HEIDENHAIN CNC Pilot 4290 Pilot User Manual
Page 92
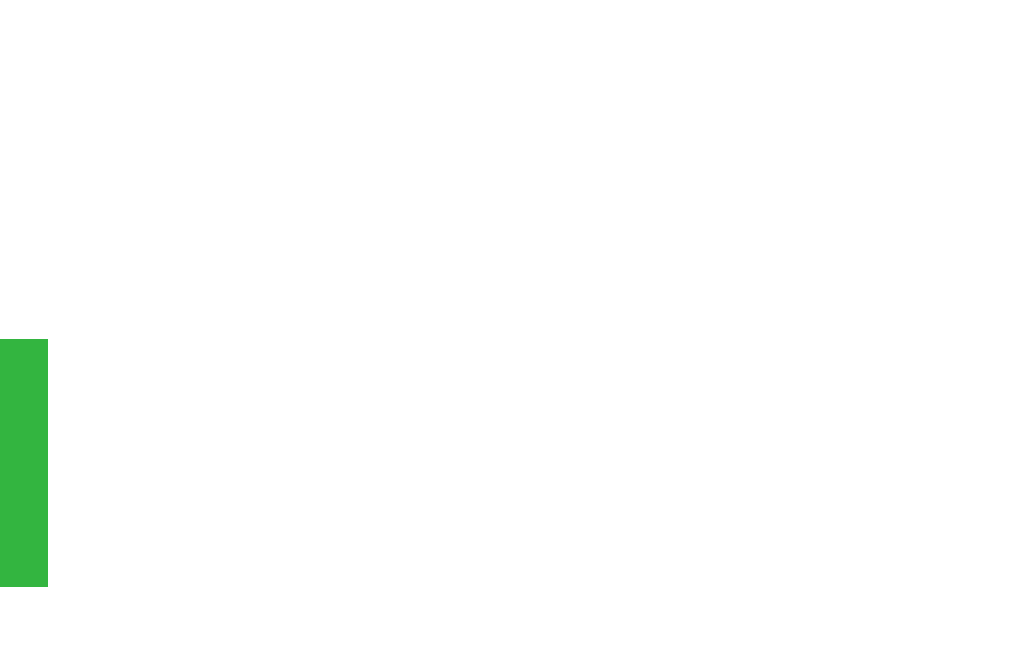
92
C-angle offset G905
G905 measures the angular offset which occurs
during workpiece transfer with a ”rotating spindle”.
The programmed ”angle C” is added to the
measured offset and becomes effective as the
datum shift value for the C axis.
Parameters
Q:
Number of the C axis
C:
Angle of additional datum shift for displaced
infeed – Range: –360°
C 360°; default: 0°
Spindle synchronization G720
G720 controls the workpiece transfer from the
master to the slave spindle and synchronizes
functions such as polygonal turning jobs.
Where: Q * master speed = F * slave speed
Parameters
S:
Number of the master spindle [1..4]
H:
Number of the slave spindle [1..4] – no input or
H=0: Switches off the spindle synchronization
C:
Offset angle [°] – default: 0°
Q:
Master speed factor – default: 1;
Range: –100
Q 100
F:
Slave speed factor – default: Q take effect;
Range: –100
F 100
Regeneration of the contour G703
If changeable variables are used during run-time conditions ”{V...},” CNC
PILOT switches off the contour regeneration function within an IF pro-
gram branch and during a WHILE loop. It is switched on again after
ENDIF/ENDWHILE.
With G703 you can switch on the contour regeneration function for
THEN or ELSE branches.
Parameters
Q:
Contour regeneration On/Off
nÿ
Q=0: Off
nÿ
Q=1: On
Storing/loading contour follow-up G702
G702 Q0 stores the current contour without influencing the contour
follow-up function.
G702 Q1 loads the stored contour; follow-up continues with the new
contour.
Parameters
Q:
Store/load current contour
■
Q=0: store
■
Q=1: load
Other G F
unctions