Startup procedure – Yaskawa G5 PID for Trim Control User Manual
Page 9
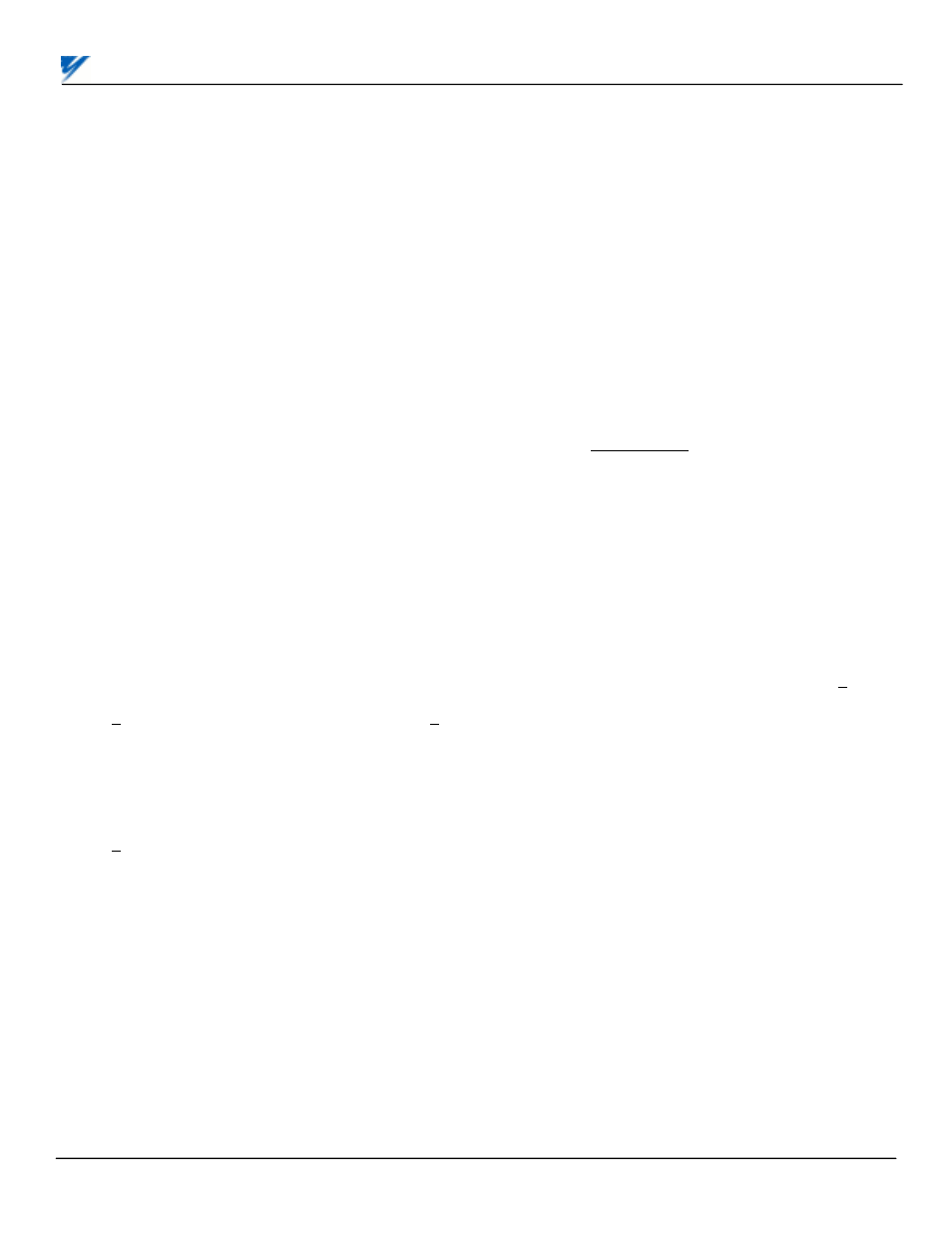
Date: 07/01/04, Rev: 04-07
Page 9 of 12
TM.G5SW.012
Startup Procedure
(typical installation - PID + Line Speed Reference):
1. Follow the appropriate startup procedure in Section 2.2 of the GPD515/G5 Technical Manual TM4515 (2.2a for Open
Loop Vector, 2.2b for Flux Vector, 2.2c for V/f, or 2.2d for V/f with PG Feedback).
2. Calibrate the line speed signal (Using terminal 13 as a 0-10V input).
2.1. Determine the required drive output frequency for maximum line speed.
Frequency = Motor RPM* Motor Poles / 120
NOTE: if this option is being applied as a winder with dancer control, use the motor speed when the
winder is at its smallest diameter (core).
2.2. Determine the maximum amount of positive trim required as a percentage of line speed.
2.3. Set E1-04 (maximum output frequency) to the value determined by the following formula:
E1-04 = Frequency
(@ max line speed)
+ Frequency
(@ max line speed)
* Max. Trim (%)
100
NOTE: If the value of E1-04 is less than 60Hz, use 60 instead of the calculated value.
2.4. Determine what the line speed signal voltage will be when the line is running at the maximum speed.
2.5. Input the voltage determined in step 2d into terminal 13 and adjust parameter H3-02 (terminal 13 gain) until
the line speed is correct (while running the drive). NOTE: in order for the drive to respond to the line speed, the
REF light on the digital operator needs to be illuminated. The LOCAL/REMOTE switch will turn this light on and
off.
2.6. Stop the drive.
3. Program the multi-function analog input 1 (terminal 16) to be PID feedback. The feedback signal can be either +10V or
0-10V:
+10V: set H3-04=1 and set H3-05=b (NOTE: +15VDC power supply is available on terminals 15 & 33)
0-10V:
set
H3-04=0 and set H3-05=b (NOTE: +15VDC power supply is available on terminal 15)
4. Program the drive to accept a PID setpoint. The setpoint for the PID loop can come from one of two places, either a
digitally entered value (b5-07) or an analog value. If a digital value is desired, set the appropriate voltage value into b5-
07. If an analog value is desired, program multi-function analog input 2 (terminal 14) to be a PID setpoint:
+10V: clip jumper J1 (see Section 5.36D), set H3-08=1 and set H3-09=20
0-10V: clip jumper J1 (see Section 5.36D), set H3-08=0 and set H3-09=20
4-20mA: set H3-08=2 and set H3-09=20
5. Determine and set PID output polarity.
5.1. Program b5-09 = 0 if an increase in feedback voltage level results in a decrease of motor speed.
5.2. Program b5-09 = 1 if an increase in feedback voltage level results in an increase of motor speed.
6. Set the appropriate PID mode. Program b5-01 = 2. When this is programmed, the drive will output a frequency
proportional to the algebraic sum of the line speed signal and the PID algorithm output.