6 fastener torques, 7 setting impeller clearance, 8 disassembly – Flowserve CPXPM User Manual
Page 19
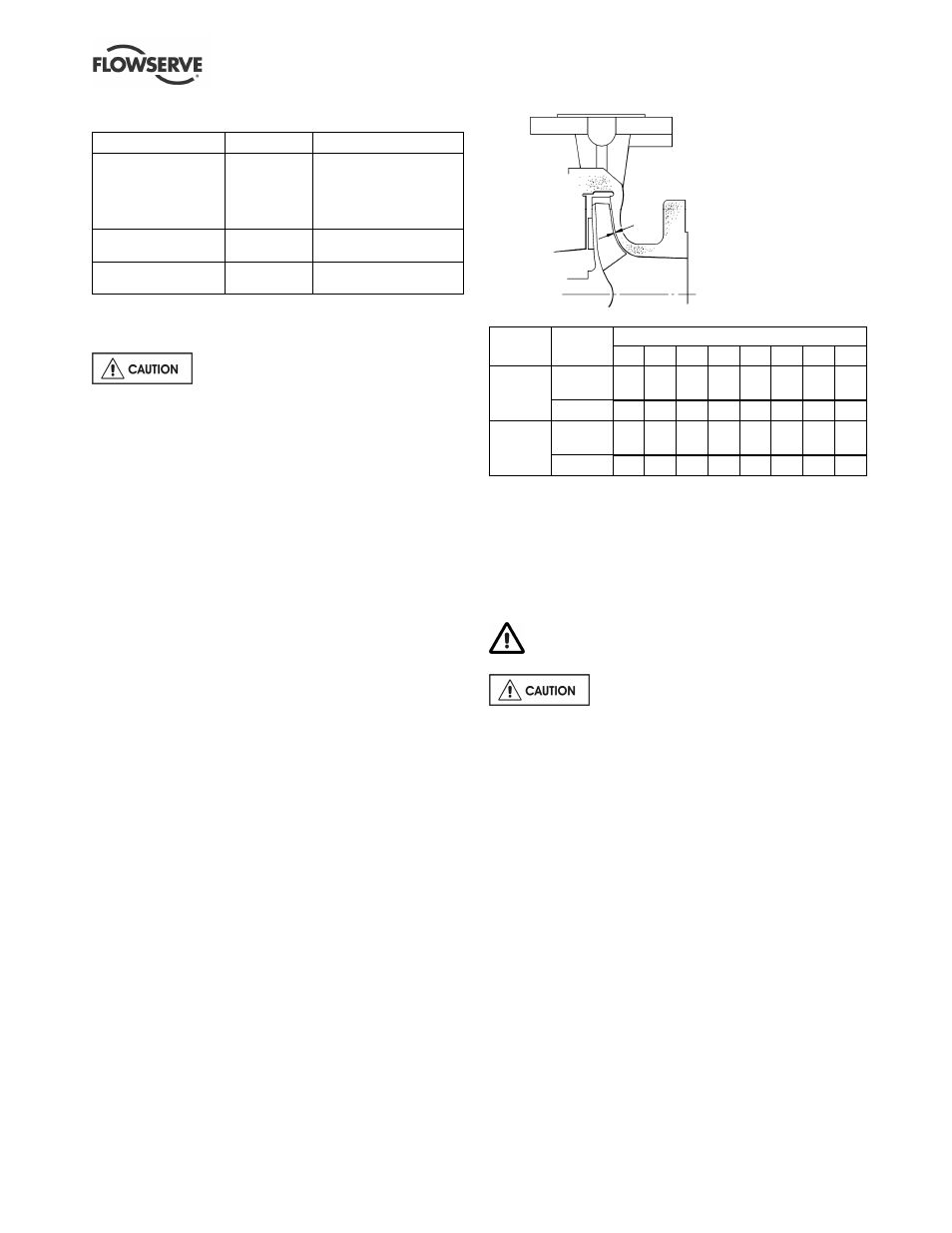
CPXPM USER INSTRUCTIONS ENGLISH 71569160 09-09
Page 19 of 28
flowserve.com
6.6 Fastener torques
Screw position
Screw size
Torque Nm (lbf·ft)
Casing and
seal cover
M8
M10
M12
M16
M20
16 (12)
25 (18)
35 (26)
80 (59)
130 (96)
Muff coupling
M8
M10
30 (22)
58 (43)
Cartridge seal sleeve
(where applicable)
M5
M8
5.5 (7) *
16 (22) *
* Where a torque wrench is unavailable, slightly tighten the
setscrews to centralize the cartridge seal, then tighten with a T-bar
until a torsional twist between 60 and 90 degrees is achieved. The
torque applied will be approximate to that recommended.
Non-metalic gaskets incur creep
relaxation - before commissioning the pump check
and retighten fasteners to tightening torques stated.
6.7 Setting impeller clearance
This procedure may be required after the pump has
been dismantled or a different clearance is required.
Before carrying out this procedure ensure that the
mechanical seal(s) fitted can tolerate a change in
their axial setting, otherwise it will be necessary to
dismantle the unit and reset the seal axial position
after adjusting the impeller clearance.
a) If a cartridge seal is fitted loosen it from the shaft.
b) Disconnect the muff coupling and clean up the
bores.
c) Clean motor shaft and stubshaft and deburr
where necessary.
d) Replace muff coupling, ensuring that the
grubscrew locates in the stubshaft.
e) The motor end coupling bolts should be slacker
than the pump end coupling bolts so that the
coupling and stubshaft can be rotated relative to
the motor shaft.
f) The motor shaft should be prevented from
rotating by using a C-spanner located in the
keyway (where possible) or by locking the fan
end of the motor.
g) Rotate the coupling until the impeller contacts the
pump casing. This is the zero clearance position
or datum for setting the front clearance.
h) Mark the bracket with a pen and, whilst preventing
the motor shaft rotating, turn the coupling in the
opposite direction by the recommended number of
notches as indicated in the table. For the
remaining steps, take care not to rotate the pump
shaft relative to the motor shaft.
i)
Carefully loosen and back off the grubscrew and
tighten the coupling bolts, ensuring that the gap
is equal between the coupling halves.
Clearance settings:
Motor frame size
Impeller
diameter
80
90
100 112 132 160 180 200
Clearance
(mm)
0.3 0.3
0.3 0.3 0.3 0.3 0.3 0.3
Up to
210 mm
Notches
7
7
7
7
7
8
8
8
Clearance
(mm)
0.4 0.4
0.4 0.4 0.4 0.4 0.4 0.4
211 to
315 mm
Notches
8
8
8
8
8
9
9
9
j)
Torque the screws to the specified values:
M 8 - 30 Nm (22 lbf•ft)
M 10 - 58 Nm (43 lbf•ft)
k) Check that the shaft can turn freely without binding.
l)
If a cartridge seal is fitted it should be reset at this
point.
6.8 Disassembly
Refer to Safety section before dismantling the
pump.
Before dismantling the pump for
overhaul, ensure genuine Flowserve replacement
parts are available.
Refer to sectional drawings for part numbers and
identification. See section 8, Parts lists and drawings.
6.8.1 General
a) Close suction and discharge valves and drain
liquid from the pump.
b) Remove screws from pump casing and pull motor
complete with rotating assembly from back of
pump casing, which will be left connected in
position in the pipework.
c) Unclip the coupling guards.
d) Take out the muff coupling screws and remove
coupling.
6.8.2 Pumps with single seals
a) Prevent the motor shaft from rotating.
b) Carefully rotate the impeller in an anti-clockwise
rotation, whilst supporting the impeller, until it
releases from the adjustment stud. Take care
not to damage the seal.