C. maintenance, D. rebuilding, E. recommended spare parts: rebuilding kits – Flowserve 34 Series Pneumatic Actuator User Manual
Page 3: Worcester controls
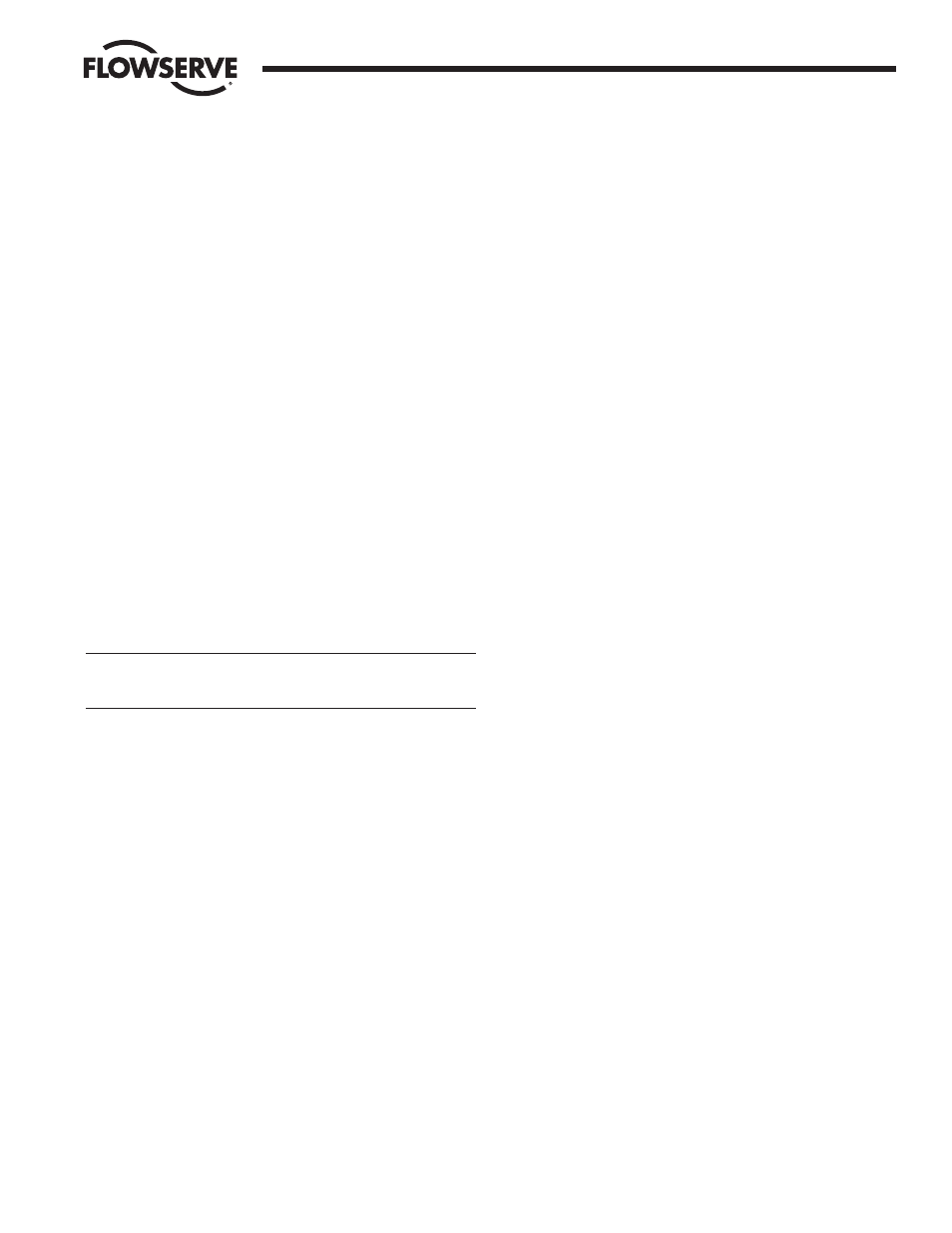
08932-F
Series 34 Pneumatic Actuator
3
C. MAINTENANCE
1. During operation, the only maintenance required is periodic
inspection of all fittings and fasteners for tightness.
2. If the unit fails to function, use the following checklist.
a. Check assembly in line:
1. Adequate air pressure? (60 to 125 psi) (80 TO 125 psi on
spring-return.)
2. Adequate volume? (
1
/
4
" tubing minimum for supply.)
3. Speed control screws backed off?
4. Electricity? (Adequate voltage.)
5. Solenoid operational? (Listen for a clicking sound.)
6. Valve operative? (Manually)
7. Actuator operative? (Manually)
b. When de-energized:
If exhausting continuously from solenoid port, replace piston
or solenoid.
If exhausting continuously from block port, replace spool
cartridge in block.
D. REBUILDING
CAUTION: If shaft retaining clip is not properly seated, the shaft
may blowout under pressure. The clip should be solidly in its
groove with the stamped numbers exposed.
Following replacement of any parts, reassembly is essentially the
reverse order of the following instructions. Please note that the
instructions are separated into the various subassemblies should the
disassembly involve only one part of the entire actuator.
When reassembling actuator, grease pins, links, shaft, and piston with
a lubricant appropriate for the temperature of the service. Petroleum
jelly is suitable for most applications.
Prior to beginning disassembly, disconnect air and electrical
connections and remove actuator from valve.
1. Solenoid Valve Block and Associated Parts
a. Unscrew solenoid assembly from valve block by turning
counterclockwise. Remove O-ring from solenoid cavity in
valve block.
b. Remove tubing assembly (if any) by loosening fittings.
Remove valve block from housing by removing the two
mounting screws.
c. If spool cartridge must be removed from the block, remove
snap ring first (snap ring must be replaced with stamped
numbers visible, solidly seated in its groove), then the
cartridge itself, noting its position, and exercising care in not
damaging O-rings. Care must be taken in reinserting into the
valve block to avoid damage to O-rings. Cartridges are not
used on spring-return units.
2. Cylinder
Using a strap wrench, turn cylinder counterclockwise until locking
wire (which will protrude through side) can be removed. Pull
cylinder from the housing.
3. Housing and Linkage
a. Remove retaining ring and washer from top of shaft.
b. Deburr shaft and remove by pressing down through housing.
c. Remove piston links, pins and lever by pulling piston away
from housing.
d. Links may now be lifted off pins and piston may be removed.
4. To disassemble a spring-return actuator follow instructions as in
Steps 1, 2 and 3 above plus:
a. Remove snap ring clip and end plate from rear of cylinder
assembly and remove spring assembly.
b. Remove spring compression bolt from inside of flange at rear
of spring assembly.
E. RECOMMENDED SPARE PARTS:
REBUILDING KITS
1. The spare parts recommended for the Series 34 Actuators are
contained in pre-packaged kits which are available through your
Worcester Controls Distributor. When ordering repair kits, give
actuator size, style and revision number.
Example: ARK34SN R1
When ordering parts, specify size and model of actuator and
revision number and use the standard nomenclature shown on
the accompanying exploded drawings.
Example: B34N R1 Link
Flow Control Division
Worcester Controls