Rebuilding instructions, Actuator disassembly, Worcester controls – Flowserve 10 ACCESS I 39 Actuators User Manual
Page 11
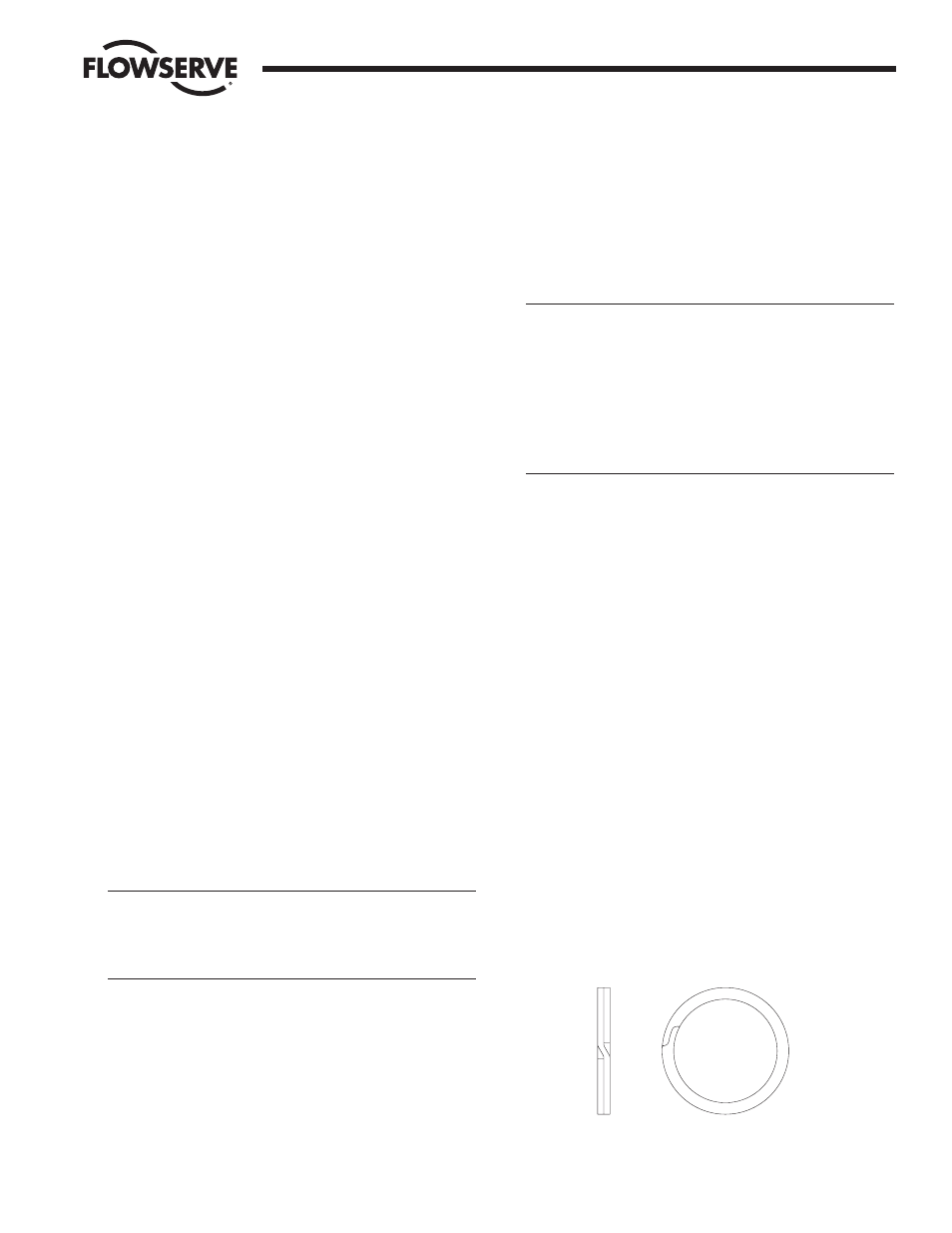
WCAIM2027
10, 15, 20 ACCESS I 39 Actuators
11
a) If actuator has no lubrication, apply generous
amount of a #1 grease.
b) If solidified grease between the pinion and the
piston racks is present, clean, dry, regrease and
reassemble.
3. Verify that actuator pinion shaft and/or pistons are
not bound. If bound, reassemble per Rebuilding
Instructions.
4. If unit exhibits excessive amounts of backlash, check
teeth on piston racks for wear. If worn, replace
piston assemblies.
5. In spring-return actuators, check for misplaced or
broken springs. If springs are broken, check body
bore for scoring.
a) If springs are broken, replace springs. SPRINGS
SHOULD ALWAYS BE REPLACED IN COMPLETE
SETS.
b) If body bore is scored, replace it. Also, replace
piston O-rings contained in repair kit.
6. If actuator is free, valve is free and control block, if
used, is shifting air properly, reassemble the
actuator and retest. If unit still fails to operate,
consult Flowserve.
REBUILDING INSTRUCTIONS
NOTE: For identification of all numbered parts discussed below,
consult exploded view of actuator.
After actuator has been repaired, mark rebuild label accordingly and
apply to actuator.
ACTUATOR DISASSEMBLY
1. Disconnect the air supply and electrical service to the actuator.
2. Remove the actuator and its mounting bracket from the valve. See
Caution note below.
CAUTION: Ball valves can trap pressurized media in the cavity.
Isolate the piping system in which the actuator/valve assembly
is mounted and relieve any pressure on the valve. For all the
valves listed in Installation Section D, the actuator bracket can
be removed without loosening or removing any valve body bolts.
3. Remove the actuator bracket from the actuator to begin repair.
Note mounting of removed bracket for easy reassembly.
4. It is not necessary to remove the control block (7A) or air
connection block (7B) to rebuild actuator. However, if it becomes
necessary to remove the block, begin by removing the block bolts
(7D). Use care to retain the block gasket (9A, 9B or 9C).
NOTE: If block gasket removed, with or without small black block
plug, differs from those illustrated in this IOM, replace with new
style or note orientation for proper reassembly.
5. Each end cap (5A and 5B) is aligned onto the body (1) over a
“fool-proof pin”. This ensures that the end caps can only be
assembled to their respective end of the actuator. Remove all four
metric screws (5C) from and remove both end caps. Remove the
two bearings (6A) and O-rings (15A and 15B) from each end cap.
CAUTION: If the actuator is a spring-return model, first remove
two end cap screws diagonally opposite each other, then
lubricate the threads and under the head. Replace the screws
and repeat procedure for the other two screws. Do this for each
end cap, as this will aid reassembly. Now uniformly loosen all
four end cap screws on each end cap two to three turns at a
time, in sequence, to relieve pre-load of the springs. On larger
actuators with springs use caution when removing end caps.
End cap screws are long enough to allow springs to relieve
before disengaging.
After the screws are removed, gently pry off each end cap, being
careful not to damage the end cap O-rings.
6. The two piston guide rod (4) assemblies can now be removed
from each end of the body and disassembled by removing the
piston set screws (12). Do not interchange piston guide rods (4)
and their respective piston (3). For Rev. R6 actuators, each guide
rod and piston may be press fitted together (do not use set
screws) and cannot be disassembled. (To assist reassembly, mark
the body with a line on the side from which the guide rod using
the through-hole is removed). Remove all O-rings (15B) and
(15C) and bearings (6B) from pistons (3).
7. The shaft (2) can only be removed after piston assemblies are
taken out. Remove the position indicator (17), if any, the shaft clip
(15F), not a reusable part! (see note below) and the stainless steel
washer from the top of shaft. Then remove the shaft through the
larger opening in the bottom of the body. The top bearing (15G) and
the O-ring (15D) can now be removed. Remove the two stainless
steel washers and throughst bearing (10) from the top of the shaft
and the O-ring (15E) and bearing (15H) from the bottom end.
NOTE: Some actuators may be using a spiral ring type shaft clip as
shown below. To remove this clip, engage the lower end of the
ring with a flat blade screwdriver. Using another flat blade
screwdriver push the top end of the clip in the opposite direction.
As the clip I.D. expands lift the clip from the shaft. The installation
of a new clip would be the above steps in reverse and ensuring
that the edges of the clip are properly seated in the shaft groove.
Flow Control Division
Worcester Controls