Kemppi TTC-TIG torches User Manual
Page 11
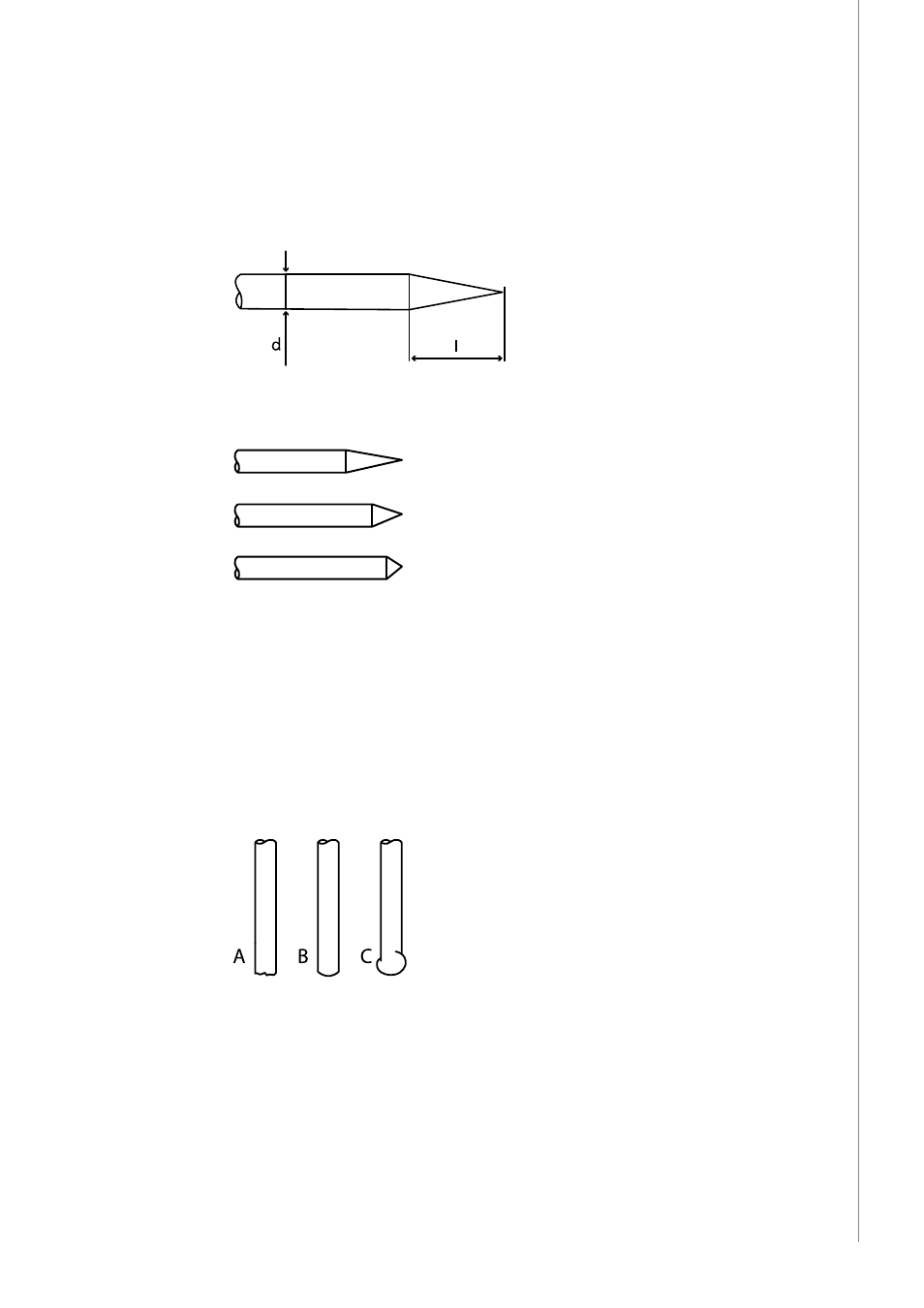
EN
2.5
sharpening OF eleCTrOde
2.5.1 d.C. welding
In D.C. welding the tip of electrode is sharpened into cone shape in order to get a steady
arc and to concentrate heat energy on welding point. Size of sharpening angle has an effect
on width of welding run and depth of penetration. Ratio of sharpening length to electrode
diameter:
I = 1 – 5 x d
Suitable sharpening length depends on welding current which is used most often.
Low currents
Mean currents
High currents
Always make sharpening grinding lengthwise of electrode.
2.5.2 a.C. welding
In A.C. welding the temperature of electrode tip rises a little more higher than melting point of
tungsten and brings about formation of ball-shaped curved surface. On basis of tip formation
and arc behaviour you can determine suitability of welding current for used electrode size and
material.
A.
Low welding current or big electrode size. Arc will be unsteady and is not directed on
welding object.
B.
Suitable current.
C.
Too high current or too small electrode diameter.
You can speed up the tip formation by electrode change e.g. with following:
• Adjust welding current a little higher than usually.
• Burn arc to waste piece by keeping the torch in vertical position.
• Arc is extinguished immediately after the electrode tip has become round.
• Current is reduced to be suitable for work and welding is started.
You can grind the electrode partly at its tip at which the tip will be better ball-shaped and the
arc more steady.
9
TT
C / © Kemppi O
y / 1130