Adjustment of positioner/controller board, Calibration, Worcester controls – Flowserve 90 Series Controller User Manual
Page 6
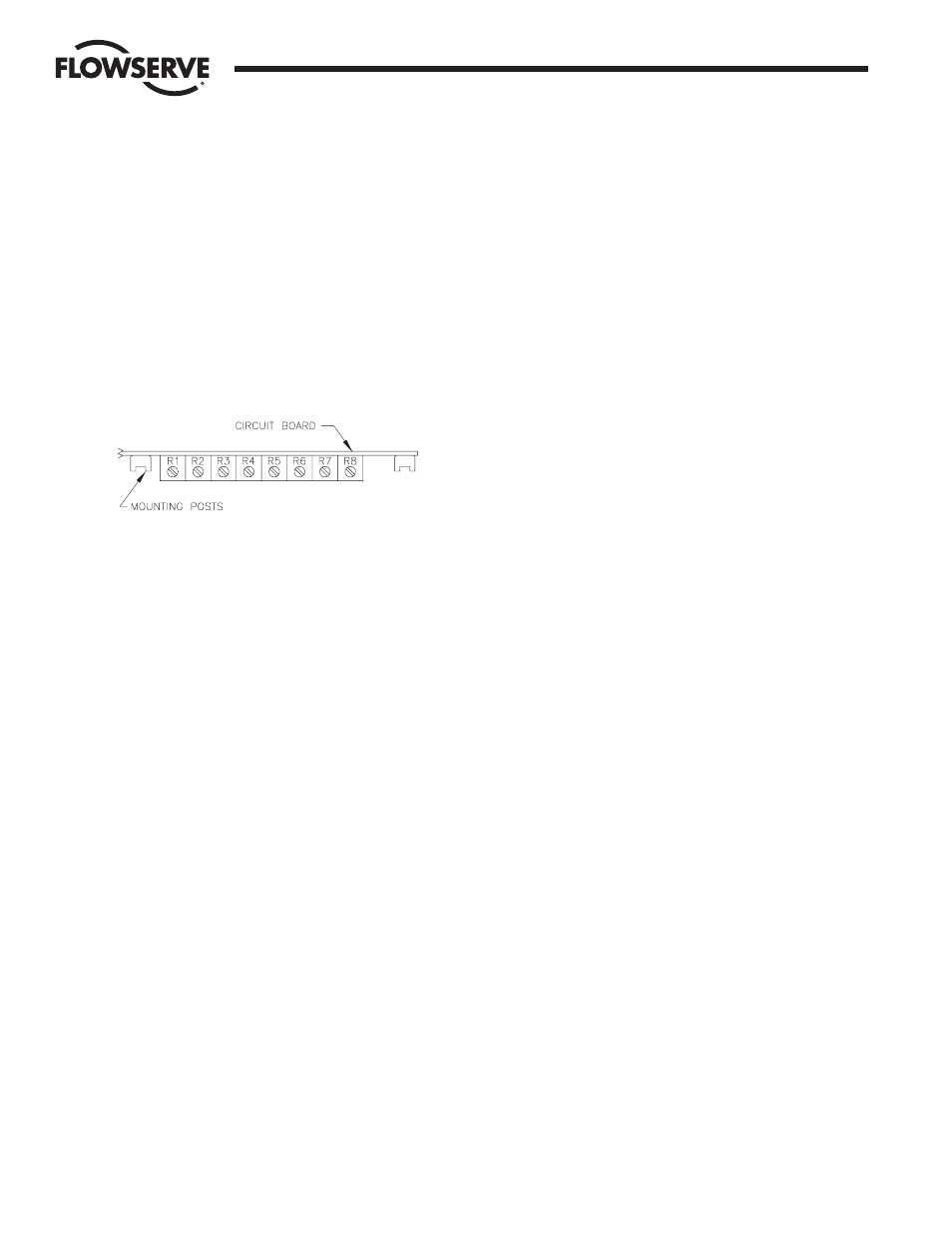
6
Positioner/Controller for Series 90 Modular Accessory System
WCAIM2045
7.ADJUSTMENT OF
POSITIONER/CONTROLLER BOARD
a. Preliminary Adjustments
Before starting the calibration and adjustment procedure, set the
circuit board trimpots as follows:
R1 –
20 mA
trimpot – Mid-travel
R2 –
4 mA
trimpot – Mid-travel
R3 –
ZERO
trimpot – Mid-travel
R4 –
SPAN
trimpot – Mid-travel
R5 –
GATE
trimpot – Mid-travel
R6 –
NULL
trimpot – Mid-travel
R7 –
ON
trimpot – Counterclockwise
R8 –
OFF
trimpot – Counterclockwise
b. Control Description
1. “20 mA” trimpot – Potentiometer R1 is used for 4-20 mA
output indication only. It calibrates the indicator to obtain
proper 4-20 mA output. It does not affect calibration of
positioner/controller.
2. “4 mA” trimpot – Potentiometer R2 is used for 4-20 mA
output indication only. It calibrates the indicator to obtain
proper 4-20 mA output. It does not affect calibration of
positioner/controller.
3. “ZERO” trimpot – Potentiometer R3 adjusts the positioner/
controller circuit board to match the minimum value of the input
signal. Adjustment range is approximately 2 to 10 mA.
4. “SPAN” trimpot – Potentiometer R4 adjusts the
positioner/controller circuit board to match the maximum
value of the input signal. Adjustment range is approximately
14 to 23 mA.
5. “GATE” trimpot – Potentiometer R5 adjusts the maximum value
for the input signal vs. feedback/setpoint signal differential,
above which the solenoid drive signal changes from pulsing to
continuous. Essentially, there are two monitoring points or
gates, one above and one below the desired position, with
amount above and below determined by the setting of the
“gate” control. Adjustable from approximately 5 to 15% plus or
minus the feedback/set-point signal.
6. “NULL” trimpot – Potentiometer R6 adjusts the width of the
circuit board’s null point, the point at which the input signal is
considered equal to the feedback/set-point signal and actuator
motion is terminated. The null width is adjustable from
approximately 0.5 to 4.0% of the full range of the input signal.
It permits adjustment of sensitivity so that minor variations in
the signal level such as noise, hum, etc. can be ignored.
7. “ON” trimpot – Potentiometer R7 adjusts the length of the
pulse delivered to the solenoid, which determines how much
the actuator will open or close for each pulse.
8. “OFF” trimpot – Potentiometer R8 adjusts the length of time
between pulses during which the controller logic waits to see
if the media change, caused by the previous pulse, was
sufficient to correct any input signal/feedback difference
before generating additional pulses.
c. Reverse-Acting
The usual mode of operation for the positioner/controller board is
to open on increasing signal when set up as a positioner and to
close on increasing signal when set up as a controller. For use
with certain types of applications, however, it may be desirable to
operate in the opposite mode. For some valves this can be
accomplished by cross-line mounting the actuator on the valve.
No wiring changes are necessary when this method is used. If
cross-line mounting is not feasible, the reversal can be
accomplished electrically on the printed circuit board and at the
terminal strip. On the circuit board it is necessary to reverse the
“R” and “D” jumpers. In other words, if the two “R” jumpers are
installed, remove them and install the two “D” jumpers and vice
versa. The positioner configuration would normally have the two
“D” jumpers installed and the controller configuration would
normally have the two “R” jumpers installed.
At the terminal strip (for reverse operation) it is also necessary to
reverse the green and purple wires on terminals 6 and 8 which go
to the circuit board. Put the green wire where the purple wire was
and put the purple wire where the green wire was. The positioner
configuration would normally be set up with the green wire from
the circuit board connected to terminal 8 and the purple wire from
the circuit board connected to terminal 6. The controller
configuration would be just the opposite. With the controller
configuration only, there may be some instances where the proper
control response would not be achieved if the green and purple
wires are reversed. In this case leave them as they were originally.
An example of such an instance would be where a valve is
mounted in a bypass line around a pump with a pressure
transmitter located in the main header and the set-point
potentiometer has a calibrated dial that indicates pressure
increasing as the knob is rotated clockwise. This means that in
order to increase header pressure, flow must be restricted in the
bypass line and the actuator must drive the valve in the closed
direction until the desired header pressure is achieved.
8.CALIBRATION
a. Input Signal
The milliamp input is normally calibrated so that in the positioner
configuration 4 mA equals full closed and 20 mA equals full open.
In the case of the controller configuration 4 mA would equal a 0%
setpoint potentiometer setting and 20 mA would equal a 100%
setpoint potentiometer setting.
For the controller, the output signal of the process transmitter
should be calibrated such that the minimum controllable point of
the parameter the sensor is measuring should equal 4 to 4.5 mA,
and the maximum controllable point of the same parameter
Flow Control Division
Worcester Controls