Maintenance – Sealey MIGHTYMIG100 User Manual
Page 5
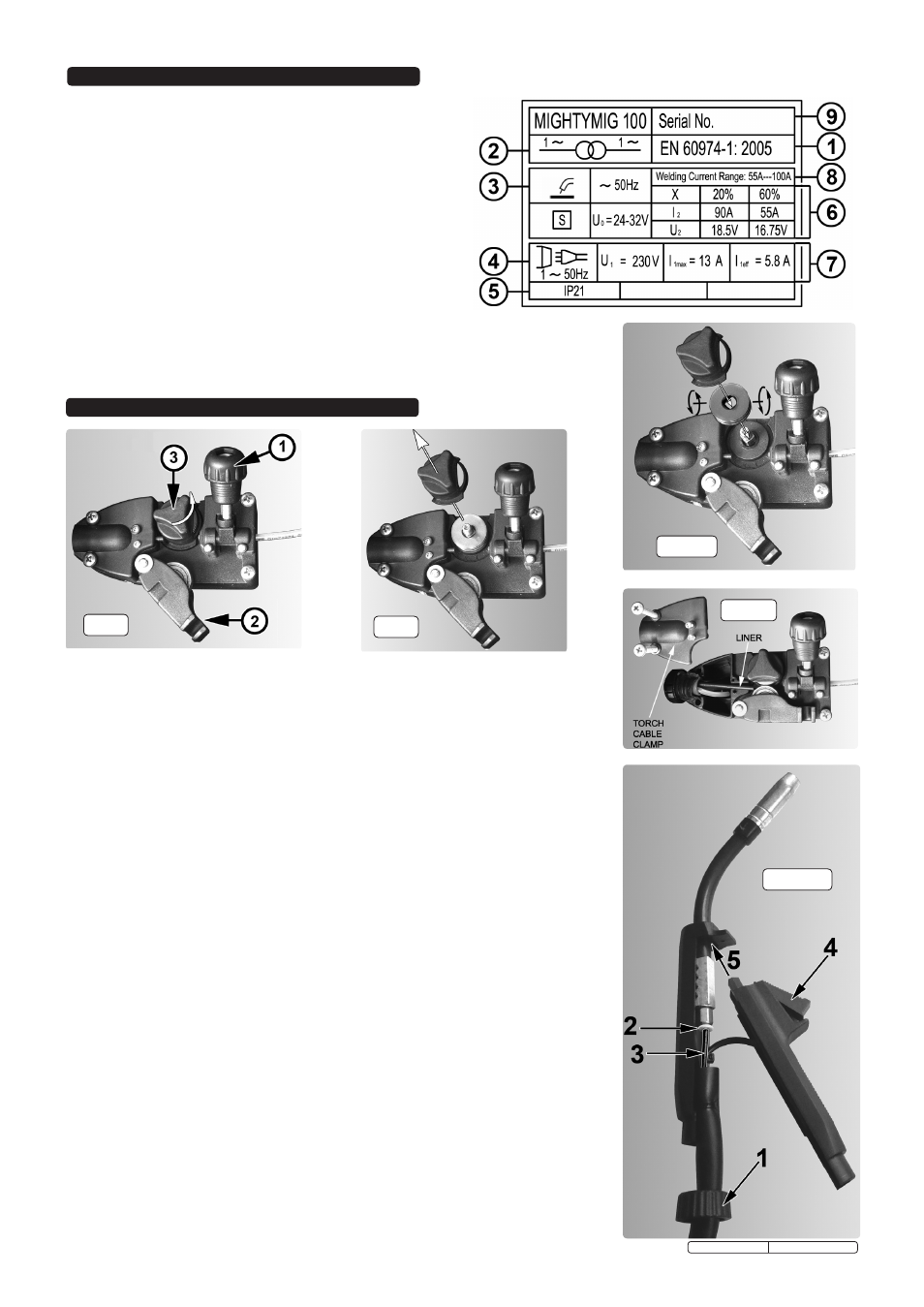
6. MAINTENANCE
On the front panel of the welder is the ratings plate, giving the
following data:
1 - The BS/EU standard relating to the safety and construction of
arc welding and associated equipment.
2 - Single phase transformer.
3 - Symbol indicates welding with a continuous flow of welding wire.
4 - Symbol for Single-phase AC supply.
5 - Rating of internal protection provided by casing.
6 - Output
U
0
Rated minimum and maximum no load voltage.
I
2
, U
2
Current and corresponding voltage.
X
Welding ratio based on a 10 minute cycle.
20% indicates 2 minutes welding and 8 minutes rest,
100% would indicate continuous welding.
7 - Mains Supply U
1
Rated supply voltage and frequency.
I
1
max Maximum current.
I
1
eff Maximum effective current.
8 - Welding current range.
9 - Serial Number. Specifically identifies each welder.
5. RATINGS PLATE
fig.8
fig.9
fig.10
fig.11
fig.12
DANGER! Unplug the welder from the mains power supply before performing maintenance or service.
6.1. Wire feed unit:
6.1.1 Check the wire feed unit at regular intervals. The feed roller wire guide plays an important part in
obtaining consistent results. Poor wire feed affects the weld. Clean the rollers weekly, especially the feed
roller groove, removing all dust deposits.
6.2. Torch:
6.2.1 Protect the torch cable assembly from mechanical wear. Clean the liner from the machine
forwards by using compressed air. If the liner is blocked it must be replaced.
6.3. Turning feed roller IMPORTANT: Turn the feed roller to suit the wire size.
6.3.1 There are two grooves on the feed roller, 0.6mm and 0.9mm. Always have the groove that is being used
on the outside of the roller (nearest to you). To turn the feed roller first loosen the wire tension knob and
move it into its up position (see fig.8-1) then move the tensioning roller assembly to its down position
(see fig.8-2). Take hold of the triangular knob on the roller retainer and rotate it 90°anticlock wise to
release it as shown in fig.8.3. Now pull the roller retainer off the drive spindle to reveal the roller as
shown in fig.9. Pull the roller off the drive spindle, flip it over and put it back on the drive spindle. (See
fig.10) The groove size you require should now be visible on the face of the roller. Push the roller retainer
back onto the drive spindle with the opening facing right. Ensure that the flanges at the base of the
retainer, seat fully into the circular recess in the main moulding and then rotate the retainer through 90°
to lock it in place.
6.4. Contact tip (to remove tip follow steps in 3.1.8):
6.4.1 The contact tip is a consumable item and must be replaced when the bore becomes enlarged or oval.
The contact tip MUST be kept free from spatter.
6.5. Gas cup (to remove cup follow steps in 3.1.8):
6.5.1
The gas cup must also be kept clean and free from spatter. Build-up of spatter inside the gas cup can
cause a short circuit at the contact tip which will result in expensive machine repairs. To keep the contact
tip free from spatter, we recommend the use of anti-spatter spray (MIG/722307) available from your
Sealey dealer.
6.6. Replacing wire liner:
6.6.1
A worn or damaged wire liner will seriously affect the performance of the welder and should be
immediately replaced. First wind the wire back onto the spool and secure it. Remove the four screws
securing the torch cable clamp to the wire feed unit (fig.11) and take off the clamp.
6.6.2 Open the torch case by gripping the torch with one hand and turning the grooved ring at the base of the
torch anticlockwise until it stops, then pull it off the torch onto the torch cable. See fig.12-1.
6.6.3 Take hold of the back end of the moulding which contains the switch and pull it outwards and
downwards to release it from the other moulding as shown in fig.12.
Original Language Version
MIGHTYMIG100 Issue: 2 - 26/02/10