3 direction of rotation, 4 guarding, 5 priming and auxiliary supplies – Flowserve Mark 3 ISO Durco User Manual
Page 17: 6 starting the pump, 7 running the pump, 8 stopping and shutdown, Guarding (5.4), Priming and auxiliary supplies (5.5), Running the pump (5.7), Vibration (5.7.2)
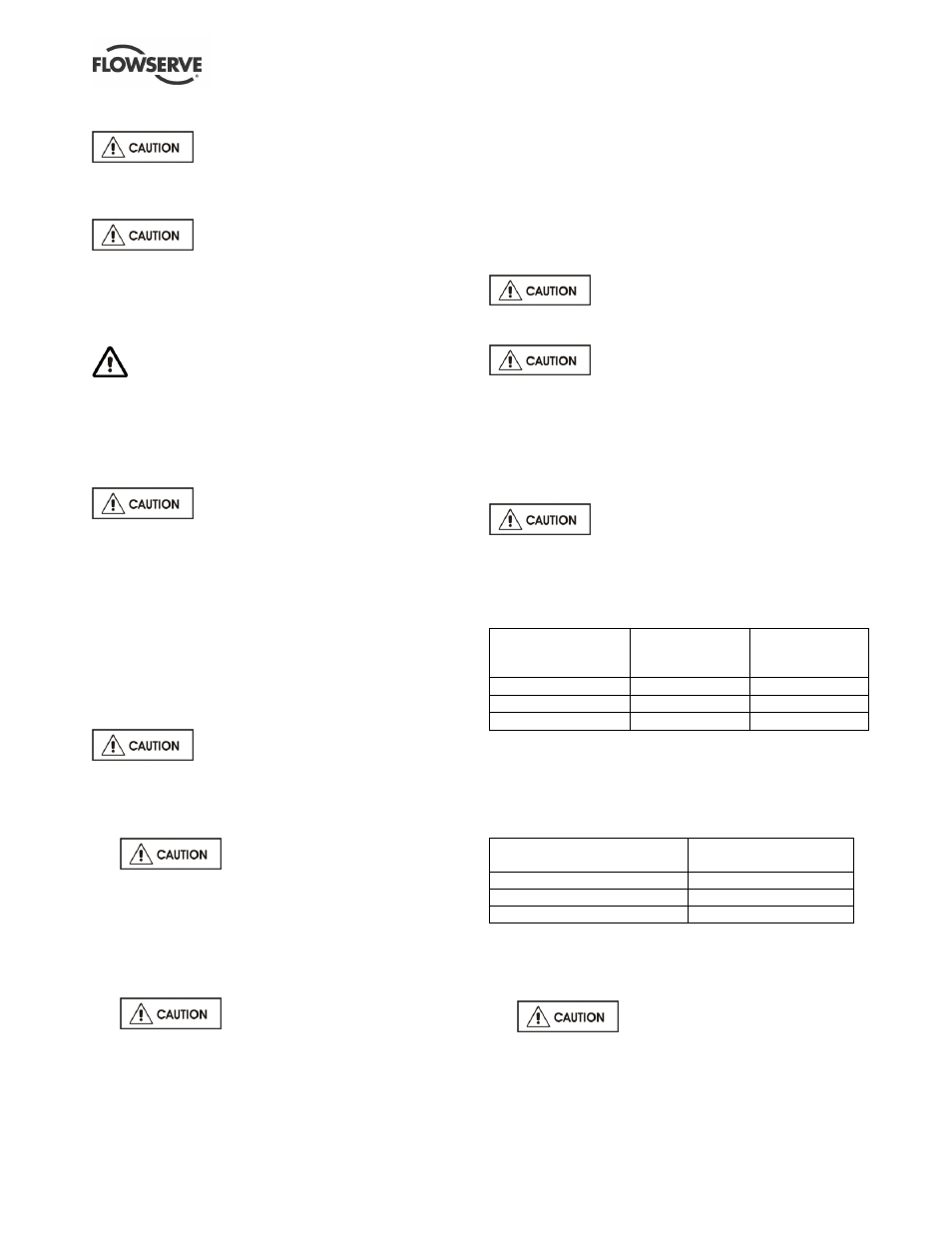
DURCO MARK 3 ISO CLOSE COUPLED ENGLISH 26999985 02-14
Page 17 of 32
flowserve.com
5.3 Direction of rotation
Briefly run or jog the motor and observe
the direction of rotation of the coupling or motor fan.
Ensure the pump is given the same direction of rotation
as the pump direction arrow on the bracket.
If maintenance work has been carried
out to the site's electricity supply, the direction of
rotation should be re-checked as above in case the
supply phasing has been altered.
5.4 Guarding
Guarding is supplied fitted to the pump set. If
this has been removed or disturbed ensure that all the
protective guards are securely refitted.
5.5 Priming and auxiliary supplies
5.5.1 Filling and priming
Ensure inlet pipe and pump casing is
completely full of liquid before starting continuous
duty operation.
Priming may be carried out with an ejector, vacuum
pump interceptor or other equipment, or by flooding
from the inlet source.
When in service, pumps using inlet pipes with foot
valves may be primed by passing liquid back from the
outlet pipe through the pump.
5.5.2 Auxiliary supplies
Ensure all electrical, hydraulic,
pneumatic, sealant and lubrication systems (as
applicable) are connected and operational.
5.6 Starting the pump
a)
Ensure flushing and or heating
liquid supplies are turned ON, before starting pump.
b) CLOSE the outlet valve.
c) OPEN all inlet valves.
d) Prime the pump.
e) Start motor and check the outlet pressure.
f) If the pressure is satisfactory, slowly OPEN the
outlet valve.
g)
Do not run the pump with the outlet
valve closed for a period longer than 30 seconds.
h) If NO pressure, or LOW pressure, STOP the
pump. Refer to section 7, Faults; causes and
remedies for fault diagnosis.
5.7 Running the pump
5.7.1 Pumps fitted with mechanical seal
Mechanical seals require no adjustment. Any slight
initial leakage will stop when the seal is run in.
Before pumping dirty liquids it is advisable, if possible, to
run the pump in using clean liquid to safeguard the seal
face.
External flush or quench should be
started before the pump is run and allowed to flow for a
period after the pump has stopped.
Never run a mechanical seal dry,
even for a short time.
5.7.2 Normal vibration levels, alarm and trip
For guidance, pumps generally fall under a classification
for rigid support machines within the International
rotating machinery standards and the recommended
maximum levels below are based on those standards.
Alarm and trip values for installed
pumps should be based on the actual measurements
(N) taken on the pump in the fully commissioned as
new condition. Measuring vibration at regular
intervals will then show any deterioration in pump or
system operating conditions.
Vibration velocity
–
unfiltered
Horizontal pumps
15 kW mm/sec
(in./sec) r.m.s.
> 15 kW
mm/sec (in./sec)
r.m.s.
Normal N
3.0 (0.12)
4.5 (0.18)
Alarm N x 1.25
3.8 (0.15)
5.6 (0.22)
Shutdown trip N x 2.0
6.0 (0.24)
9.0 (0.35)
5.7.3 Stop/start frequency
Pump sets are normally suitable for the number of
equally spaced stop/starts per hour shown in the
table below. Check capability of the driver and
control/starting system before commissioning.
Motor rating kW (hp)
Maximum stop/starts
per hour
Up to 15 (20)
15
Between 15 (20) and 90 (120)
10
Above 90 (120)
6
Where duty and standby pumps are installed it is
recommended that they are run alternately every week.
5.8 Stopping and shutdown
a)
Close the outlet valve, but ensure
that the pump runs in this condition for no more
than a few seconds.
b) Stop the pump.