Flowserve Apex 5000 Positioner User Manual
Page 2
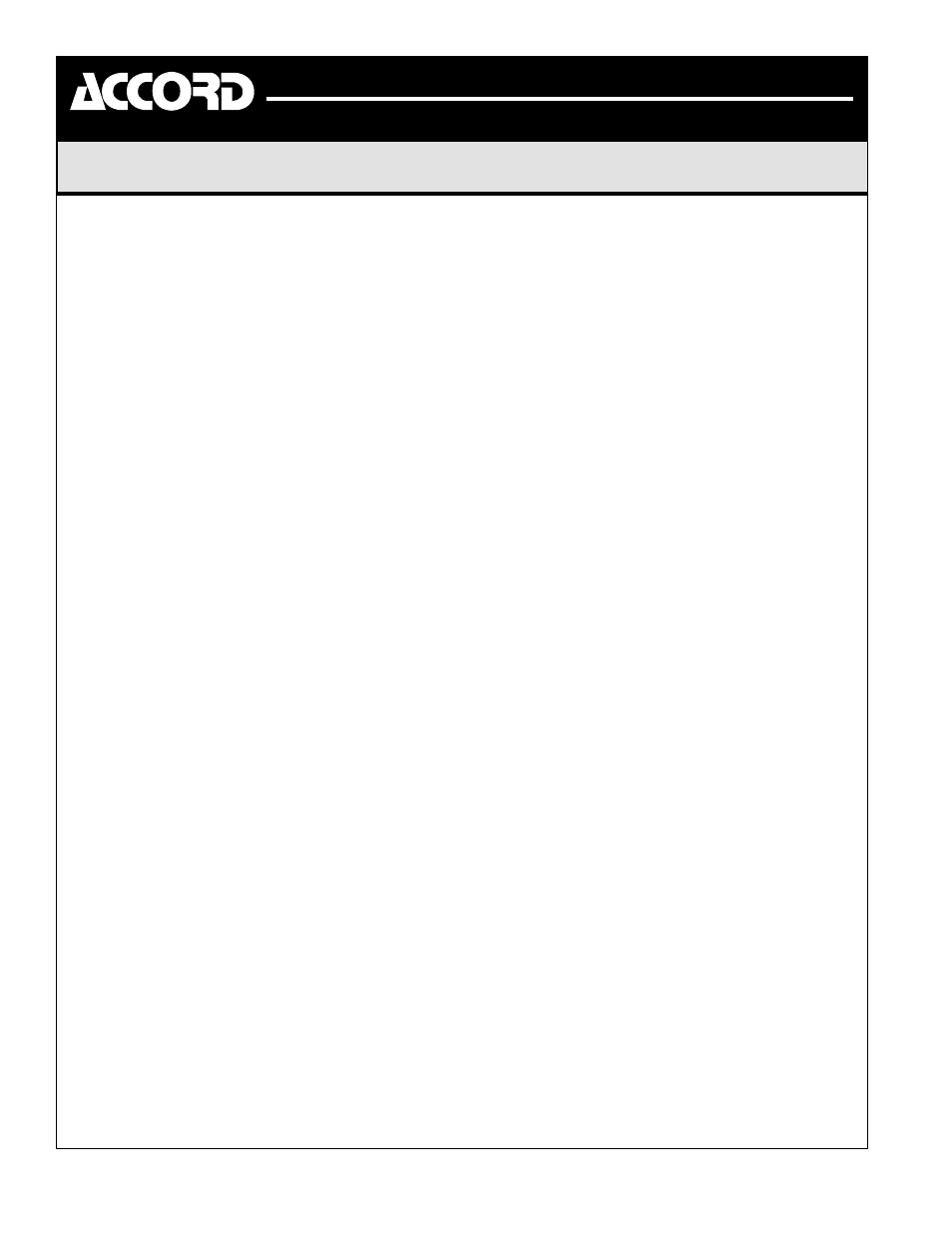
© 2011, Flowserve Corporation, Provo, UT
B00062a4 (AC-53 MFG) 03/11
Apex 5000 Positioner
Installation, Operation and Maintenance Instructions
CONTROLS
Accord Controls
765 South 100 East
Phone: 801 373 4576
A Unit of Flowserve Corporation
Provo, Utah 84606-6160
Facsimile: 801 489 2591
www.accord-controls.com
Cam Installation:
Introduction:
The standard cam features linear, 90 degree
operation for full 3-15 psi input, 3-9 and 9-15 psi split
ranges, and 3-15 psi 180 degree operation. The factory
setting is 3-15 psi, 90 degrees, with “D” (direct) side up for
full clockwise position at 3 psi.
Caution:
Be sure supply air pressure is removed and no
pressure exists in actuator before adjusting cam.
Cam Removal:
With a wrench on the output shaft
(if necessary), loosen and remove the jam nut. Remove
pressure from feedback arm by pushing it away from cam.
Remove cam.
Cam Installation:
1. Be sure shaft is properly aligned with coupler
or actuator.
2. Push feedback arm away from shaft to avoid pressure
on cam.
3. Place cam over shaft. Make sure “D” is showing for
direct acting or “R” is showing for reverse acting.
4. Align hole at start of desired range with bearing.
5. Tighten jam nut making sure cam does not rotate. Use
a flat-bladed screwdriver to prevent cam rotation.
Calibration:
Caution:
Cam pinch points may injure fingers. Be sure to
avoid placing fingers and other objects in cam pinch points.
Also avoid touching balance beam and spool while making
adjustments as unpredictable cam rotation may result.
Finally, maintain control of input signal while making
adjustments.
1. Start with cover removed, supply air connected, and a
3 psi (4 mA) input signal.
2. Loosen jam nut on zero adjust screw.
3. Turn zero adjust screw to rotate actuator/valve to
desired start or fail position. “Loosening” screw moves
actuator/valve away from start or fail position towards
end position.
4. Change input signal to 15 psi (20 mA).
5. Loosen span adjust lockscrew (larger screw on span
adjust assembly).
6. Turn span adjust pinion to rotate actuator/valve to
desired end position. Counterclockwise rotation moves
slide towards cam which moves actuator/valve
towards start or fail position. Retighten lockscrew to
lock setting.
7. Repeat steps 3 through 7 as necessary. Note:
The
Apex 5000 positioner is designed so that span
adjustment does not affect zero setting. However, zero
setting may be affected slightly because of
manufacturing tolerances and/or zero setting itself.
8. While holding zero knob to prevent rotation, tighten
jam nut to lock setting.
9. Replace cover.
Gain Adjustment:
Introduction:
The Apex 5000 positioner features an
adjustable gain. This feature can be used to tune positioner
performance to specific applications. The adjustment
primarily affects sensitivity, but also may affect overshoot
and speed (to a minor extent). For most applications,
especially medium and large-sized actuators on valves with
resistive closure members (ball and plug valves), the
factory setting of maximum gain should be used for
maximum sensitivity and quick response. For smaller
actuators or actuators on low resistance closure members
(butterfly valves and dampers) lower gain may improve
performance by reducing overshoot. This also tends to
reduce sensitivity. On applications using the low flow spool
valve, the maximum gain setting is suggested.
1. Remove cover and loosen gain adjust lockscrew.
2. Move gain adjust assembly by holding the tab and
pushing towards balance beam (to decrease gain) or
away from balance beam (to increase gain). The
triangle adjacent to adjustment assembly indicates
effective ends of adjustment travel when lined up with
fillet closest to tab.
3. Tighten lockscrew to lock setting and replace cover.
4. Important:
Check positioner calibration after making
gain adjustments.
Page 2 of 8