Final adjustment of positioner/controller, Worcester controls – Flowserve 90 Series Controller User Manual
Page 7
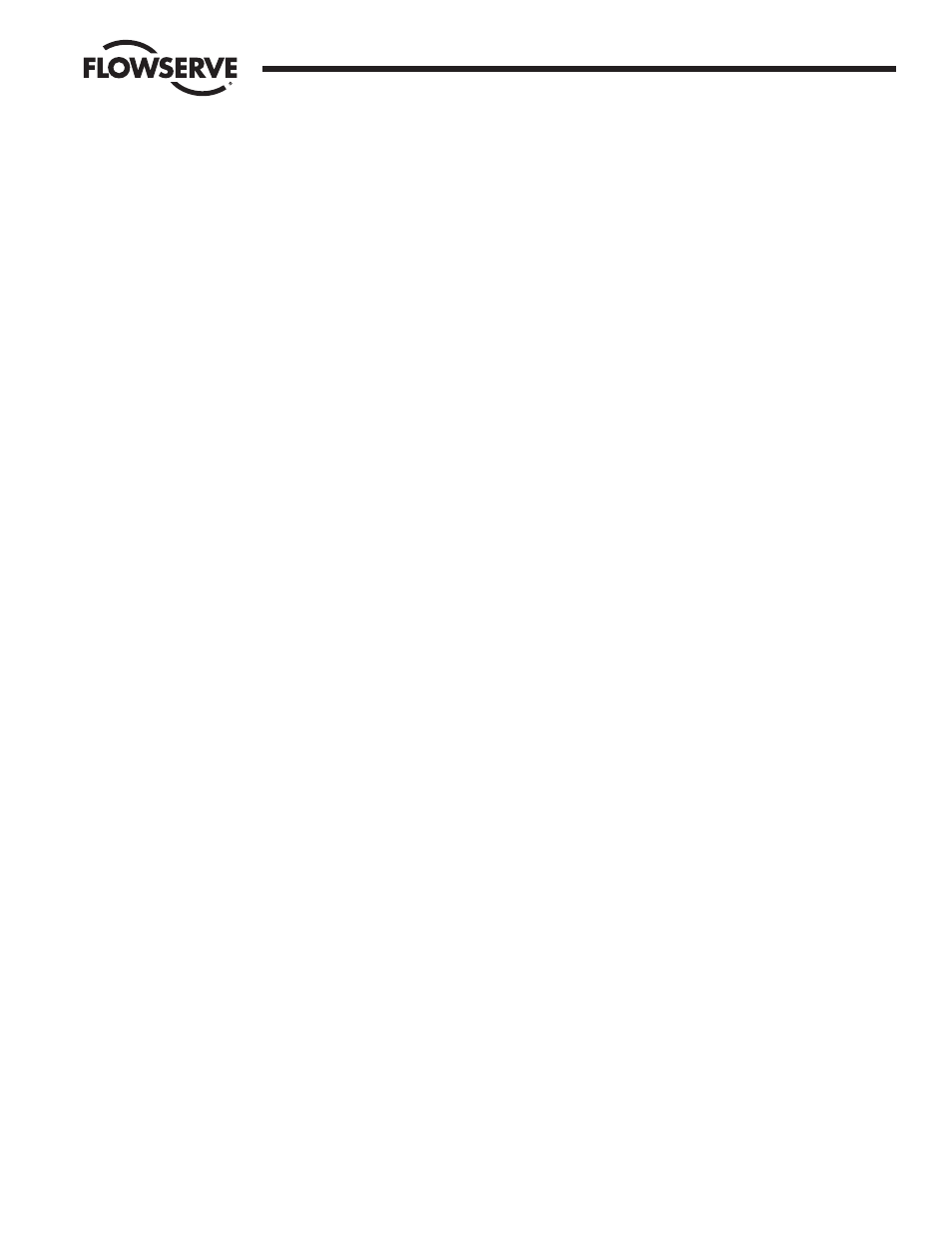
WCAIM2045
Positioner/Controller for Series 90 Modular Accessory System
7
should equal 19.5 to 20 mA. For example, a loop controlling flow
has a maximum flow rate of 600 gallons per hour (gph), and the
range of control desired is between a minimum of 150 gph and a
maximum of 450 gph. The flow transmitter should be calibrated
so that the 150 gph flow rate generates a 4 mA signal and the 450
gph flow rate generates a 20 mA signal. Alternately, the
transmitter could be calibrated to output 4 mA for zero gph and
20 mA for 600 gph. This would compress the operable range of
the setpoint control into 50% of its normal full scale (for this
example), but should give acceptable operation for most
applications. If large and/or long-term deviations are being
controlled, the controller can cause the valve to be driven to the
full-open or closed limits of its travel. In order to minimize this
effect, turn the “gate” trimpot (R5) to its full counterclockwise
position, the “off” trimpot (R8) to its full clockwise position, and
the “on” trimpot (R7) to its full counterclockwise position. It may
then be necessary to adjust the “on” trimpot in the clockwise
direction to get the “on” pulse sufficiently long to move the valve.
b. Input Calibration – Positioner
Prior to calibrating the positioner board, the feedback
potentiometer should be checked for correct calibration—if this
has not already been done. See paragraph 6.c.7 for the correct
procedure. Output the minimum position signal (normally 4 mA)
with the actuator in the fully-closed position. Adjust the “ZERO”
trimpot (R3) so that LED “LD2” remains lit. Now increase the
position signal to maximum (normally 20 mA) with the actuator in
the fully open position (use air if necessary). Adjust the “SPAN”
trimpot (R4) so that LED “LD2” remains lit. Repeat the above two
steps two or three times to fine tune the adjustments.
c. Input Calibration – Controller
Input the minimum signal from the transmitter and turn the
setpoint potentiometer to 0%. Adjust the “ZERO” trimpot (R3) so
that LED “LD2” remains lit. Disregard valve position during these
adjustments. Input the maximum signal from the transmitter and
turn the setpoint potentiometer to 100%. Adjust the “SPAN”
trimpot (R4) so that LED “LD2” remains lit. Repeat the above two
steps two or three times to fine tune the adjustments.
9.FINAL ADJUSTMENT OF
POSITIONER/CONTROLLER
a. Positioner
The final adjustment of the positioner configuration of the circuit
board is straightforward. Because air is compressible, the “gate”
or window trimpot should be adjusted sufficiently wide to
minimize the possibility of overshooting. The optimum adjustment
is to have the actuator pulse from one to three times to reach final
position. It will probably be necessary to adjust the “on” (R7) and
“off” (R8) trimpots to give the actuator a chance to stabilize its
position after a motion pulse. The “on” pulse time must be long
enough to create a sufficient differential pressure across the
actuator pistons to overcome valve rotational torque, and the “off”
time long enough for the actuator to settle into position. The
“null” trimpot (R6) can normally be left at its mid-travel position.
Turning it clockwise will increase the circuit’s sensitivity to signal
change but at the same time it will make the circuit more
susceptible to electrical noise if it is present. Turning this trimpot
counterclockwise will have the opposite effect.
b. Controller
The primary objective in tuning the controller to the process loop
is to match the basic or pulsed operation of the controller to the
median dynamics of the loop. This is accomplished by adjusting
the length of the “on” pulse to move the valve sufficiently to
compensate for approximately 60% of the average median level
input signal variation. Next, adjust the “off” time between pulses to
approximately 50% of the loop transmit time (the time it takes for
the process transmitter to respond to a change in valve position).
For example, if it takes two seconds for a valve position change to
start affecting the loop process sensor, adjust the wait period
duration to approximately one second. Adjusted this way, the
average media variation will be compensated for in two to three
pulse periods, while the smaller variations can be compensated
for in one to two pulse periods. This minimizes the chances of
overshooting while at the same time providing a relatively quick
response to average variations.
Large variations and those variations whose rate of change
exceeds the pulsed response capability of the controller will
eventually exceed the speed gate setting, causing the actuator to
operate at its normal non-pulsed speed. The actuator will move
continuously in the corrective direction until stopped either by the
proper process condition appearing at the sensor pickup point, or
the actuator reaching its end of travel, whichever occurs first.
If the actuator has reached one of its limits, it will stay there until
the process condition at the sensor crosses the setpoint, at
which time the actuator will start pulsing back to what will
eventually be a new valve position, which compensates for the
original process variation.
If the average loop variation is only a few percent of the full range
of sensor input signal, a short duration pulse and a tight speed
“gate” adjustment would, in most cases, provide the best control
action. If the average variations are large, that is 10% or greater of
the full range of the sensor signal, longer pulse durations and
wider speed “gate” settings should provide the best control action.
Compensating for the majority of loop process variations with the
controller staying in the pulse mode of operation means the
controller is optimally adjusted and maintaining the loop at or
close to the setpoint. However, because of the compressibility of
air in the actuator, it may be necessary to experiment with the
adjustments to achieve the optimum response of the controller,
for basically the same reasons as presented in section 9.a.
c. Throttle Valves
The M.A.S. package, when configured as a positioner or controller,
is provided with air throttle valves that are used to control actuator
speed. (These are shipped from factory fully open). In many
instances an actuator/valve combination is capable of moving
much faster than desired for good process control. The throttle
valve(s) in conjunction with the positioner/controller trimpot
adjustments provide great latitude in actuator response time.
Flow Control Division
Worcester Controls