JBL Synthesis Everest DD67000 User Manual
Page 9
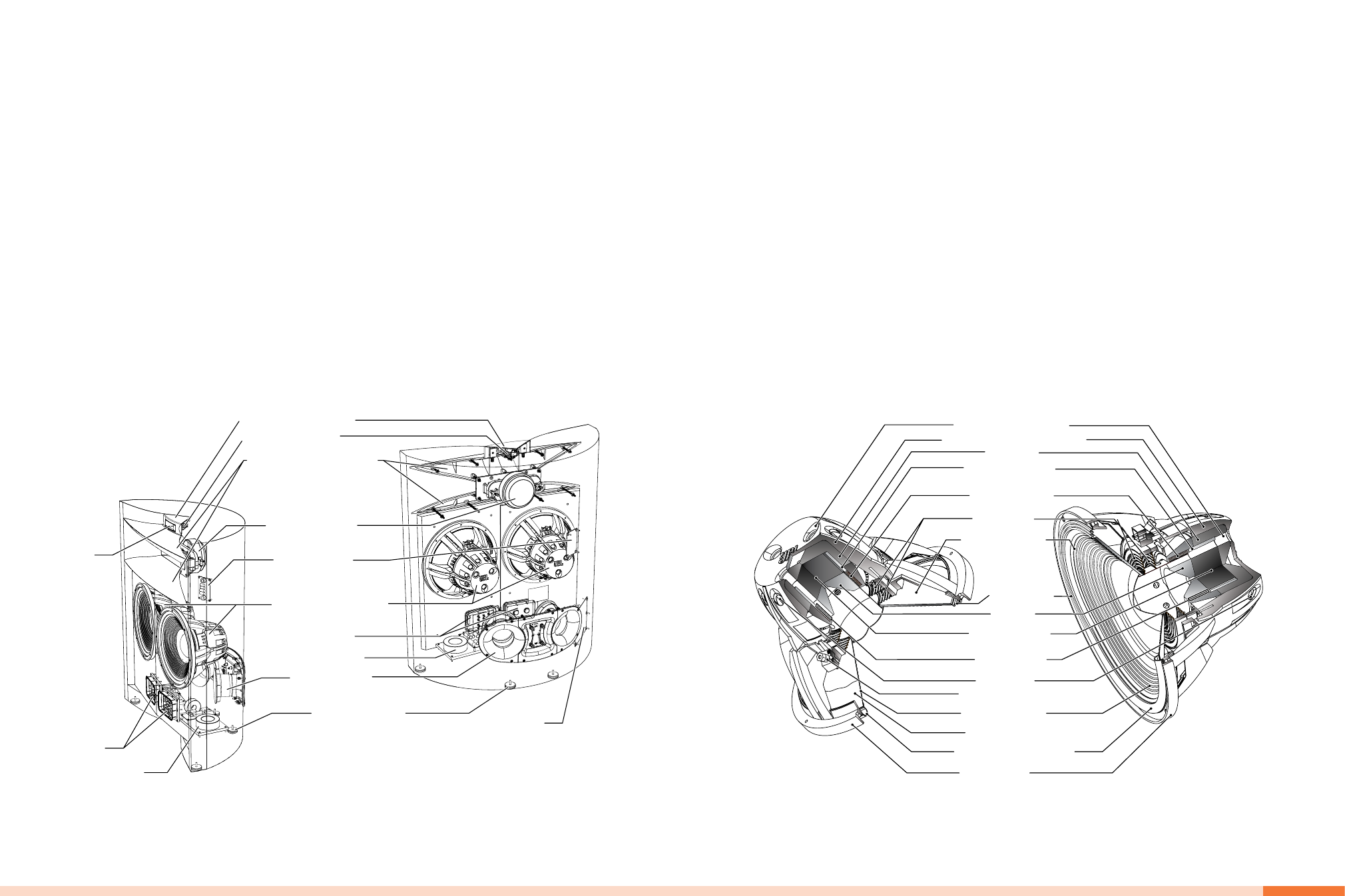
17
16
The transducers, horns and crossover networks are housed
in a visually stunning enclosure that is reminiscent of both the
Hartsfield and Paragon systems. The specially curved baffle
provides the sidewalls for the main high-frequency horn. The top
and bottom horn flares are accomplished by the attachment of
precision-molded SonoGlass
®
horn “lips” to the enclosure’s upper
surface. The UHF driver is mounted to a SonoGlass horn which is
itself mounted to a die-cast aluminum housing.
The entire Everest DD65000 and DD67000 enclosure is
constructed of MDF. The curved panels are formed out of two
thicknesses of MDF with an inner, outer and middle skin. The
MDF is internally grooved, allowing the panels to curve to the
desired dimensions. The voids in the material are filled with a
foam damping compound. The panels are held in place using
a complex internal bracing scheme and external fixturing during
the curing process. The woofer baffle module is a six-sided 3/4
inch (19mm) thick shell, constituting an extremely rigid and secure
structure. The DD65000 has a 1 inch (25mm) thick veneer-
covered outer baffle, giving the total combined woofer baffle a
thickness of 1-3/4 inch (45mm). The DD67000 has an inner 3/4
inch (19mm) baffle constructed of Finland birch plywood and an
outer 1-inch thick baffle that is covered in carbon fiber woven
cloth. The outer baffles of both models are removable (bolted from
the inside of the enclosure) to enable repair or replacement of the
covering surface, should that ever be necessary.
The system is ported on the rear with a tuning frequency of
32Hz for the DD65000 and 31Hz for the DD67000. Two large
4-inch (100mm)-diameter flared ports are combined with the
input connections on a massive three-piece die-cast aluminum
structure. The entire enclosure rests on four stainless-steel foot
assemblies. Stainless-steel coasters are included to protect
wood and tile floors from damage from the spiked feet. The grille
assembly is constructed of MDF and uses a thick, perforated
metal sheet to provide the curved shape. The grille securely
attaches to the enclosure with metal pins and rubber cups.
The low-frequency and high-frequency transducers for the Project
Everest systems are designed to be absolute minimum-distortion
drive units. Although they are capable of tremendous acoustic
output, they are designed to be nearly linear in every way, up to
a reasonably high drive level. This enables the system to sound
the same regardless of playback level. In addition, a great deal of
attention was paid to minimizing distortions and non-linear effects
occurring around signal zero-crossings. The result of this is that
Project Everest systems are able to play at very low levels and still
present realistic response and detail to a degree unattained by
other loudspeaker systems.
Die-cast aluminum housing
045-series 1" (25mm)
uhf compression Driver
sonoglass high-frequency horn
476-series 4" (100mm)
hf compression Driver
sonoglass
uhf horn
adjustment
Panels
crossover network
1501aL-series 15" (380mm)
Lf Driver
adjustment Panels
crossover network
Die-cast aluminum
input Plate/Port assembly
spiked foot assembly
crossover network
crossover
network
Project Everest DD65000/DD67000 System Major Components
Project everest transducers
The 1501AL FAmiLy oF Low-Frequency
TrAnsducers
The 1501AL-1 (DD65000) and 1501AL-2 (DD67000) low-
frequency drivers are very similar to the 1501AL used in the
DD66000, and 1500AL and 1500AL-1 used in the K2 S9800 and
K2 S9900 systems. They all share a common motor assembly
and they all use a long 4-inch (100mm) diameter voice coil with
edge-wound aluminum wire. The 1501 family voice coil is wound
double impedance so that the pair of woofers in a Project Everest
system still allows an 8-ohm system impedance. Their voice coils
are completely immersed in an underhung radial magnetic field
generated by an Alnico 5DG magnet. This underhung design is
a significant feature because even at high output levels, the coil
will always see a constant drive force and will be more thermally
coupled to the motor than is possible with conventional designs.
Alnico was chosen for the magnet material because of its
stable operating point. This material is insensitive to temperature
changes and back EMF from the voice coil. JBL has overcome
Alnico’s tendency to demagnetize with high drive by utilizing
a massive shorting ring at the base of the motor assembly. In
addition to this, the top plate is constructed of alternating copper-
steel laminations. The presence of the copper rings linearizes
the magnetic properties of the gap to all but eliminate both eddy
current distortion and local flux modulation.
A thick-wall, cast-aluminum frame is used to rigidly support the
motor structure. This fully vented frame and motor design also
serves to minimize the back pressure under the dome and spider,
helping to reduce harmonic distortion to even lower levels. JBL’s
Vented Gap Cooling™ (VGC) is incorporated within the motor
structure, and lowers the operating temperature of the coil during
moments of high power operation.
back Plate
vented gap cooling
™
vents
Die-cast aluminum motor housing
conductive aluminum
shorting ring
alternating
copper/steel ring
top Plate
Dual inverted
nomex
®
spiders
Pure Pulp sandwich
cone with foam injection
core (1501aL-2)
Pleated cloth
accordion surround
(1501aL-2)
Polepiece
alnico 5Dg magnet
5-Way binding Post connectors
Layered Paper-Pulp
matrix cone (1501aL-1)
aquaplas Damping material
(1501aL-1)
foamed rubber suspension
(1501aL-1)
Die-cast
aluminum frame
cooling vents
4" edge-Wound
aluminum voice coil
1501AL-Series Woofer Section View