Batteries, Maintenance and troubleshooting, Worcester actuation systems – Flowserve F75 Series Fail-Safe Module User Manual
Page 4
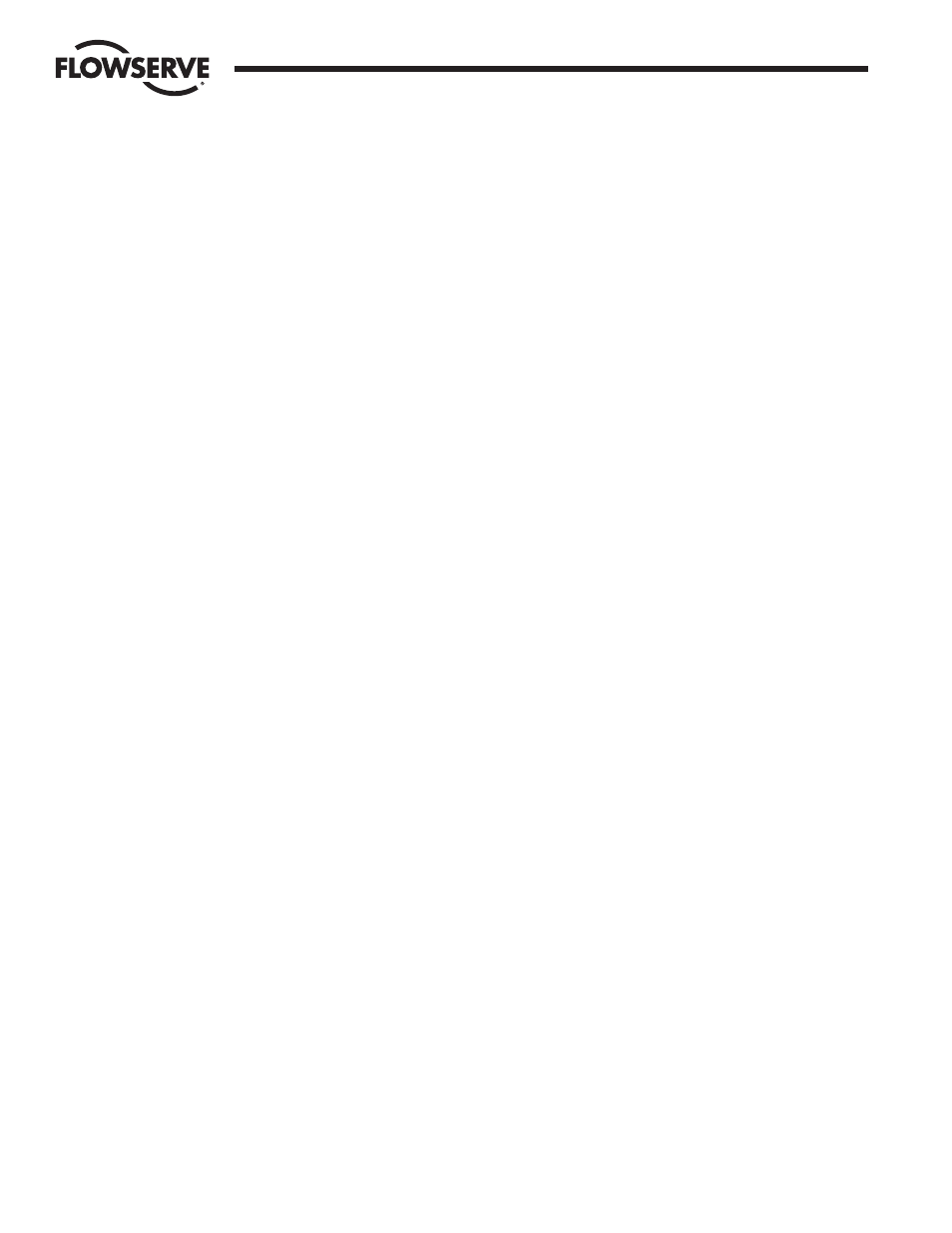
4
Series F75 Fail-Safe Module
WCAIM2029
6. BATTERIES
6.1 To obtain optimum shelf life, batteries should be stored in a cool
area; if possible, store batteries between 40° to 65°F. Never store
batteries at temperature over 100°F.
Each battery is to be inspected for a date code on the top of the
battery between its terminals. Within 6 months of this date, the
battery should be charged, and every 6 months of storage
thereafter, and before placing the batteries into service. They must
be inspected to make sure rough handling has not damaged the
battery. If damaged, there is a possibility of loss of sulfuric acid
electrolytes and possible corrosion of adjacent components.
Sulfuric acid can cause severe burns to skin and eyes. If a battery
is damaged, the battery cannot be used and must be discarded.
Be careful in handling and disposing of any damaged batteries.
If any skin contact is made with a damaged battery, immediately
flush the contacted skin with water for at least five minutes.
The batteries are “carefree”; they cannot spill, never require
maintenance, have dual covers, and are completely rechargeable.
For maximum protection from high temperatures, it is
recommended that the ambient where the fail-safe module is used
should be between 65° and 100°F.
6.2 Alternative Power Supply
Large external lead-acid batteries may be used as a non-
interruptible 24 VDC supply. If this is done, internal batteries
should be disconnected from terminals 6 and 7, removed from
module, and properly stored. External DC power supply should
then be connected to terminals 6 and 7.
7. MAINTENANCE AND
TROUBLESHOOTING
7.1 The Series F75 module requires no regular maintenance other
than checking and eventually replacing batteries as described in
paragraph 2.3.6, 7 and 8.
For maintenance, troubleshooting and other information on the
Series 75 actuator itself refer to IOM for Series 75 Electric Valve
Actuators.
7.2 If it becomes necessary to replace the fail-safe circuit board, the
replacement board may need to be calibrated to achieve the
required voltage. If so, use the following procedures (reference
wiring diagram in Figure 1 on page 1 of this manual or wiring
label inside of 75 actuator cover):
7.2.1 Across
terminals 6 and 7, connect a
1
/
4
watt, 2K resistor.
Connect Series F75 module to AC power as required —
120 VAC or 240 VAC. Measure amperage through resistor
and voltage across it. Adjust R7 on circuit board to achieve
a voltage of 27–27.5 VDC, at about 13 mA current.
7.2.2 Disconnect AC power. Remove the 2K resistor. Connect a
470 ohm, 3 watt resistor across terminals 6 and 7. Again
apply AC power. Measure voltage across resistor. Voltage
should be about 26.5 to 27 VDC. Adjust R8 so that green
status light on front cover goes out and yellow status light
on cover goes on.
7.2.3
Again, disconnect AC power. Remove the 470 ohm
resistor at terminals 6 and 7 and replace with a 10 watt,
68 ohm resistor. Reapply AC power and measure voltage
across resistor. Voltage should be a 21 to 21.5 VDC.
Adjust R9 so that red status light on cover goes on and
yellow status light on cover goes out.
The battery charger and indicator status light circuit has
been calibrated.
To verify, connect the load again across 6 and 7 and
slowly decrease resistance while measuring voltage to
verify the voltages at which the indicator light switch goes
on and off while decreasing and increasing the loads. (The
voltage at which light goes on and off will be slightly
different).
Flow Control Division
Worcester Actuation Systems