Research Concepts RC2000C User Manual
Page 106
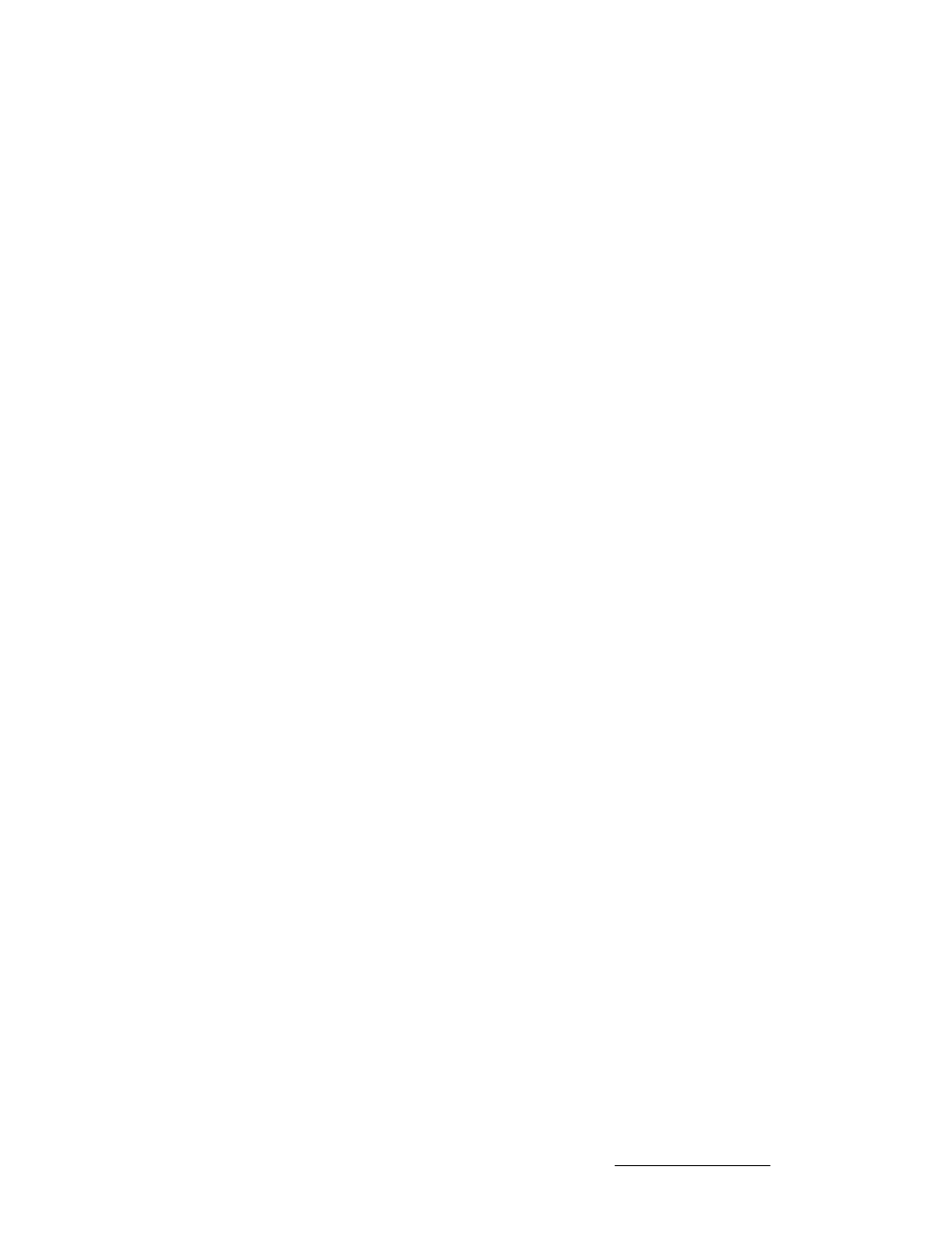
98
RC2000C Az/El Tracking Antenna Controller
Appendix F
AC or Large DC Motors
Research Concepts, Inc. • 5420 Martindale Road • Shawnee, Kansas • 66218-9680 • USA
www.researchconcepts.com
A number of manufacturers make sensors that may be placed directly between the motor and the gear
reducer of the sensor on the C56 flange. Powermation’s #DTK056M1 (phone. 800 811 2691,
www.powermation.com) and Dart's CF Series (phone. 317-873-5211, www.dartcontrols.com) are two
examples. These sensors consist of a Hall effect pickup and a magnet wheel that attaches to the shaft
of the motor via set screws. They are available with several different ‘pulses per revolution’
characteristics. Both of these sensors increase the separation between the motor and the gear reducer
or actuator by 0.750”. In many cases the existing shaft coupling mechanism can accommodate this
extra separation without modification.
Regardless of what type of sensors are used, the user must ensure that the five requirements outlined
above for the sensor waveform are met. Some signal conditioning circuits may be required to meet the
waveform high and low level specification. Note that there is a 5.7-volt supply available on the back of
the antenna controller that is meant to be used with the polarotor. The maximum current draw from this
supply should not exceed 200 milliamps. Also note that shielded cables are required to interface the
antenna controller to the pulse sensors - see the antenna controller manual for more information.
Appropriate cables are available from RCI.
To insure that the pulse duration requirement is not violated, the user should consider the speed of the
motor and the number of pulses produced by the sensor for each revolution of the motor. To determine
the number of pulses per second, take the motor speed in revolutions per minute (rpm) and divide by 60
to get revolutions per second. Multiply this value by the number of pulses per revolution to obtain the
number of pulses per second. To obtain the pulse duration in milliseconds divide 500 by the number of
pulses per second. Mathematically, this formula is ...
PULSE_DURATION (milliseconds) = 30000 / (RPM x PULSES_PER REVOLUTION)
Here is an example:
Motor Speed: 1750 rpm
Pulse Sensor: 1 pulse per revolution
Pulse Duration = 30000 / ( 1750 x 1) = 17.14 milliseconds
To make sure that the total sensor waveform edge count requirement is satisfied, the user must
determine how many revolutions of the motor are required to move from the azimuth ccw limit to the
azimuth cw limit (and from the down to the up limit) along with how many edges are produced for each
revolution of the motor.
With the Powermation and Dart pulse sensors mentioned above, the user can select from the following
the number of pulses per revolution: 1, 2, 15, or 60. The question comes up - how many pulses per
revolution are required? The number of pulses per revolution of the motor determines the resolution
with which the antenna controller can position the antenna. In general, it is sufficient to have 10 position
counts over the antenna’s 3-dB beamwidth. Remember that the controller counts both the rising and
falling edges of each position pulse.
See the section of this paper entitled Pulse Sensor Selection Design Example which gives a step by
step design example for a 6.1 meter Ku band antenna.
Pulse Sensor Selection Design Example
Here is a design example for the azimuth axis of a 6.1 meter antenna (the calculation for the elevation
axis is similar) ...
Antenna Size: 6.1 meters
Operating Frequency: Ku Band (12 GHz)
Azimuth Motor RPM: 1750
Range of antenna azimuth movement: 100 degrees