0 description 3.1 configuration, 2 nomenclature, 3 design of major parts – Flowserve MSP User Manual
Page 13
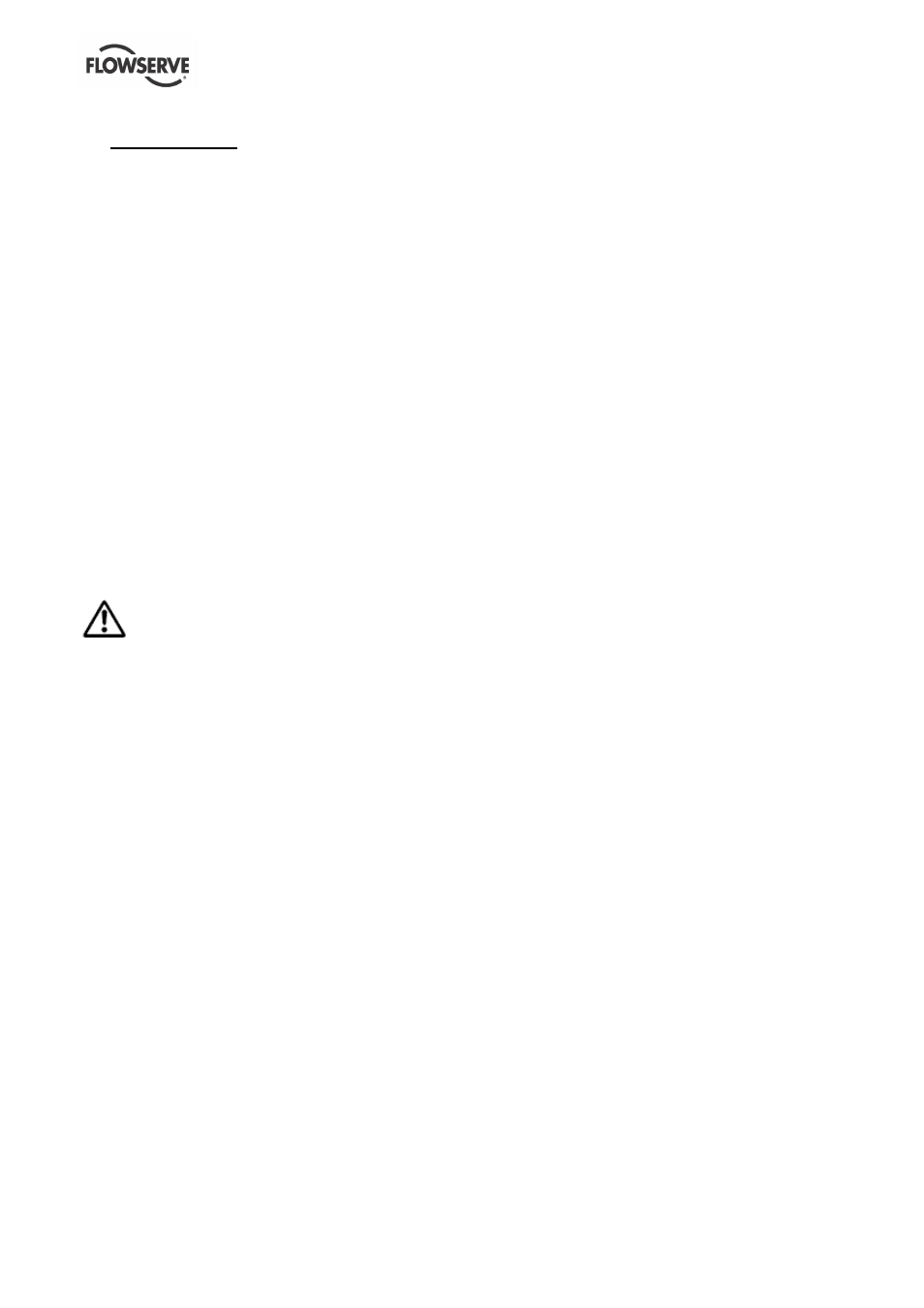
MSP USER INSTRUCTIONS ENGLISH - 07/14
Page 13 of 35
3.0 DESCRIPTION
3.1 Configuration
The model MSP belongs to Flowserves family of API
610 vertical inline pumps.
MSP pumps are directly coupled to a medium speed
induction motor, which is driven by a VFD (Variable
Frequency Drive). The pump unit is available in 5
motor sizes:
22 kW
max. 6000 rpm
37 kW
max. 6000 rpm
55 kW
max. 8000 rpm
80 kW
max. 8000 rpm
120 kW
max. 8000 rpm
The hydraulics are designed for low flow at high
heads and consist of:
•
a semi open radial vaned impeller to guarantee
optimum performance
•
a circular volute with a single coned diffuser to
minimize hydraulic forces
The pump unit is available in single stage or two
stage opposed impeller configuration. Both versions
are available with high and low flow hydraulics. For
low NPSHA applications an inducer is available.
The sense of rotation of the pump is
clockwise (CW), looking from the coupling to the shaft
end of the pump.
3.2 Nomenclature
Example:
MSP
22A-Ind ….1 stage
MSP2 22A-Ind ….2 stage
M S P
Medium Speed Pump
22/37/55/80/120 Motor power in kilowatts at
maximum speed
A
Hydraulic for higher capacities
B
For lower capacities
C
For higher power
Options:
-Ind
Inducer
3.3 Design of major parts
3.3.1 Pump casing
Vertical inline design with flanged suction elbow and
integrated baseplate. It is directly flanged to the motor
stand, which itself is flanged to the motor. Back pull
out design for easy maintenance, so the casing
remains on its foundation in case of repair.
3.3.2 Hydraulics
A circular volute in combination with a single coned
diffuser is inserted into the pump casing. A radial
vaned semi open impeller is used to ensure optimal
performance.
3.3.3 Motor
Medium speed induction motor for vertical
arrangement. The bearings are grease lubricated and
designed to take the pump hydraulic forces.
3.3.4 VFD
The VFD allows to operate the connected motor with
variable speed. Generally we supply the converter as
a completely wired unit including all contactors and
fuses. A RFI (radio frequency interference) - filter is
included to meet the requirements of the public
electricity supplier. All necessary safety features are
included, so that the unit needs only be connected to
the electrical power supply.
3.3.5 Coupling
The pump is rigid coupled to the motor. So the motor
bearings take all the load from the hydraulic forces.
The shaft of an electric motor must be a magnetic
material, so no stainless steels can be used. To
overcome this material restriction the impeller is
located on a separate shaft which is clamped to the
motor shaft via an annular spring clamping device.
Therefore also all kind of stainless steels and higher
Alloy can be used for pump shaft.
The coupling has the following design data:
Max. transm. torque of coupling = 1040 Nm (767 ft-lbs]
Max. transm. axial force = 59 kN (13275 lbs)
3.3.6 Control Circuit
The control circuit control, protect and adjust the main
circuit within the VFD cabinet.
Two filter-fan’s (12M1, 12M2) situated in the front
door obtain constantly the temperature
of the cabinet to avoid electronics damage and keep
pure from dirty air in the environment.
They start normally after switched-on the main switch
of the cabinet.
The PTC-thermistor’s tripping device (12K1) observe
the winding temperature of the main motor. When the
temperature exceeds the max. allowable value the
auxiliary contact (NC)
which is in line with the control circuit fuse (10F2) and
the auxiliary contact of the external motor fan (13Q1)
interrupt the safety loop requested by international
regulations. This cause an immediately stop of the
VFD itself.