Valve maintenance – Flowserve Valtek Mark One and Mark Two Control Valves User Manual
Page 7
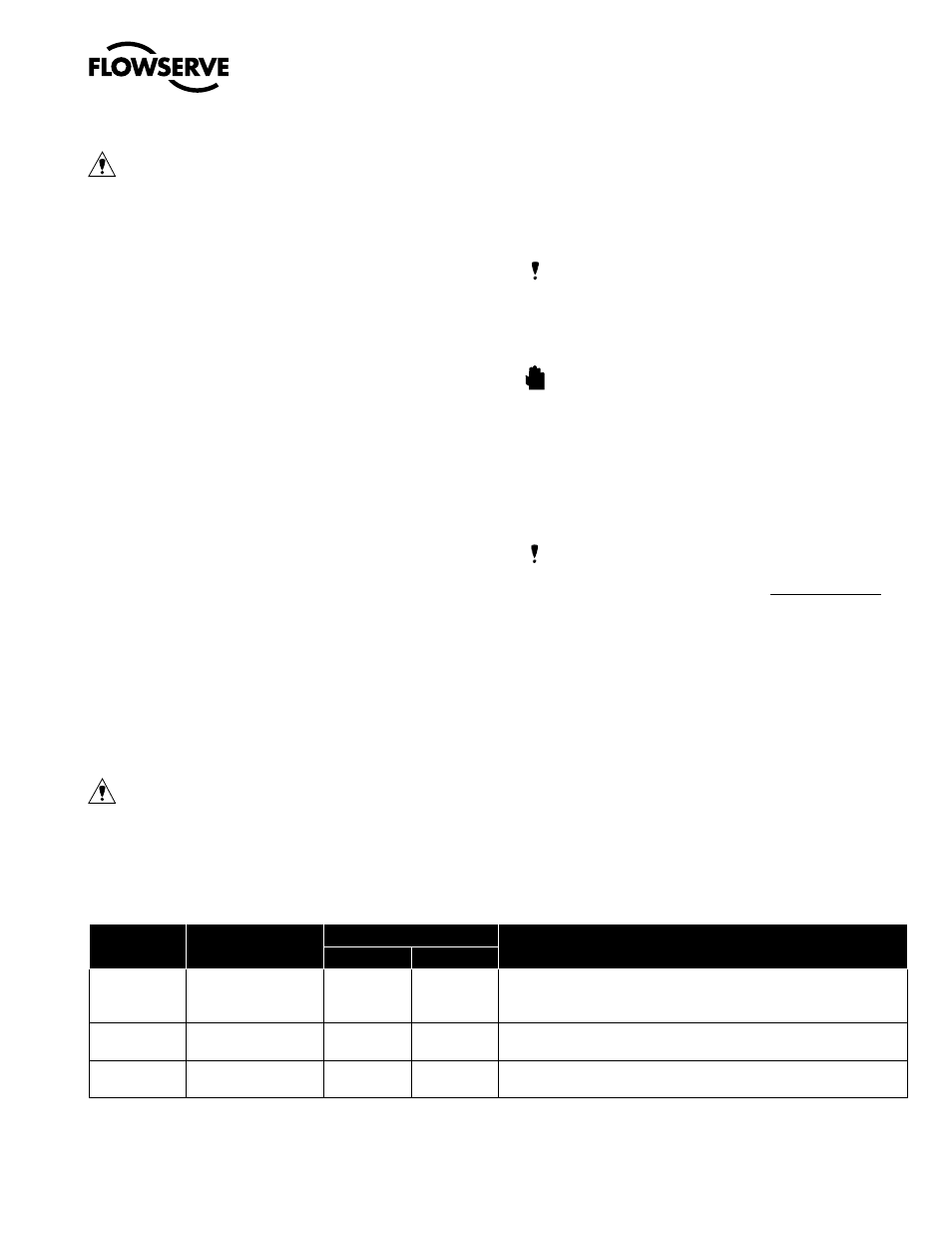
7
®
Valtek Mark One and Mark Two Control Valves FCD VLENIM001-01-AQ - 8/14
5.5.
If the valve is supplied with a lubricator fitting, check lubri-
cant supply and add lubricant if necessary. See Table I for
common lubricants.
5.6.
If possible, stroke the valve and check for smooth, full-
stroke operation. Unsteady stem movement could indicate
an internal valve problem.
NOTE: Due to excessive friction a dry graphite packing can
cause the plug stem to move in a jerky fashion. Lubrication
of graphite packing will provide smoother stroking. Lubri-
cation can be done by using a bonnet lubricator or by lib-
erally coating each packing ring by hand during installation.
Please refer to Table I for lists of common lubricants.
WARNING: Keep hands, hair and clothing away from all
moving parts when operating the valve. Failure to do so can
cause serious injury.
5.7.
Make sure positioner linkage and stem clamp are securely
fastened. If the stem clamp is loose, check plug thread en-
gagement (refer to the “Reassembly and Installation” sec-
tion for the correct procedure on aligning the plug with the
seat). Tighten stem clamp nut.
NOTE: Refer to the appropriate User Manuals when adjust-
ing positioners and providing maintenance to actuators.
Current User Manuals are available at www.flowserve.com.
5.8.
Verify that the takeoff arm and follower arm are not binding
at either end of the stroke. The follower arm attached to the
positioner should be free to move slightly when the valve is
at both ends of the stroke.
5.9.
Ensure all accessories, brackets and bolting are securely
fastened.
5.10.
If possible, remove air supply and observe actuator for cor-
rect fail-safe action.
5.11.
Check rubber actuator bellows for splits, cuts or wear.
CAUTION: Do not overtighten packing. This can cause exces-
sive packing wear, high stem friction that may impede plug
movement and can damage the packing. Over-tightening
packing will not improve the stem seal unless the packing
has been previously damaged. Damaged packing should be
replaced.
4.5.
Make sure the valve fails in the correct direction in case of air
failure. This is done by turning off the air supply and observ-
ing the failure direction.
5. Valve Maintenance
At least once every six months, check for proper operation
by following the preventative maintenance steps outlined
below. These steps can be performed while the valve is in-
line and, in some cases, without interrupting service. If an
internal problem is suspected, refer to Section 6, Valve Dis-
assembly and Inspection.
5.1.
Look for signs of gasket leakage through the end flanges and
bonnet. Re-torque flange and bonnet bolting (if required).
Refer to Table II for bonnet bolt torque values.
5.2.
Examine the valve for damage caused by corrosive fumes or
process drippings.
5.3.
Clean valve and repaint areas of severe oxidation.
5.4.
Check packing box bolting for proper tightness and packing
leakage. If packing leakage is noticed, packing maintenance
is required. Refer to the packing installation manual (docu-
ment number VLAIM040) for specific details on maintaining
the style of packing supplied.
CAUTION:
Do not overtighten packing. This can cause exces-
sive packing wear and high stem friction that may impede
stem movement. Packing that is tightened too tight will typ-
ically not seal correctly.
Lubricant
Manufacturer
Temperature Range
Application Description
°F
°C
Krytox®
E.I DuPont
-5 to 550
-20 to 285
Fluorinated general purpose grease; handles common liquids and
gasses; good lubricity in harsh mediums; nonflammable, chemically
inert; will not harm plastic or metal parts
GP 460
Acheson Colloids
Company
32 to 1000
0 to 540
Graphite in petrolatum; high pressure; anti-galling; graphite remains
above 600°F / 316°C
725
Chesterton
32 to 2600
0 to 1425
Nickel, Aluminum and graphite in oil suspension; provides protection
with an ultra-thin coating of nickel particles
Table I: Common Packing Lubricants
STOP!