Valve maintenance, Valve seats, Valve disassembly/reassembly – Jordan Valve Mark 70 Series – Sliding Gate Control Valve User Manual
Page 2
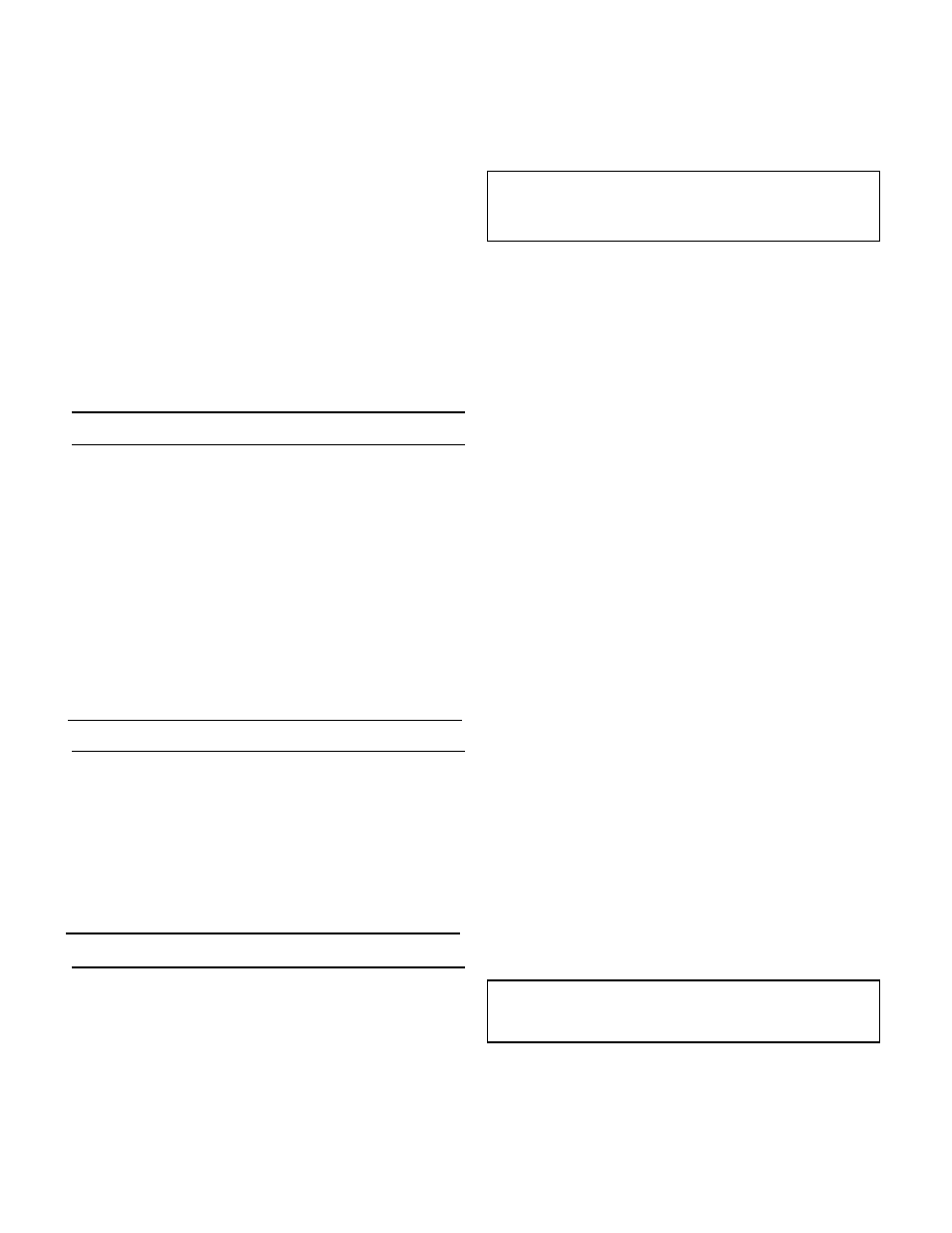
The control valve has been pre-set by Jordan Valve.
2.
However, finer adjustments may be required to
compensate for pressure drop conditions of the ap-
plication.
With the inlet, outlet, and bypass shutoff valves
3.
closed, and no pressure in the downstream line, fully
open the outlet shut off valve. Increase flow gradu-
ally by slowly opening the inlet shutoff valve. Do
not fully open the inlet valve until you are sure that
the controller and control valve have control of the
system. Usually, the handwheel on the inlet valve will
turn freely when this point is reached.
To shut off the line fluid, close the inlet shut-off valve
4.
first, then the outlet shut-off valves.
Body and cap bolts should be retightened per
5.
torque procedures after valve reaches operating
temperature.
Valve Maintenance
Caution: Make certain that there is no pressure in the
valve before loosening any fittings or joints. The fol-
lowing steps are recommended.
Close inlet shutoff valve.
1.
Allow pressure to bleed off through downstream
2.
piping. Do not attempt to reverse the valve by bleed-
ing pressure from the upstream side of the valve.
When the pressure gauges indicate that all pressure
3.
has been removed from the system, close the outlet
shutoff valve, and the valve may be serviced.
Note: refer to the drawing at the end of this docu-
ment for description and proper orientation of parts.
Valve Seats
Follow instructions under Maintenance section to
1.
remove valve from line.
Disassemble the valve only as far as necessary to do
2.
the required work. See Valve Disassembly section.
When replacing seats it is recommended by Jordan
3.
Valve that the packing be replaced if the valve is
older than one year. Follow the instructions under
Packing.
Valve Disassembly/Reassembly
1/2” to 1-1/4” Sizes
To remove the control valve from the line, follow the
1.
instructions under MAINTENANCE.
Secure the body hex in the vise. Remove the cap
2.
screws (3) and lift the cap (2) straight up.
Next, remove the plate (5) and place it on the bench
3.
with the lapped surface up. You will notice that there
is also a locating pin that aligns the plate with the
disc guide. This locating pin should be on the same
side as the “<” on the body and cap.
Now, remove the disc (6) and disc guide (4), placing
4.
the disc on the bench with the lapped surface up.
Fingertip pressure should be sufficient to remove
these parts.
It is critical that the disc pin not be rotated
when disassembling, cleaning, or reassem-
bling, since this affects the stroke adjustment.
Clean all parts of the body and cap with a good
5.
quality solvent. The disc and plate can then be
cleaned. Place a 4/0 polish cloth or jeweler’s cloth
on a smooth, flat surface and polish the lapped
surfaces. If the parts are badly scarred, do not at-
tempt to relap them, but return them to the factory
for repair or replacement. If the parts are not scarred
too deeply, they can be repaired at minimal cost.
A 0.005 feeler gauge should be used to check the
6.
clearance between the disc and the disc guides.
If the clearance is less than 0.005”, clean the disc
guides with a smooth file.
For Reassembly
Place the disc guide (4) in the body bore with the lo-
7.
cating pin on the same side as the “<” on the body.
Place the disc (6) in the aperture of the disc guided
8.
(4) with the arrow pointing to the index pin hole and
engage the disc pin (8).
In placing the plate (5) in the body (1), notice that
9.
the index pin hole in the lapped surface of the plate
engages the index pin of the disc guide (4).
Replace the cap (2).
10.
Tighten the cap screws (3) uniformly, being cautious
11.
not to apply too much torque. See Torque Require-
ments.
1-1/2” & 2” Sizes
To remove the control valve from the line, follow
1.
instructions under MAINTENANCE.
Secure the body hex in a vise. Remove the cap bolts
2.
(3) and lift the cap (2) straight up.
Remove the pressure ring (4A). Remove the disc
3.
(6) and plate (5) assembly by lifting the assembly
straight up from the body. Place the assembly on the
bench with the disc up.
It is critical that the disc pin not be rotated
when disassembling, cleaning, or reassem-
bling, since this affects the stroke adjustment.
Clean the body and cap bores with a good quality
4.
solvent.
To clean the disc and plate, remove the guide
5.
screws. Place a 4/0 polish cloth or jeweler’s cloth on
a smooth, flat surface and polish the lapped surfac-
es. If the parts are badly scarred, do not attempt to