Applied Motion Si3540 User Manual
Page 13
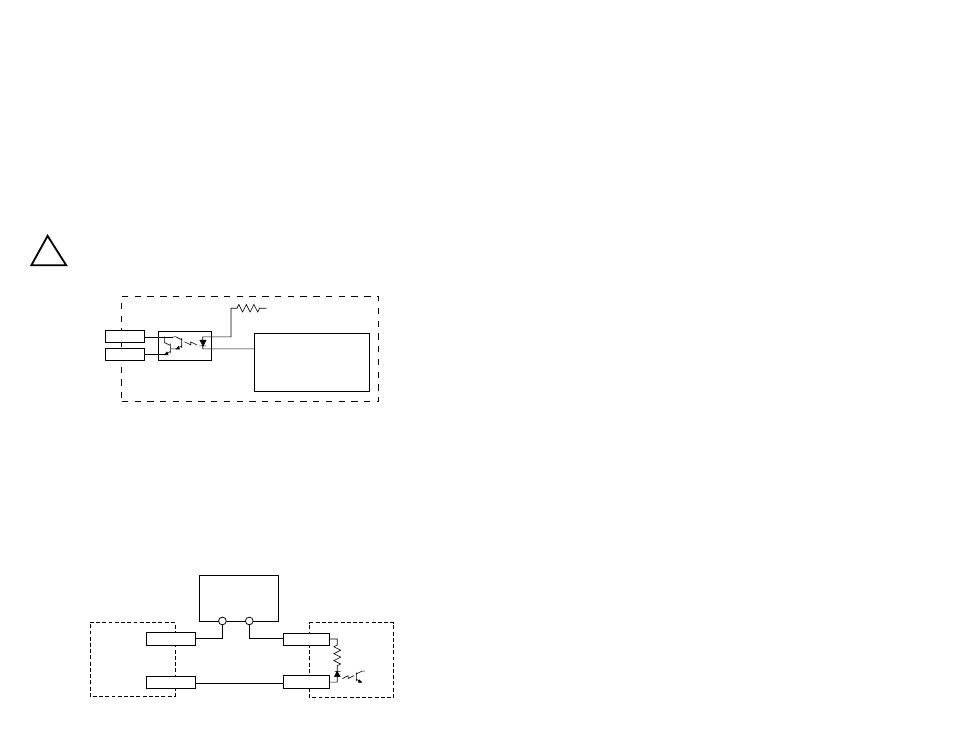
-13-
Wiring Outputs
Before we discuss the output conditions, we need to talk about the circuitry. All
three Si3540 outputs are optically isolated. That means that there is no electrical
connection between the indexer-drive and the output terminals. The signal is
transmitted to the output as light. What you “see” is a transistor (NPN type) that
closes, or conducts current, when the output is “low”. When the output is high, the
transistor is open.
Note: At power-up, the Si3540 sets all three programmable outputs high (open
circuit).
Since there is no electrical conneciton to the Si3540, you must provide the source
of current and voltage, typically from a power supply. You must also limit the
current to less than 100 mA so that the output transistor is not damaged. You
would normally use a resistor for this, but some loads (such as PLC inputs) limit
the current automatically.
The diagram below shows how to connect an Si3540 output to an optically isolated
PLC input.
Schematic Diagram of Si3540 Output Circuit
PLC
COMMON
INPUT
Si3540
OUTPUT-
OUTPUT+
12-24 VDC
Power Supply
+
–
330
+5V
OUT1–
OUT1+
Optoisolator
NEC PS2502
or equiv.
Si3540
Controller Chip
inside Si3540
The maximum voltage between any pair of + and - output
terminals is 24 volts DC. Never connect AC voltages to the
Si3540 output terminals. Maximum current is 100 mA per
output.
!
-14-
Microstepping
Most step motor drives offer a choice between full step and half step resolutions.
In full step mode, both motor phases are used all the time. Half stepping divides
each step into two smaller steps by alternating between both phases on and one
phase on.
Microstepping drives like the Si3540 precisely control the amount of current in each
phase at each step position as a means of electronically subdividing the steps even
further. The Si3540 offers a choice of 13 step resolutions. The highest setting
divides each full step into 254 microsteps, providing 50,800 steps per revolution
when using a 1.8
°
motor.
In addition to providing precise positioning and smooth motion, microstep drives
can be used for motion conversion between different units. The 25,400 step/rev
setting is provded as a means of converting motion from metric to english (there are
25.4 mm in an inch). Other settings provide step angles that are decimal degrees
(36,000 steps/rev makes the motor take 0.01
°
steps). Some settings are used with
lead screws. When the drive is set to 2000 steps/rev and used with a 0.2 pitch lead
screw, you get 0.0001 inches/step.
The microstep resolution of the Si3540 is set by the Si Programmer
TM
software.