Tune Mode and establish the offset
percentage for valve movement.
Run the Auto-Tune procedure. If an alarm occurs, note
the alarm condition, exit the Auto-Tune Mode and take
appropriate action to insure a safe condition. If Auto-Tune
completes, view the computed control terms and decide
whether to install them or reject them.
If there are no alarm conditions, return to the Run Mode
and observe controller operation. If more tuning is
desired, consider the closed-loop tuning described below.
Alternately, individual control parameters can be modified
in the Program Mode.
4.8.3 Tuning the Controller Manually
Manual tuning involves making changes to the setpoint
and observing the behavior of the process. Observations
should be recorded and some type of recording device
(e.g., a strip chart recorder) is highly recommended.
Be sure the controller is operating in a safe and relatively
stable manner at or near a typical setpoint.
Enter the Manual Setpoint Mode and make a step change
to the setpoint value. The suggested amount of setpoint
step change is in the range of 5% to 10%, but should
not cause an unsafe condition to occur. Return to the
Run Mode.
Measure the lag time. This is the time it takes after the step
is made before any change in the process is observable.
Measure the response of the process. Did it overshoot? If
so, by how much? Does it tend to oscillate after a step
change? If so, what is the frequency of oscillation? How
long does it take the process to reach the new setpoint?
Analyze the results. Based on the requirements for control,
determine what control parameters might need changing.
4.8.4 Some Guidelines for Control Parameters
The maximum gain possible occurs where the process
begins to oscillate about the setpoint.
The recommended proportional gain (the P-term) for
stability is one-half or even one-third the maximum gain
determined. So, for example, if oscillation begins at a
P-term setting of 6000, good stability will be achieved by
reducing the setting to 2000 or 3000.
Leave the Integral (I-term) value at 60 unless very high
performance operation is required. Refer to the Appendix
on floppy disk for fine tuning guidelines.
Leave the Derivative (D-term) value at 10 unless faster
response time for high performance systems with short
lag times and high proportional gain is required.
Set the Cycle Time to a value greater than or equal to the
measured process system lag time. If the cycle time is set
to less than the lag time, the valve position might change
before the effect of a previous change is detected.
Flow Control Division
Worcester Actuation Systems