Maintenance, Rebuilding, Worcester controls – Flowserve 51 Series Flanged Ball Valves User Manual
Page 2
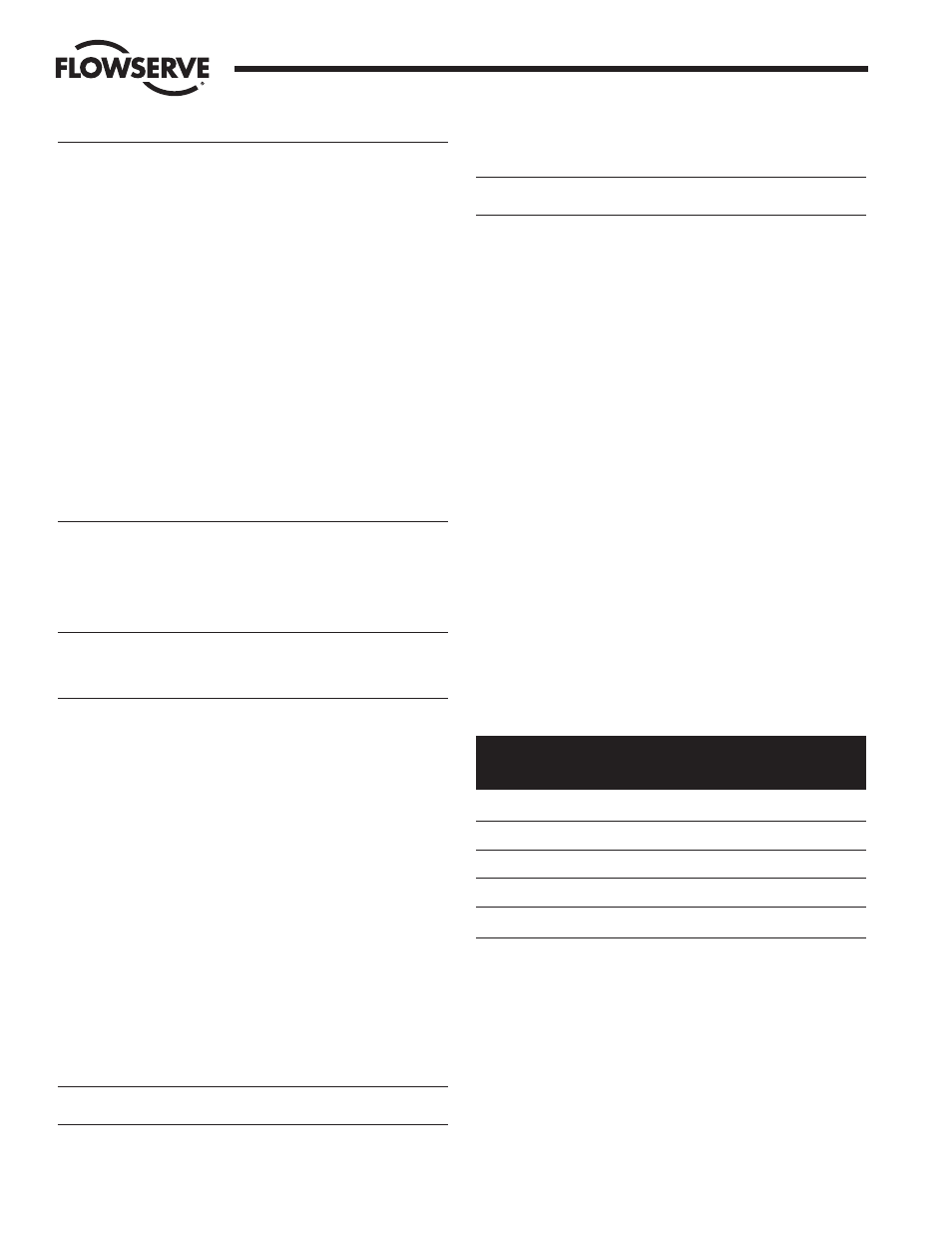
Flow Control Division
Worcester Controls
2
Z|x" - 2" 51/52 One-piece, Flanged Ball Valves
WCAIM2014
CAUTIONS: The fluoropolymer and UHMWPE body seals (codes T
and U) and the coated stainless steel gaskets (codes M and G)
make excellent seals. However, some points of caution in their use
need emphasizing.
No fluoropolymer or UHMWPE part (except seats) or seat back seal
is reusable. Coated stainless steel gaskets are also not reusable.
Upon disassembly of the valve, they should be discarded and
replaced with new parts.
Care must be taken to avoid scratching the fluoropolymer or
UHMWPE seals, or the coating of the gaskets during installation.
Light lubrication of these seals can help prevent damage.
Care must also be taken when handling a graphite thrust bearing,
stem seal, or seat back seal. These parts can be easily damaged
by squeezing the OD of the seal. Parts are to be handled on the flat
surfaces rather than the OD.
The ball used in valves with “A” and “G” (filled metal) seats is
round to special tolerances. To ensure proper contact with the seat,
do not drop, dent or scratch the ball during handling. These balls
also have an anti-galling coating. DO NOT use uncoated balls with
filled metal seats.
MAINTENANCE
If seepage is noted at stem, tighten retaining nut per the following steps.
CAUTION: For maximum stem seal life, proper stem adjustment
procedure must be followed.
Excessive tightening causes higher torque and shorter stem seal life.
For CL51/52 valves only, immediately after the first frost is detected
around the stem, tighten the retaining or self-locking nut, as stated
below, to adjust the compression of the stem seals.
For Valves with Two Stem Nuts and a Lockwasher
(with or without handle):
Tighten retaining nut (lower nut) until Belleville washers are flat, the
nut will “bottom”.
Back off retaining nut
1
/
6
turn.
Tighten handle nut securely to lock retaining nut in place. (On some
automated valves, two retaining nuts are used with a lockwasher in
between. Hold the bottom nut securely with a wrench while tightening
the top nut to lock the two nuts in place.)
For Valves with Self-Locking Stem Nut (and four Belleville washers):
Tighten self-locking stem nut until Belleville washers are flat, the nut
will “bottom”.
Back off nut
1
/
3
turn.
CAUTION: The self-locking stem nut is difficult to tighten, and must
fully flatten Belleville washers before backing off.
REBUILDING
a
WARNING: BALL VALVES CAN TRAP PRESSURIZED FLUIDS IN
BALL CAVITY WHEN CLOSED
Special handling and cleaning procedures are necessary for oxygen
and vacuum service valves. Refer to industry practices when
overhauling these units
If the valve has been used to control hazardous media, it must be
decontaminated before disassembly. It is recommended that the
following steps are taken for safe removal and disassembly.
Relieve the line pressure. Operate the valve prior to attempting
removal from line.
Place valve in half-open position and flush the line to remove any
hazardous material from valve.
For CL51/52 valves, refer to Chlorine Institute Pamphlet 6 procedure
for flushing and drying, and for additional information on precautions
and cleaning.
All persons involved in the removal and disassembly of the valve
should wear the proper protective clothing such as face shield,
gloves, apron, etc.
A standard repair kit may be ordered for the valve. Specify the size,
series, material of seats and body seal and R# (revision number) of
valve or for non-standard valve, the “P”-Number, “T”-Number, “C”-
Number, or similar as found on nameplate. Some series, such as FZ,
S, AF, W, W2, and CL have their own repair kits, which are ordered by
the prefix. If valve body is stainless steel, place a “6” after valve size
in repair kit ordering code.
Examples:
Rev. #
Valve
Prefix
Series
or P, T, C,
Size
(if required)
RK
51
Material
etc. #
1"
AF
RK
51
RT
R3
3
/
4
" 6
RK
51
PM
R5
1
/
2
"
RK
51
RT
T0914
1
/
2
"
W
RK
52
XM
R3
Disassembly of Valve:
Remove valve from line. Unscrew end plug and set aside. If the body
seal was not removed with the end plug, remove it from the valve and
discard. Remove and discard the near seat and seat back seal (if any).
Place valve in closed position and remove the ball.
NOTE: If required, end plug disassembly tools are available from your
supplier or from Flowserve.