Troubleshooting apex 8000 positioner – Flowserve APEX 8000 High-Performance Positioner User Manual
Page 11
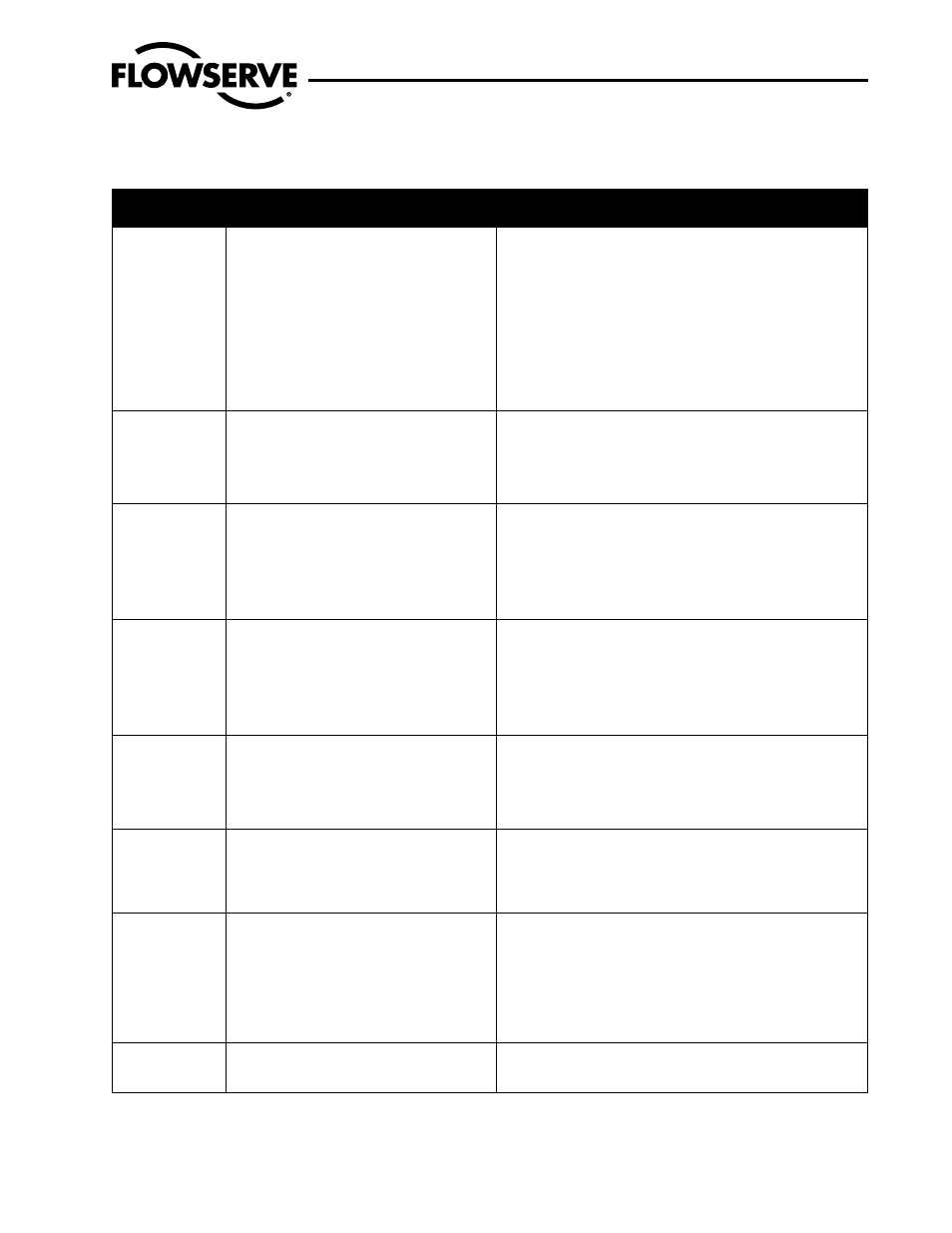
Troubleshooting APEX 8000 Positioner
Failure
Probable Cause
Corrective Action
Valve won’t
stroke, no
excessive air is
exhausting from
positioner
1. Tubing to wrong ports
2. Cam action reversed
3. Feedback lever arm is stuck
4. Low air supply
5. Relay tube stuck
6. Balance adjust screw not adjusted correctly
7. I/P module filter plugged
8. I/P module failure
9. I/P mounting bolts loose
10.I/P pressure signal blocked
1. Re-tube to correct ports (see “installation section).
2. Refer to “installation” section and reverse cam
3. Work with lever arm until it turns freely
4. Increase air supply to recommended value
5. Disassemble relay assembly and work relay tube free. Lightly
lubricate if necessary
6. Adjust balance pressure with adjusting screw
7. Remove I/P module and replace filter
8. Replace I/P module
9. Tighten mounting bolts
10. Remove I/P module and clear passageway; replace O-ring if
necessary
Valve won’t
stroke, excessive
air exhausting
from positioner
1.
A diaphragm in relay assembly burst
2. One of the poppets is stuck
3. Internal control valve problem
4. Damaged relay O-rings on relay tube
5. Blocked passageways in relay
1. Replace relay assembly or replace diaphragms
2. Remove relay assembly/poppet cover; free stuck poppet
3. Refer to instructions or check for actuator tubing leaks
4. Disassemble relay and replace O-rings
5. Disassemble relay and check small holes under diaphragms; clean
if clogged
Actuator goes
to full signal
position
regardless of
signal
1.
Broken feedback spring
2. Linkage is disconnected or stuck
3. Orifice is clogged by water, oil or dust in air
supply
4. Bent flapper, damaged nozzle
5. I/P module failure
6. Clogged orifice screen
1. Replace feedback spring
2. Check and tighten bolts/nuts in linkage. Make sure linkage does not
hang up; grease ping that rides in follower arm slot
3. Remove orifice screw and carefully clean orifice hole
4. Straighten flapper or replace damaged parts
5. Replace I/P module
6. Remove relay and clean ore replace orifice screen
Calibration
1. Loose positioner mounting
2. Loose linkage
3. Loose zero adjustment locking knobs
4. Wear of arms or pins
5. I/P mounting bolts loose
6. Stroke has change in valve
1. Remove cover and check three screws holding positioner to bracket;
check two bolts holding bracket to yoke
2. Tighten nuts and bolts on linkage and stem clamp
3. Tighten zero adjustment locking knob; re-calibrate if necessary
4. Replace worm arms, pins; grease appropriately
5. Tighten I/P mounting bolts
6. Refer to valve maintenance instructions
Excessive air
consumption
(other than
normal exhaust)
1. Air leakage from manifold rings between relay
and base
2. Air leakage from tubing
3. Leaky cylinder piston O-rings
4. Air leakage from relay
1. Tighten screws holding relay assembly together and/or replace
O-rings
2. Tighten or replace tubing fittings
3. Replace O-rings in cylinder
4. Disassemble relay and check and replace dynamic O-rings next to
tube if necessary
Actuator strokes
very slowly in one
direction only
1. Connection between signal capsule and flapper
misadjusted
2. Tubing to cylinder is restricted
3. Balance pressure low
1. Adjust gain according to Figure 6 or until actuator strokes
approximately equal speed in both directions. Verify alignment of
upper and lower gain plates. Make sure spacer nut is tightened.
2. Inspect tubing/fittings for restriction and replace if necessary
3. Adjust balance pressure according to page 5
Erratic operation
1. Dirt buildup on relay poppets or seats
2. Dirt buildup on relay tube
3. Clogged ports / passageways in relay
4. Faulty I/P module
5. Clogged orifice screw
6. Mechanical binding in linkage or internal
galling in valve
7. Clogged orifice screen
1. Disassemble; clean poppets and seats; add air filter or change filter
2. Disassemble; clean relay and lightly lubricate; replace O-rings if
necessary; add air filter or change filter
3. Disassemble, inspect and clean all ports and passageways
4. Replace the I/P module
5. Remove orifice screw and carefully clean orifice
6. Tighten linkage or refer to valve maintenance instructions
7. Remove relay and clean or replace orifice screen
Excessive
overshoot
1. Restricted air flow to positioner
2. Balance pressure not set correctly
3. Gain is set too high
1. Adjust air supply as needed
2. Adjust balance pressure according to page 5
3. Lower gain mechanism until overshoot is minimized
Apex 8000 High-Performance Positioner AXENIM0130-06 11/10
11