Principles of operation, Operation – Flowserve APEX 8000 High-Performance Positioner User Manual
Page 2
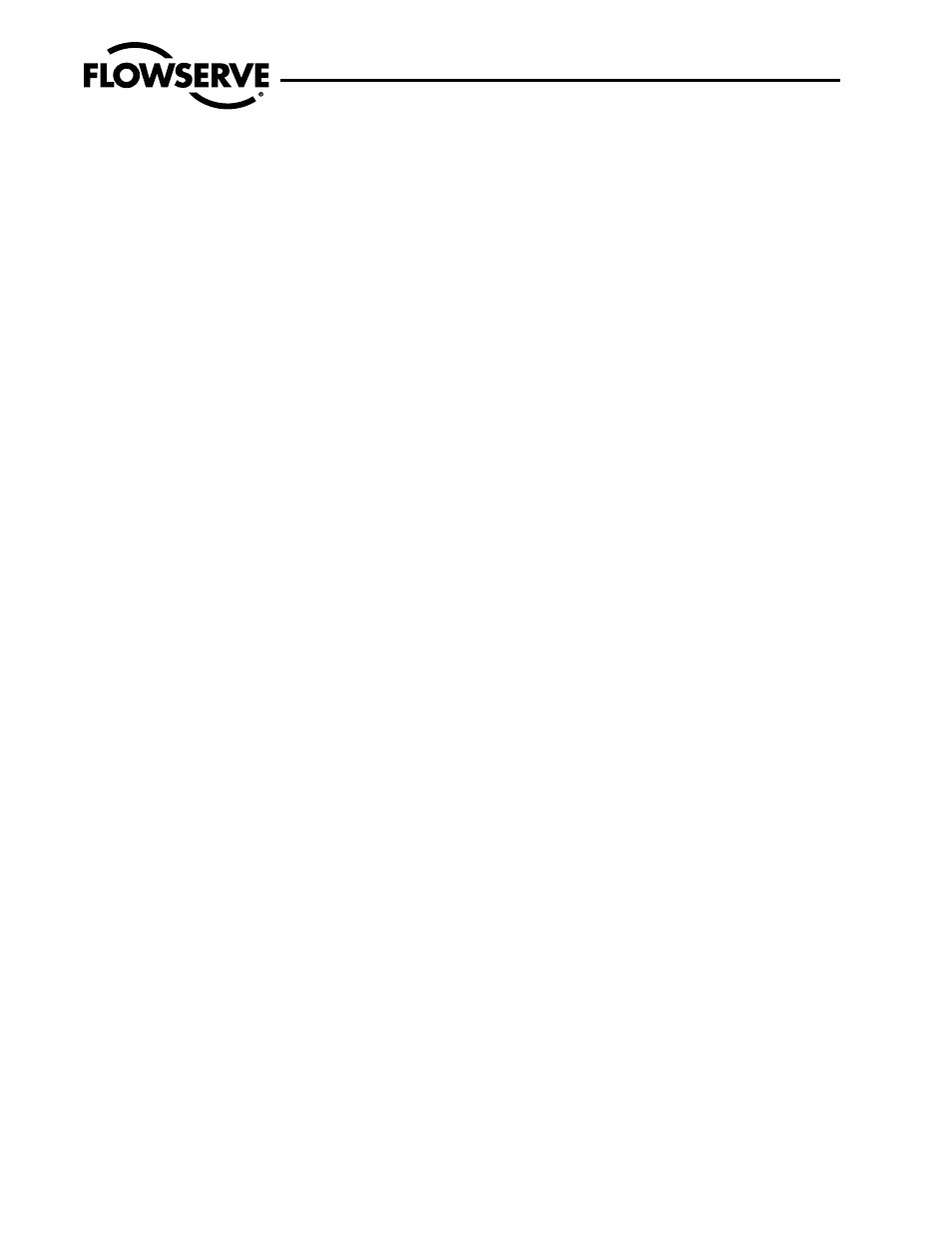
Principles of Operation
This bulletin is designed to assist in installing, calibrating, troubleshooting and performing maintenance as required for the APEX 8000 Series
high-performance positioner.
Product users and maintenance personnel should thoroughly read and strictly follow the instructions contained in this bulletin
prior to operating the positioner. Any questions concerning this product should be directed to a Flowserve representative
To avoid possible injury to personnel or damage to valve parts, WARNING and CAUTION notes must be strictly followed.
Modifying this product, substituting non-factory parts or using maintenance procedures other than outlined could drasti-
cally affect performance and be hazardous to personnel and equipment.
The APEX 8000 high-performance positioner is a two-stage device and is designed for use in control loops where fast response
is required. The APEX 8000 positioner is designed to be modular and use the P/P module for 3-15 psi input signal or the NT
3000 Series Transducer Module for 4-20 mA input signal.
The APEX 8000 high-performance positioner is designed as a four-way device, but can easily be converted to a three-way device
by plugging one of the output ports.
NOTE: The APEX 8000 high-performance positioner must use the I/P NT 3000 Transducer. The I/P 2000 Transducer is not ac-
ceptable for use with the APEX 8000 Series Positioner.
The APEX 8000 positioner can handle supply pressures up to 150 psi; thus, a supply regulator is usually not required. However,
a five micron air filter is required for pneumatic positioners and a coalescing filter is required for I/P positioners.
NOTE: The air supply should conform to ISA Standard S7.3 (a dew point at least 18° F / -8° C below ambient temperature,
particle size below 5 microns, oil content not to exceed one part per million).
The APEX 8000 Series positioner features an adjustable gain of 400-1100:1. The medium gain setting is standard for smaller
actuators, while the high gain setting is used on larger actuators (refer to ‘Gain Adjustment Procedure’ section for further
details.)
Operation
The positioner schematic (Figure 1) shows an APEX 8000 Series positioner connected for double-acting service on a rotary
rack-and-pinion actuator. Tension on the feedback spring provides feedback to the positioner, which varies as the stem position
changes. The spring-loading force is applied through the feed-back linkage and cam to the positioner’s input capsule.
Instrument signal pressure is applied between the diaphragms in the input capsule. Therefore, the input capsule serves as a
force-balance member, matching the valve stem position (as measured by tension on the feedback spring) to the instrument
signal.
When the opposing forces balance exactly, the system will be in equilibrium and the stem will be in the exact position called for
by the instrument signal. If the opposing forces are not in balance, the input capsule will move up or down and, by means of
the pilot-valves, will change the output pressures, moving the stem until the tension on the feedback spring exactly opposes the
instrument signal pressure.
2
Apex 8000 High-Performance Positioner AXENIM0130-06 11/10