Transducer operation, Converting positioner input signal, Calibration – Flowserve NT3000 Series User Manual
Page 4
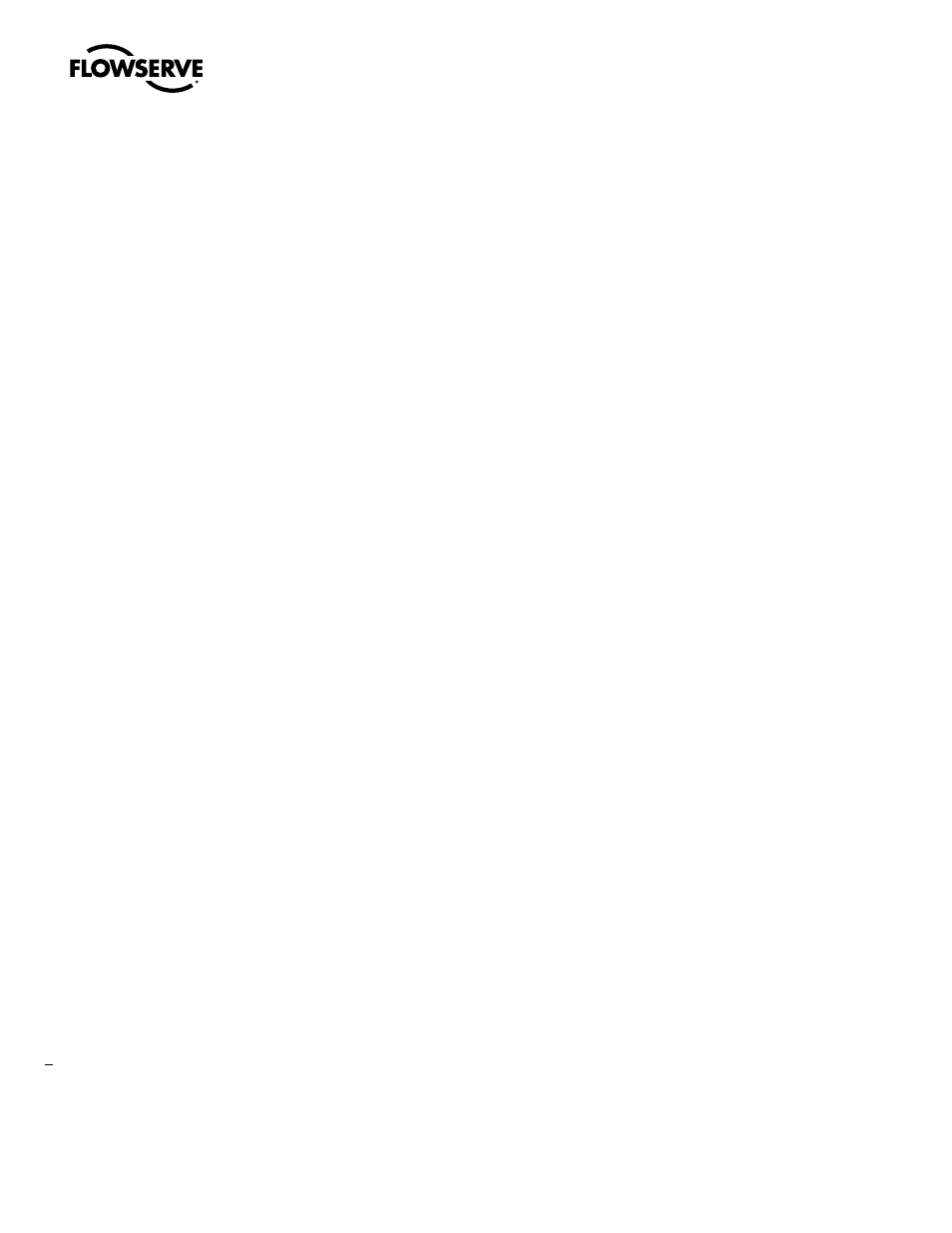
NT 3000 Series Electro-Pneumatic Transducer Module FCD VLAIM0047-00 - 09/04
4
Transducer Operation
The NT 3000 is considered an ‘active’ I/P transducer. An active
device has gain and controls the current through transistors, diodes,
capacitors, resistors, and integrated circuits. A ‘passive’ transducer
has no gain characteristics and consists of a large coil with a fixed
resistance (i.e., fixed voltage drop). The effective impedance of an active
transducer varies with the input current. The NT 3000 transducer is a
current-powered device that can be modeled as a 5.7 V zener diode in
series with a 17-ohm resistor. For a DCS system output of 4-20 mA,
the voltage drop across the transducer varies between 5.7 V and 6.1
V while the impedance varies between 1330 ohms and 270 ohms.
Flowserve recommends an operating voltage of 6.5 VDC (i.e. the DCS
system should allow for at least 6.5 V loop load across the NT 3000
terminals; not that a 6.5 V supply is connected to the transducer.)
The transducer receives a 4 to 20 mA signal and converts it to a
3-15 psi output signal.
The supply pressure to the NT 3000 is filtered as it passes through
a field-replaceable, coalescing filter element in the transducer. The
air then passes through an internal pressure regulator that regulates
the pressure to approximately 23 psi. The supply pressure then goes
through an orifice that restricts the flow and air consumption. Refer to
Figures 2 and 3.
The air is further controlled to 3-15 psi using a diaphragm flapper that
is attracted by an electromagnet to a nozzle. A temperature-compen-
sated piezoresistive pressure sensor mounted on a circuit board senses
the transducer output pressure. The pressure sensor and circuitry
create a feedback loop that determines how much current to send to the
electromagnet for a desired pressure output. The electromagnet in the
feedback loop varies the nozzle-flapper spacing, which regulates the I/P
output pressure to 3-15 psi.
Converting Positioner Input Signal
XL series or Beta series positioners can be adapted to
4 to 20 mA (I/P) or pneumatic signal (3-15 psi). For pneumatic opera-
tion, the positioner is fitted with the pneumatic adapter. For electrical
operation, the positioner is equipped with the NT 3000 transducer.
Refer to the appropriate Flowserve Installation, Operation, Maintenance
Instructions.
Calibration
Valtek positioners mounted on valves are calibrated at the factory;
however, it may be necessary to recalibrate the transducer before oper-
ating the valve. The zero and span of the NT 3000 transducer are set to
close tolerances at the factory and normally do not need adjustment.
If required, the NT 3000 transducer can be recalibrated either while
mounted on the XL or Beta positioner or while mounted on a calibra-
tion manifold. Calibration manifolds are available from the factory
(PN 097370.999.000). To calibrate the I/P transducer zero and span
settings, refer to Figures 4 or 5 and proceed as follows.
NOTE: Although calibration can be accomplished using the output
pressure gauge on the I/P transducer, its accuracy is ±3 percent. It is
recommended that the standard gauge be removed for calibration and
that more accurate calibration equipment of ±0.1 percent of span be
used. The pressure gauge port is
1
⁄
8
-inch NPT.
1. Connect the 30-150 psi supply pressure to the positioner or calibra-
tion manifold.
2. Remove the I/P transducer housing cover.
c
WARNING: Disconnect power to the I/P module before
removing the housing cover in explosive atmospheres;
otherwise, personal injury may occur.
3. Connect an adjustable current source to the terminal block on the
circuit board.
NOTE: The zero and span adjustments are multi-turn
potentiometers (pots) that have no stops on the ends of their travel;
however, they have a slip clutch to prevent damage from over-
adjustment. The pots also make a clicking noise when they have
reached the limits of their adjustment.
4. Apply a 4 mA signal to the input. Adjust the zero trim pot to achieve
a 3 psi output. The output will increase with clockwise rotation of
the zero trim pot.
5. Increase the input signal to 20 mA. Adjust the span trim pot to
achieve a 15 psi output. The output will increase with clockwise
rotation of the span.
6. Recheck the zero setting by repeating Step 4. The span adjustment
may affect the zero setting.
7. Repeat Steps 4, 5 and 6 until the proper adjustments are obtained.