Sealey TA090 User Manual
Page 13
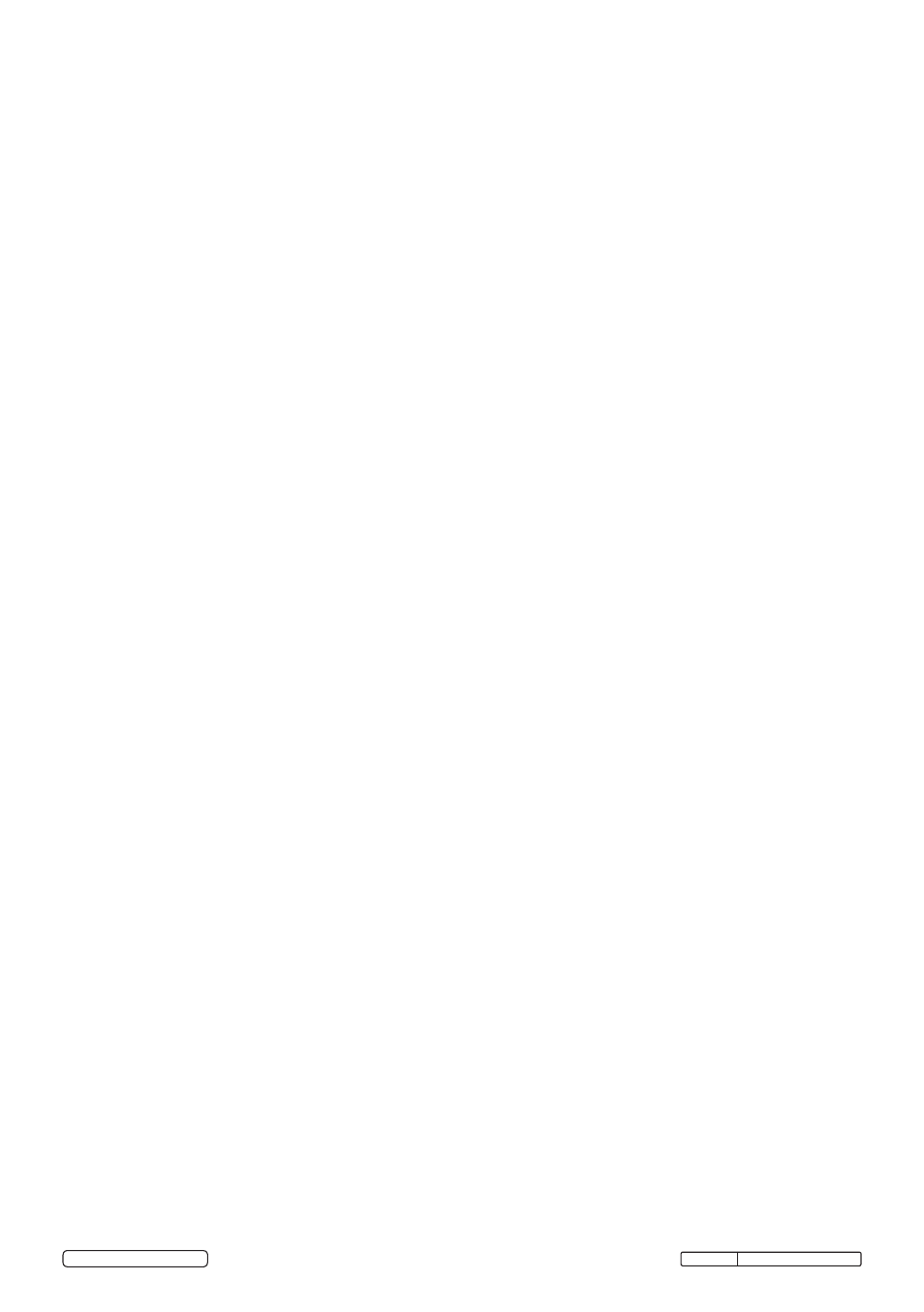
NOTE:
14.9.5 Apply the probe to test sample several times.
14.9.6 The thickness of the foil should be roughly equivalent to the estimated coating thickness.
14.9.7 Even while a series of measurements is being taken, foil calibration can be carried as often as
necessary. The old calibration will be overwritten; the ZERO calibration remains in memory until a
new zero point calibration is made.
14.9.8 See one-point calibration for more information.
14.10 Shot-blasted surfaces
The physical nature of shot-blased surfaces results in coating thickness reading that are too high. The
mean thickness over the peaks can be determined as follows (The statistics program is not of great
benefit in this procedure):
Method A:
14.10.1 The gauge should be calibrated according to 14.8 or 14.9. Use a smooth calibration sample
with the same curvature radius and the same substrate as the later measuring sample.
14.10.2 Now take approx. 10 readings on the uncoated, shot-blased sample to produce the mean
value Xo
14.10.3 After this take approx. 10 further readings on coated, shot blasted test sample to produce the
mean value Xm 4. The difference between the two mean values is the mean coating thickness Xeff
over the peaks. The greater standard deviations of the two values Xm and Xo should also be taken
into consideration: Xeff=(Xm-Xo)±S
Method B:
14.10.4 Carry out a zero calibration of 10 readings on a shot-blased, uncoated sample. Then carry
out a foil calibration on the uncoated substrate. The foil set should consist of a number of individual
foils of max. 50 microns thickness each and should roughly correspond to the estimated coating
thickness.
14.10.5 The coating thickness can be read directly from display and should be averaged from 5 to 10
single measurements. The statistics function is useful here.
Method C:
This method also gives reliable results. Simply follow the two-point calibration method using two foils
as described in section 14.9. For a maximum approach to the respective nature of surface, the foil
value can be reached by using several foils – 50um each. The mean coating thickness should be
calculated from 5 to 10 readings. The statistics program is very useful here.
NOTE:
For coatings thicker than 300 um, the influence of roughness generally is of no importance and it will
not be necessary to apply above calibration methods.
14.11 General Remarks on Measurement
After careful calibration has been made, all subsequent measurements will lie within the guaranteed
measuring tolerance. Strong magnetic fields near generators or live rails with strong currents can
affect the reading.
When using the statistics program for obtaining a mean value it is advisable to place the probe
several times at a typical measuring spot. Any false readings can be removed immediately Via the
MENU system.
The final reading derives from the statistical calculation and from the guaranteed tolerance levels of
the gauge.
Coating Thickness D =X±s±u
Example: Readings: 150um, 156um, 153um
Mean value: X=153um
Standard deviation: s=±3um
Measuring uncertainty: u=±(1% of reading + 1um)
D= 153±3±(1,53um+1um)
=153±5,5um
MAX: maximum reading
MIN: minimum reading
Original Language Version
TA090 Issue No.1 25/10/12
© Jack Sealey Limited