Flowserve Twin Screw Rotary User Manual
Page 30
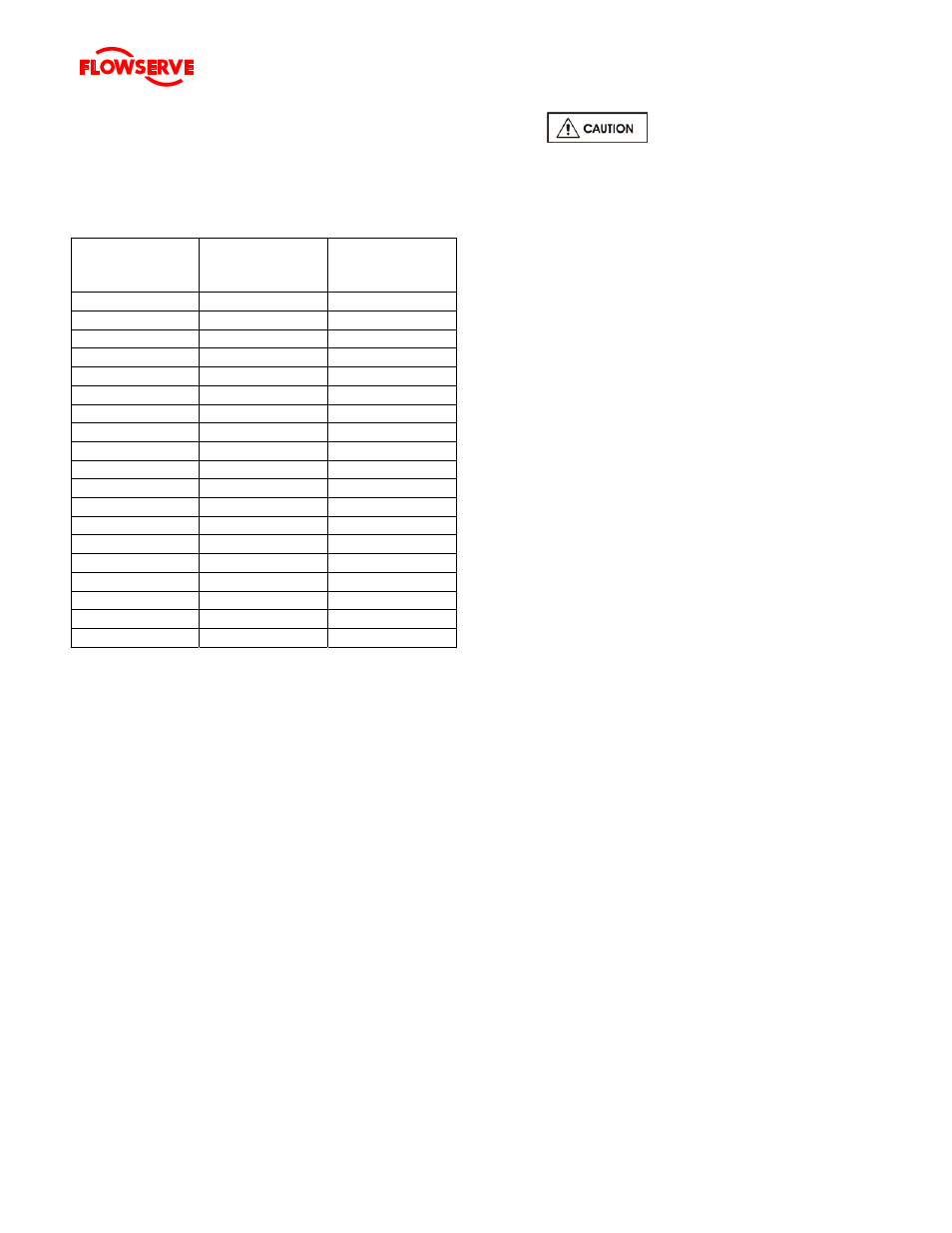
TWIN SCREW PUMPS. ORIGINAL USER INSTRUCTIONS. ENGLISH. 71569243 – 07/10
Page 27 of 53
®
5.2.2 Oil Levels
The following table provides reference oil levels
(below shaft centreline) for the housings on external
bearing pumps. Note that once the initial oil level is
set in the gear housing it should be adjusted after
startup following the directions in section 5.2.3.
Pump Size
Gear Housing
Oil Level
mm (in)
Opposite End
Oil Level
mm (in)
NA
21.3 (.84”)
16 (.63”)
NC (RTG)
30 (1.18”)
21.1 (.83”)
ND
32.5 (1.28”)
23.1 (.91”)
NE
36.6 (1.44”)
26.7 (1.05”)
NF (RTG)
42.9 (1.69”)
32.5 (1.28”)
NFX (RTG)
47.8 (1.88”)
32.5 (1.28”)
NG (RTG)
47.8 (1.88”)
32.5 (1.28”)
NH (RTG)
52.3 (2.06”)
38.6 (1.52”)
NI (RTG)
57.2 (2.25”)
42.4 (1.67”)
NII (RTG)
57.2 (2.25”)
42.4 (1.67”)
NIM (RTG)
57.2 (2.25”)
42.4 (1.67”)
NIJ (RTG)
71.4 (2.81”)
54.9 (2.16”)
NJ (RTG)
79.2 (3.12”)
58.7 (2.31”)
NL (RTG)
79.2 (3.12”)
58.7 (2.31”)
NLX (RTG)
88.9 (3.50”)
58.7 (2.31”)
NM (RTG)
84.1 (3.31”)
66.5 (2.62”)
NP24 (RTG)
104.6 (4.12”)
69.9 (2.75”)
NP18 (RTG)
104.6 (4.12”)
69.9 (2.75”)
*RTG signifies rear timing gear configuration.
5.2.3 Checking running oil level in gear housing
If the oil reservoir is filled to the level indicated on the
column gauge (when pump is at running speed),
ample lubrication will be provided for the timing gears
and bearings contained in the housing.
However, if field operating conditions (temperature,
etc.) vary considerably from standard, the level must
be checked internally to insure proper lubrication.
Follow the procedure as outlined below.
a) Remove the filler vent plug.
b) With the pump running at rated speed and
operating temperature, the timing gears should
pick up enough oil to create a fine mist
throughout the gear case. Too much oil will
cause overheating. Too little oil will cause gear
and bearing failure. Adjust oil level until fine mist
is present.
c) Replace vent filler and pipe plugs.
d) Repeat procedure periodically to ensure proper
lubrication and extended pump life.
5.2.4
Lubrication schedule for
external bearing pump
5.2.4.1 Requirements for oil lubricated bearings
Normal oil change intervals are 4 000 operating hours
or at least every 6 months. For pumps on hot service
or in severely damp or corrosive atmosphere, the oil
will require changing more frequently. Lubricant and
bearing temperature analysis can be useful in
optimizing lubricant change intervals.
The lubricating oil should be a high quality mineral oil
having foam inhibitors. Synthetic oils may also be
used if checks show that the rubber oil seals will not
be adversely affected.
The bearing temperature may be allowed to rise to
50 ºC (122 ºF).above ambient, but should not exceed
82 ºC (180 ºF). A continuously rising temperature, or
an abrupt rise, indicate a fault.
Oils used in the bearing housing should meet the
following requirements.
1. Oxidation Stability Specification per AGMA
Standard 250.04 table 1, page 9.
2. Foam Suppression Specification per AGMA
Standard 250.04 table 1, page 9.
At initial start-up, oil must be drained completely and
replaced after one week or 100 hours running time
(except for temperatures above 121
°C (250 °F)).
For normal running temperatures between 10
°
and 65
°C (50 ° and 150 °F):
Indoor installations or outdoor summer conditions
with ambient temperature of –5
° to 35 °C (20 ° to 95
°F).
Oil should meet AGMA Standard 250.04 AGMA
Lubricant No. 5, viscosity range 198 to 242 cST at
40
°C.
Typical oils per Column "A" in Section 5.2.1. Change
oil every six months or seasonally.
For winter running temperatures between –18
°
and 38
°C (0 ° and 100 °F):
Cold Starting conditions with ambient temperatures
of –5
° to 10 °C (20 ° to 50 °F).
Oil should meet AGMA Standard 250.04 AGMA
Lubricant No. 2EP, viscosity range 60 to 75 cST at
40
°C.