Installation in a cored fiberglass hull, Operation, maintenance, repair, & parts, Using the blanking plug – Airmar B122—Long-Stem User Manual
Page 7: Servicing the insert & blanking plug
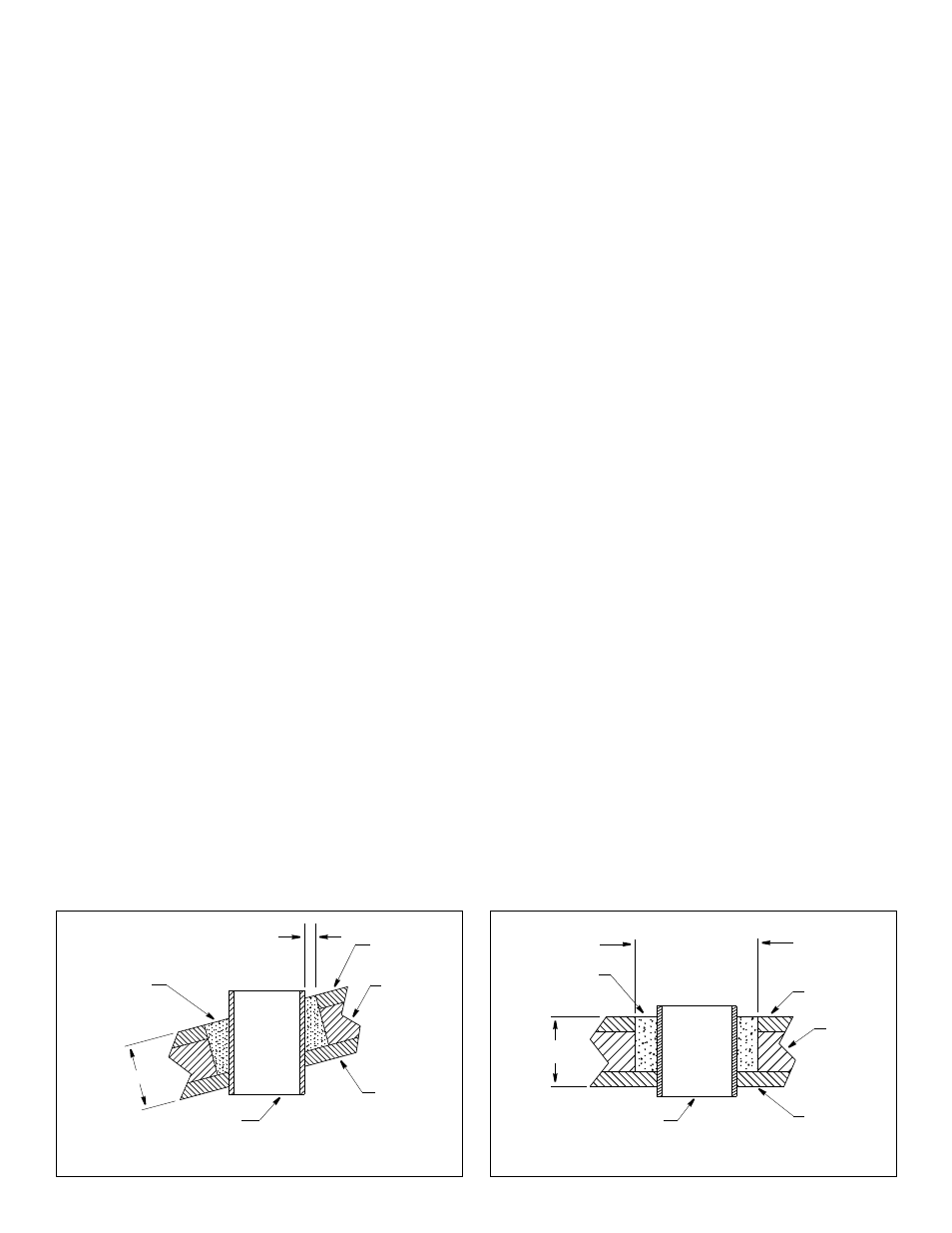
7
Installation in a Cored Fiberglass Hull
The core (wood or foam) must be cut and sealed carefully. The
core must be protected from water seepage, and the hull must be
reinforced to prevent it from crushing under the hull nut allowing
the housing to become loose.
CAUTION: Completely seal the hull to prevent water seepage into
the core.
1. Drill a 3mm or 1/8" pilot hole from inside the hull. If there is a rib,
strut, or other hull irregularity near the selected mounting
location, drill from the outside. If the hole is drilled in the wrong
location, drill a second hole in a better location. Apply masking
tape to the outside of the hull over the incorrect hole and fill it
with epoxy.
Fairing—Drill perpendicular to the waterline (see Figure 13).
No fairing—Drill perpendicular to the hull (see Figure 14).
2. Using the 51mm or 2" hole saw, cut a hole from outside the hull
through the outer skin only. Be sure to hold the drill plumb, so
the hole will be perpendicular to the water surface.
NOTE: The optimal interior hole diameter is affected by the
hull’s thickness and deadrise angle. It must be large enough in
diameter to allow the core to be completely sealed.
3. Using a minimum 60mm or 2-3/8" hole saw, cut through the inner
skin and most of the core from inside the hull keeping the drill
perpendicular to the hull. The core material can be very soft.
Apply only light pressure to the hole saw after cutting through the
inner skin to avoid accidentally cutting the outer skin.
4. Remove the plug of core material, so the inside of the outer skin
and the inner core of the hull is fully exposed. Sand and clean
the inner skin, core, and the outer skin around the hole.
5. Coat a hollow or solid cylinder of the correct diameter with wax
and tape it in place. Fill the gap between the cylinder and hull
with casting epoxy. After the epoxy has set, remove the cylinder.
6. Sand and clean the around the hole, inside and outside, to ensure
that the marine sealant will adhere properly to the hull. If there is
any petroleum residue inside the hull, remove it with either mild
household detergent or a weak solvent (alcohol) before sanding.
7. If this is an installation with a fairing, follow the same procedure
to prepare the hull for the anti-rotation bolt ("Installation in a
Cored Fiberglass Hull", steps 2 through 6). Use a 11mm or 3/8"
drill bit to cut the outer skin and a min. (19mm or 3/4") drill bit for
the hull’s inner skin.
8. Proceed with the installation instructions.
Operation, Maintenance, Repair, & Parts
Using the Blanking Plug
To protect the insert, use the blanking plug:
- When the boat will be kept in salt water for more than a week.
- When the boat will be removed from the water.
- When aquatic growth buildup is suspected due to inaccurate
readings from the instrument.
1. The O-rings must be intact and well lubricated to make a
watertight seal. On the blanking plug, inspect the O-rings
(replace if necessary) and lubricate them with the silicone
lubricant supplied or petroleum jelly (Vaseline
®
) (see Figure 9).
2. Remove the insert from the housing by removing the safety wire
and unscrewing the cap nut (see Figure 12).
3. With the blanking plug ready in one hand, pull the insert most of
the way out. Remove the insert and rapidly replace it with the
blanking plug. Seat it into place with a pushing twisting motion
until the key fits into the notch in the housing. Screw the cap nut
in place and hand tighten only. Do not over tighten.
No valve—With practice, only about 250ml (10oz.) of water will
enter the boat.
4. Reattach the safety wire to prevent the insert from backing out
in the unlikely event that the cap nut fails or is screwed on
incorrectly.
Servicing the Insert & Blanking Plug
B122, Blanking Plug—The O-rings must be intact and well
lubricated to make a watertight seal. Inspect the spare O-rings
and lubricate them with silicone lubricant or petroleum jelly
(Vaseline
®
) (see Figure 9). Install the O-rings.
DST800L, ST700
—
The water lubricated paddlewheel bearings
have a life of up to 5 years on low-speed boats [less than 10kn
(11MPH)] and 1 year on high-speed vessels. Paddlewheels can
fracture and shafts can bend due to impact with water borne
objects and mishandling in boat yards. O-rings must be free of
abrasions and cuts to ensure a watertight seal.
1. To remove the old paddlewheel shaft, grasp the end with small
diagonal wire cutters and pull (see Figure 10 or 11).
2. Place the new paddlewheel in the cavity with the flat side of the
blade facing the same direction as the arrow on the top of the
insert.
3. Tap the new shaft into place until the end is flush with the
outside wall of the insert.
4. The O-rings must be intact and well lubricated to make a watertight
seal. Inspect the spare O-rings and lubricate them with silicone
lubricant or petroleum jelly (Vaseline
®
). Install the O-rings.
hull’s outer skin to
hull
outer
solid or hollow
cylinder
pour in
casting
epoxy
core
inner
Figure 13. Preparing a cored fiberglass hull with fairing
Dimension equal to
the thickness of the
ensure adequate
clearance
Copyright © 2006 Airmar Technology Corp.
skin
skin
Figure 14. Preparing a cored fiberglass hull: no fairing
inner skin
core
outer skin
solid or hollow cylinder
pour in
casting
epoxy
9-12 mm
(3/8-1/2")
larger than the
hole through the
hull’s outer skin
hull thickness
Copyright © 2005 Airmar Technology Corp.