0 limitations – Mathey Dearman 4SA Saddle Machine User Manual
Page 18
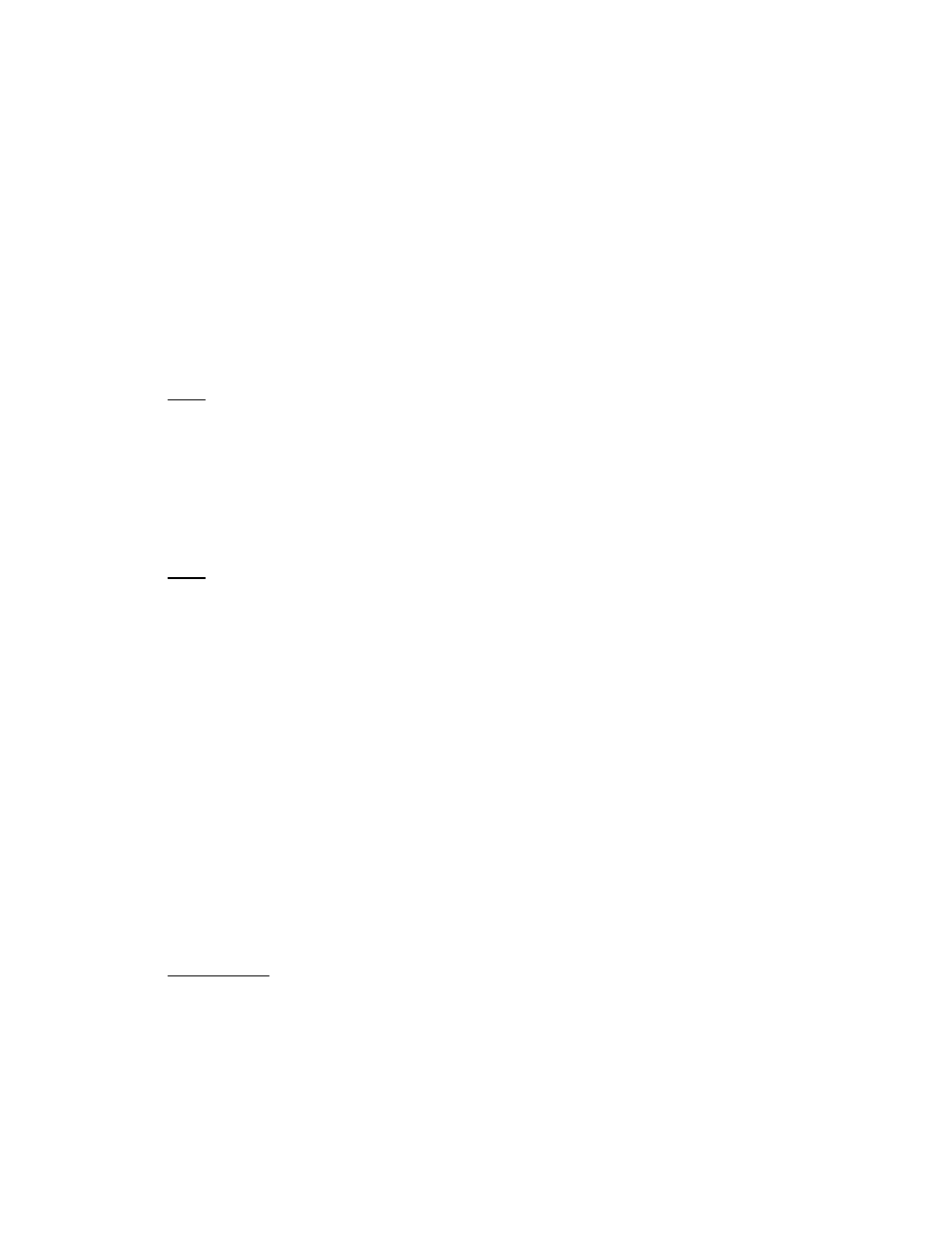
18
7.2.25 When placing the Left Single Bearing Bracket Assembly (Figure 4 item 4) in position, rotate the Pinion
Gear (Figure 5 item 3) so the teeth mesh in the teeth of Ring Gear (Figure 4 item 3).
7.2.26 Install the 3/8-16 x 3/4” Hex Head Cap Screws (Figure 4 item 11) and 3/8” Washer (Figure 4 item
14) into the Left Single Bearing Bracket (Figure 4 item 4) and screw into the Saddle (Figure 4 item 1).
7.2.27 There should be a .005” to .007” gap between the Pinion Gear (Figure 5 item 3) and the teeth of Ring
Gear (Figure 4 item 3). Make sure the Pinion Gears (Figure 5 item 3) of the Single Bearing Brackets
(Figure 4 items 4 & 5) are evenly spaced in the teeth of the Ring Gear (Figure 4 item 3).
7.2.28 Snug the 3/8-16 x 3/4” Hex Head Cap Screws (Figure 4 item 10) with a 9/16” wrench.
7.2.29 Tighten the Socket Set Screw (Figure 5 item 6) in the Sprocket (Figure 5 item 2) of the left Single
Bearing Bracket (Figure 4 item 4) with a 5/32” allen wrench.
7.2.30 Rotate the Ring Gear (Figure 4 item 3) clockwise (as viewed from the front of the machine) check the
entry of the Pinion Gear (Figure 5 item3) of the Right and Left Single Bearing Bracket Assemblies
(Figure 4 items 4 & 5) into the Ring Gear (Figure 4 item 3).
7.2.31 Adjust the Pinion Gear (Figure 6 item 3) of the Left Single Bearing Brackets (Figure 4 item 4) as
needed so that it enters the Ring Gear (Figure 4 item 3) without hesitation.
Note: When the Pinion Gears (Figure 5 item 3) of the Left and Right Single Bearing Bracket (Figure 4
item 4 & 5) enters the Ring Gear (Figure 4 item 3) it should not suddenly pull the Ring Gear. As the
Pinion Gear (Figure 5 item 3) of the Left and Right Single Bearing Bracket (Figure 4 item 4 & 5)
leaves the Ring Gear (Figure 4 item 3) it should not suddenly push the Ring Gear.
7.2.32 Tighten the Hex Head Cap Screws (Figure 4 item 11) on both sides of the Left Single Bearing Bracket
Assembly(Figure 4 item 4) using a 9/16” wrench.
7.2.33 Rotate the Ring Gear (Figure 4 item 3) one (1) full revolution in the clockwise and counterclockwise
direction checking the entry of the Ring Gear (Figure 4 item 3) into the Pinion Gears (Figure 5 item 3)
of the Left and Right Single Bearing Bracket (Figure 4 item 4 & 5).
Note: The entry of the Pinion Gears into the Ring Gear should be smooth and without hesitation.
7.2.34 Reattach both Tie Rod Handles (Figure 4 item 7) to the Single and Double Bearing Bracket
Assemblies (Figure 4 items 4, 5 & 6) with the Hex Head Cap Screws (Figure 4 item 10 ) and Hex Nuts
Figure 4 item 13) and tighten with a 1/2" wrench.
7.2.35 Rotate the Ring Gear (Figure 4 item 3) one (1) full revolution in the clockwise and counterclockwise
direction checking the entry of the Ring Gear (Figure 4 item 3) into the Pinion (Figure 5 item 3) of the
Left & Right Single Bearing Bracket Assembly (Figure 4 item 4 & 5) to insure the entry of the Pinion
Gears into the Ring Gear is smooth and without hesitation.
7.2.36 Drill through the Sprocket (Figure 5 item 2) and Axle (Figure 5 item 4) of the Left Single Bearing Bracket
(Figure 4 Item 4) with a 3/16” drill.
7.2.37 Install 3/16”x 1-1/4 long spring pine into the Sprocket (Figure 5 item 2).
7.2.38 The machine is now ready for the cutting operation.
7.3
Disassembly and Repair of the Single and Double Bearing Bracket Assemblies.
Contact Mathey Dearman for instructions, if disassembly and repair of the Single and Double Bearing
Bracket Assemblies is required
7.4
Storage
If the machine will not be used for a period of the time, the machine should be cleaned and regreased
with Lubriplate 130-AA. The machine should be stored in a clean and dry place protected from damage.
8.0 Limitations
Mathey Dearman is not and will not be responsible for
Improper use of the Saddle Machine.
Use of the Saddle Machine in violation of any national and/or international electrical and safety
regulations in force.
Connection of the Motorized Saddle Machine to an improper or wrong power source.
Faulty maintenance.