Axis synchronism monitoring – BECKHOFF DK9222-0711-0051 User Manual
Page 2
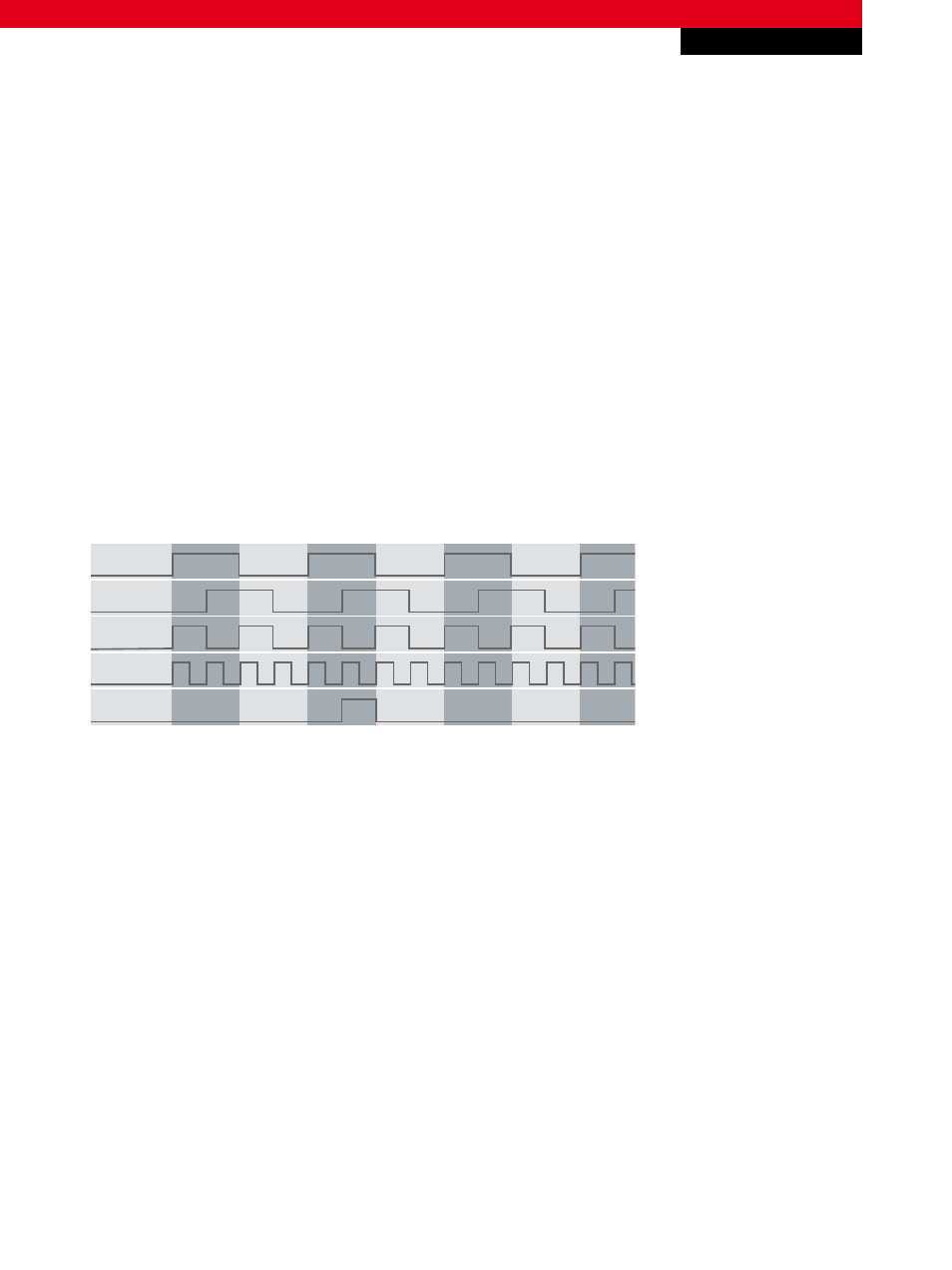
XFC
XFC technology microincrements
Application Note DK9222-0711-0051
Technical background
The incremental encoder is the main link between the mechanical system and the control system for monitoring mechanical
movements. Incremental encoders convert linear or rotary movements into signals that can be analyzed electrically. For rotary
movements, a certain number of light/dark segments applied to a pulse disc are scanned with a light beam. A scannable scale
arranged in the direction of motion is used for capturing linear movements. The accuracy of the returned position is limited by
the encoder resolution. For rotary movements, the resolution corresponds to the quotient of revolution (360°) and number of
segments. It indicates the smallest possible measurable difference between two positions. The more segments, the higher the
resolution and the more precise the position information. A standard encoder has 1000 lines, resulting in an accuracy of 360° /
1000 = 0.36°. This means a rotary movement can be monitored with a precision of ±0.36°. In many cases, this is adequate for
simple positioning tasks, although a finer resolution is required in order to monitor axis synchronism in addition to the position.
CH
A
CH
B
2fold
4fold
CH
N
Fig. 1 Encoder signals with different resolutions
Physical improvement of the resolution through maximization of the encoder segments is only feasible to a certain degree,
since manufacturing tolerances and operating conditions increase the costs of the encoder. A simple and effective way of
maximizing the resolution is to use a second detection point. With two signals that are offset by 90°, three additional edges
are available for detection. They can be used to detect the direction of rotation in addition to the position, and an additional
reference signal for zeroing is output once per revolution. Analysis of these additional edges can refine the resolution by a
factor of 4 (360° / 4 * 1000 = 0.09°), which is why this principle is referred to as quadrature encoder.
Axis synchronism monitoring
Axis synchronism is monitored through cyclic position polling and interpolation of these values within the PLC. The timebase
for the interpolation is provided by the strict cycle-linked processing of the instructions in the PLC. With a cycle time of 1 ms
(which is common for motion applications), the positions are scanned with a timebase of 1 ms. However, the real encoder
scanning intervals are not as rigid as those of the PLC and vary. The reason for the irregularity is inherent to the functional
principle variation of the fieldbus transfer times (jitter) and the encoder inaccuracy with ±½ edge. Since the PLC does not take
this discontinuity of the polling intervals into account and assumes a constant interval duration, the position representation
New Automation Technology
Beckhoff
2
For application notes see disclaimer on the last page